Українською
  In English
Feed aggregator
Empowering the Next Generation: ESSCI’s Role in Promoting E-Mobility and Battery Technology Skills
Author : Saleem Ahmed, Officiating Head, ESSCI
India is undergoing a significant transformation in its transportation sector, with electric vehicles at the forefront of this revolution. The government’s proactive initiatives, such as the Faster Adoption and Manufacturing of Electric Vehicles scheme and the Production Linked Incentive program for Advanced Chemistry Cell battery manufacturing, underscore a strong commitment to sustainable mobility. These efforts aim to achieve a 30% EV market share by 2030, a goal that necessitates a highly skilled workforce proficient in battery technology and e-mobility systems.
ESSCI’s Targeted Training Programs for E-Mobility
To address the burgeoning demand for skilled professionals in the EV sector, the Electronics Sector Skills Council of India has developed specialized training programs. These programs are meticulously designed to equip learners with industry-relevant expertise, preparing them for roles in manufacturing, design, and maintenance within the e-mobility ecosystem.
One of ESSCI’s flagship qualifications is the Battery System Assembly Operator (ELE/Q6604) program.
This course focuses on training individuals in the precise assembly of battery packs, emphasizing a comprehensive understanding of battery construction, adherence to safety protocols, and stringent quality control measures. Given that battery packs constitute a significant portion of an EV’s total cost, their proper assembly is crucial for both performance and affordability.For those inclined towards innovation and design, the Battery System Design Engineer (ELE/Q6701) qualification offers a robust foundation in battery architecture, chemistry, and optimization techniques.
Participants are trained to develop high-performance energy storage systems that enhance efficiency, extend battery lifespan, and minimize environmental impact. As India progresses towards advanced battery technologies, expertise in battery design becomes indispensable for realizing the nation’s e-mobility objectives.
Equally vital to the EV ecosystem is the Battery System Repair Technician (ELE/Q7001) program. This course concentrates on diagnosing, troubleshooting, and repairing battery systems. As battery degradation over time can affect vehicle performance and range, skilled repair technicians are essential to sustaining India’s EV adoption. The program ensures that professionals are proficient in battery diagnostics, cell balancing, thermal management, and safety protocols—skills that are increasingly in demand as India’s EV repair and servicing sector expands.
Collaborations and Industry Integration
To enhance practical learning, ESSCI collaborates with industry leaders and academic institutions, ensuring that its training programs align with the latest technological advancements and market demands. A notable initiative is ESSCI’s partnership with ABB India, which led to the establishment of a Smart Electrician Training Centre in Faridabad, Haryana. This center provides hands-on training in modern electrical systems, smart grid technologies, and EV charging infrastructure, equipping technicians with real-world expertise.
Additionally, ESSCI actively engages with automotive manufacturers, battery producers, and energy storage companies to integrate their insights into curriculum development. Collaborations with companies involved in lithium-ion battery manufacturing, battery recycling, and charging infrastructure development ensure that the training programs remain pertinent to industry needs. These partnerships also facilitate job placements for trainees, bridging the gap between skill acquisition and employment.
Rising Demand for E-Mobility Professionals in India
The Indian EV market is experiencing exponential growth, with projections estimating a Compound Annual Growth Rate of 49% from 2022 to 2030.This surge is driven by supportive government policies, increasing environmental awareness, and technological advancements. The adoption of EVs is anticipated to generate approximately 5 million direct and indirect jobs in India by 2030, with a significant portion of these roles emerging in battery technology, EV servicing, and charging infrastructure.
Furthermore, the lithium-ion battery market in India is expected to reach substantial capacity by 2030, propelled by the escalating demand from the EV sector. This trend underscores the urgent need for skilled professionals capable of developing, maintaining, and optimizing battery systems for electric vehicles, energy storage solutions, and grid stabilization.
The Road Ahead: Preparing India’s Workforce for the E-Mobility Revolution
ESSCI’s emphasis on future-ready skill development is instrumental in India’s journey toward sustainable mobility. By aligning its training programs with evolving industry trends, ESSCI addresses the immediate demand for skilled professionals and prepares the next generation for long-term career opportunities in e-mobility and battery technology.
With continued government support, industry collaborations, and advancements in battery research, India is well-positioned to become a global leader in electric mobility. However, achieving this vision requires a robust skilling ecosystem that empowers individuals with the expertise needed to drive innovation and ensure the reliability of EV technology.
Through its specialized training initiatives, ESSCI is effectively bridging the skill gap, enhancing employability, and contributing to India’s clean energy goals. As the demand for battery engineers, EV service technicians, and energy storage specialists continues to rise, ESSCI’s programs will remain integral to shaping the future of e-mobility in India.
The post Empowering the Next Generation: ESSCI’s Role in Promoting E-Mobility and Battery Technology Skills appeared first on ELE Times.
Nuvoton NuMicro MA35D1 Microprocessor Dual-OS Solution: Revolutionizing Industrial Automation and AIoT Applications
Nuvoton Technology’s NuMicro MA35D1 is a high-performance, dual-core Arm Cortex-A35 microprocessor capable of running both RTOS and Linux simultaneously. In the latest application demonstration, it delivers instant boot-up within one second, real-time control, and versatile application support by leveraging the strengths of both operating systems.
Linux excels in networking, multimedia, and multitasking, offering rich software tools and broad hardware compatibility that simplifies integration, while RTOS ensures stable and predictable response times for real-time industrial control scenarios. To meet diverse application demands, the MA35D1 maximizes performance and efficiency, making it an ideal solution for industrial automation, AIoT applications, smart buildings, home appliances.
Key Features
- Dual-OS Support: Runs RTOS and Linux simultaneously for optimal performance in real-time applications.
- Instant Boot-Up: Instantly operational within 1 second for mission-critical applications.
- Immediate Data Processing: Rapid sensor data acquisition and LCD display updates.
- Enhanced UI Experience: Powered by Qt for MCUs, the UI provides high-quality and smooth user interface experience.
- Networking Features: Smart devices can connect to the built-in MA35D1 web server for real-time monitoring and remote control.
Technical Specifications
- Processor: Dual-core 64-bit Cortex-A35, 800 MHz and Cortex-M4
- Memory: Multi-chip package (MCP) DDR SDRAM up to 512 MB
- Security Features: Integrated Nuvoton Trusted Secure Island (TSI) to enhance system security
- Multimedia: JPEG/H.264 decoder, TFT-LCD resolution up to 1080p
- Connectivity: 2 sets of Gigabit Ethernet, high-speed USB, SDIO 3.0, 4 sets of CAN FD, and 16 sets of UART
The post Nuvoton NuMicro MA35D1 Microprocessor Dual-OS Solution: Revolutionizing Industrial Automation and AIoT Applications appeared first on ELE Times.
IQE and X-FAB sign JDA to develop European-based GaN power outsourced manufacturing platform
Navitas & GigaDevice partner to combine power & control for high-frequency, high-efficiency & high-density power platforms
📢 Набір на групи з танцювально-рухової терапії "Танець стихій" для студентства та працівників
Готовий_а бути в моменті? У світі, де ми часто відчуваємо стрес і тривожність, важливо навчитися бути тут і зараз, відчувати себе, своє тіло та емоції. Заняття з танцювально-рухової терапії (ТРТ) допоможуть знайти внутрішній спокій і навчитись реагувати на виклики без страху та зайвої напруги.
Візит делегації КПІ ім. Ігоря Сікорського до Франції
🇫🇷 Розпочинаємо серію дописів щодо візиту делегації КПІ ім. Ігоря Сікорського до університетів і науково-дослідних установ Франції для налагодження та посилення подальшої співпраці.
Unlocking the Potential of 6G FR3
Courtesy: Keysight
6G aims to connect the physical, digital, and human worlds through emerging technology focusing on new spectrum utilization, artificial intelligence integration into networks and devices, digital twins, and new network architectures. These elements enhance network programmability and automation across various 6G use cases.
While the commercial deployment of 6G seems quite far away, the research needs for 6G are already here, including growing efforts around the spectrum. New frequency ranges are needed to satisfy the bandwidth needs of the ever-growing throughput requirements. Frequency range 3, or FR3, is one of the new spectrum ranges where 6G is evolving. There were only two frequency ranges for 5G: FR1 and FR2. FR3 is between FR1, often referred to as sub-6 GHz, and FR2, the so-called millimeter-wave range, between 7 and 24 GHz.
6G Requirements : A Drive Towards Deterministic Channel Models4G and 5G addressed radio channel modeling requirements using geometry-based stochastic channel models (GSCMs) for simulating and testing massive multiple-input and multiple-output (mMIMO) systems. However, 6G use cases and technologies are generating new requirements for radio channel modeling because of:
- Near-field (NF) and short-range communications using smaller cells.
- The need for accurate location-based services.
- Smart environments with multiple radio access technologies.
- Propagation challenges at sub-terahertz (THz) frequencies.
- Flexible adaptation and enhanced environmental awareness.
- Integrated sensing and communication (ISAC) and extreme MIMO (xMIMO).
Antenna arrays with substantial apertures are under investigation in the 6G FR3 band for MIMO technologies, including MIMO, mMIMO, and xMIMO. xMIMO antenna arrays support narrow pencil beams and more MIMO layers than conventional mMIMO. Figure 1 shows an example of extreme hybrid beamforming, FR3 upper mid-band base station. As a result, the design and validation of xMIMO wireless systems necessitate accurate intra- and inter-cluster angular characteristics from the channel model.
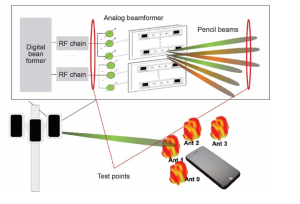
Ensuring that the channel model accurately captures the intra- and inter-cluster angular characteristics is essential when conducting system simulations or testing the actual performance of xMIMO base stations in RAN and Open RAN configurations. In addition, dynamic channel models are necessary for evaluating beam management and precoding adaptation over user equipment movement. These channel models consider transitions between line-of-sight / non-line-of-sight and blockage conditions.
However, the current 3GPP GSCM channel models lack the accuracy needed to develop extreme beamforming algorithms with highly directive pencil beams. To address that, a new 3GPP RP-234018 Release 19 technical study item on channel modeling enhancements for 7 to 24 GHz for New Radio (NR) was initiated.
To test the upper mid-band for FR3, test engineers need:
- Phase and time coherent multichannel emulation.
- Semi-deterministic and/or deterministic channel models.
- Accurately calibrated equipment for phase and amplitude measurements.
- Comprehensive measurement and analysis tools.
6G FR3 system testing requires phase and time-coherent multichannel emulation using semi-deterministic and deterministic channel models. From the physical layer (PHY) to the application layer, key performance metrics for 6G FR3 testing include:
- Beam weight estimation and pointing metrics.
- Beam shape and gain.
- Sidelobe levels.
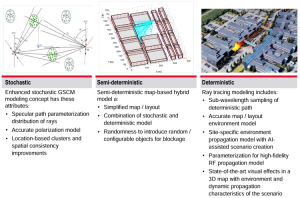
With a robust channel emulation solution, test engineers can reproduce a diverse propagation environment and emulate hardware impairments like phase noise and interference. They will need:
- Channel emulation capabilities to create realistic and highly accurate 6G FR3 environment models.
- Signal generation capabilities to provide the necessary 6G transmit waveform to the channel emulator.
- Performance metrics, including beamforming gain, beam width, and sidelobe levels.
- Software tools to perform phase and time-coherent multichannel emulation and create geometry-based stochastic channel models.
- Testing environment to reproduce propagation environments and ensure comprehensive testing.
Keysight 6G FR3 system test solution includes a channel emulator, channel emulation software, and an MXG signal generator.This solution creates realistic and highly accurate stochastic and deterministic models for mimicking 6G FR3 components and systems. The MXG signal generator provides the signal input to the FR3-capable channel emulator. The channel emulator also supports ISAC for detecting and tracking objects.
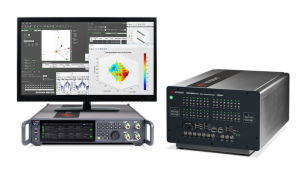
Precise channel emulation is crucial for 6G FR3. Accurate channel models are needed to support advanced 6G features and allow for realistic testing of 6G technologies, such as mMIMO and beamforming, under various conditions to understand how these technologies will perform in real-world scenarios. Additionally, it supports advanced use cases like ISAC, which require detailed knowledge of the channel characteristics to function effectively.
Be prepared for 6G and the challenges it brings onboard and accelerate your 6G prototyping before releasing standards using Keysight solutions for channel modeling and emulation for FR3 MIMO, mMIMO, xMIMO, and ISAC.
The post Unlocking the Potential of 6G FR3 appeared first on ELE Times.
NVIDIA Accelerated Quantum Research Center to Bring Quantum Computing Closer
Courtesy: Nvidia
As quantum computers continue to develop, they will integrate with AI supercomputers to form accelerated quantum supercomputers capable of solving some of the world’s hardest problems.
Integrating quantum processing units into AI supercomputers is key for developing new applications, helping unlock breakthroughs critical to running future quantum hardware and enabling developments in quantum error correction and device control.
The NVIDIA Accelerated Quantum Research Center, or NVAQC, announced today at the NVIDIA GTC global AI conference, is where these developments will happen. With an NVIDIA GB200 NVL72 system and the NVIDIA Quantum-2 InfiniBand networking platform, the facility will house a supercomputer with 576 NVIDIA Blackwell GPUs dedicated to quantum computing research. “The NVAQC draws on much-needed and long-sought-after tools for scaling quantum computing to next-generation devices,” said Tim Costa, senior director of computer-aided engineering, quantum and CUDA-X at NVIDIA. “The center will be a place for large-scale simulations of quantum algorithms and hardware, tight integration of quantum processors, and both training and deployment of AI models for quantum.”
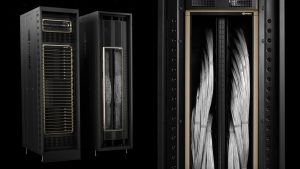
Quantum computing innovators like Quantinuum, QuEra and Quantum Machines, along with academic partners from the Harvard Quantum Initiative and the Engineering Quantum Systems group at the MIT Center for Quantum Engineering, will work on projects with NVIDIA at the center to explore how AI supercomputing can accelerate the path toward quantum computing.
“The NVAQC is a powerful tool that will be instrumental in ushering in the next generation of research across the entire quantum ecosystem,” said William Oliver, professor of electrical engineering and computer science, and of physics, leader of the EQuS group and director of the MIT Center for Quantum Engineering. “NVIDIA is a critical partner for realizing useful quantum computing.”
There are several key quantum computing challenges where the NVAQC is already set to have a dramatic impact.
Protecting Qubits With AI Supercomputing
Qubit interactions are a double-edged sword. While qubits must interact with their surroundings to be controlled and measured, these same interactions are also a source of noise — unwanted disturbances that affect the accuracy of quantum calculations. Quantum algorithms can only work if the resulting noise is kept in check.
Quantum error correction provides a solution, encoding noiseless, logical qubits within many noisy, physical qubits. By processing the outputs from repeated measurements on these noisy qubits, it’s possible to identify, track and correct qubit errors — all without destroying the delicate quantum information needed by a computation.
The process of figuring out where errors occurred and what corrections to apply is called decoding. Decoding is an extremely difficult task that must be performed by a conventional computer within a narrow time frame to prevent noise from snowballing out of control.
A key goal of the NVAQC will be exploring how AI supercomputing can accelerate decoding. Studying how to collocate quantum hardware within the center will allow the development of low-latency, parallelized and AI-enhanced decoders, running on NVIDIA GB200 Grace Blackwell Superchips.The NVAQC will also tackle other challenges in quantum error correction. QuEra will work with NVIDIA to accelerate its search for new, improved quantum error correction codes, assessing the performance of candidate codes through demanding simulations of complex quantum circuits.
“The NVAQC will be an essential tool for discovering, testing and refining new quantum error correction codes and decoders capable of bringing the whole industry closer to useful quantum computing,” said Mikhail Lukin, Joshua and Beth Friedman University Professor at Harvard and a codirector of the Harvard Quantum Initiative.
Developing Applications for Accelerated Quantum Supercomputers
The majority of useful quantum algorithms draw equally from classical and quantum computing resources, ultimately requiring an accelerated quantum supercomputer that unifies both kinds of hardware.
For example, the output of classical supercomputers is often needed to prime quantum computations. The NVAQC provides the heterogeneous compute infrastructure needed for research on developing and improving such hybrid algorithms.
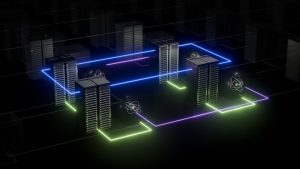
New AI-based compilation techniques will also be explored at the NVAQC, with the potential to accelerate the runtime of all quantum algorithms, including through work with Quantinuum. Quantinuum will build on its previous integration work with NVIDIA, offering its hardware and emulators through the NVIDIA CUDA-Q platform. Users of CUDA-Q are currently offered access to Quantinuum’s System H1 QPU hardware and emulator for 90 days.
“We’re excited to collaborate with NVIDIA at this center,” said Rajeeb Hazra, president and CEO of Quantinuum. “By combining Quantinuum’s powerful quantum systems with NVIDIA’s cutting-edge accelerated computing, we’re pushing the boundaries of hybrid quantum-classical computing and unlocking exciting new possibilities.”
QPU Integration
Integrating quantum hardware with AI supercomputing is one of the major remaining hurdles on the path to running useful quantum hardware.
The requirements of such an integration can be extremely demanding. The decoding required by quantum error correction can only function if data from millions of qubits can be sent between quantum and classical hardware at ultralow latencies.
Quantum Machines will work with NVIDIA at the NVAQC to develop and hone new controller technologies supporting rapid, high-bandwidth interfaces between quantum processors and GB200 superchips.
“We’re excited to see NVIDIA’s growing commitment to accelerating the realization of useful quantum computers, providing researchers with the most advanced infrastructure to push the boundaries of quantum-classical computing,” said Itamar Sivan, CEO of Quantum Machines.
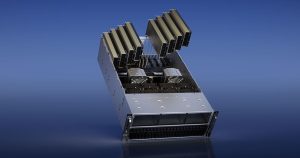
Key to integrating quantum and classical hardware is a platform that lets researchers and developers quickly shift context between these two disparate computing paradigms within a single application. The NVIDIA CUDA-Q platform will be the entry point for researchers to harness the NVAQC’s quantum-classical integration.
Building on tools like NVIDIA DGX Quantum — a reference architecture for integrating quantum and classical hardware — and CUDA-Q, the NVAQC is set to be an epicenter for next-generation developments in quantum computing, seeding the evolution of qubits into impactful quantum computers.
The post NVIDIA Accelerated Quantum Research Center to Bring Quantum Computing Closer appeared first on ELE Times.
A high-performance current source

The ever innovative and prolific Mr. Woodward has offered “PWM-programmed LM317 constant current source,” an intriguing programmable constant current source which elicited a lively conversation in its comments section. A Zen paradox arose: if the addition of a capacitor between ground and the LM317 ADJ pin reduces the power supply-induced ripple current delivered to the load while also reducing the impedance seen by the load (making it a less “Ideal” current source), is it a better or worse “constant current source”? To answer the question, it must also be considered that the capacitor also slows the response to load current changes which result from alteration of the PWM duty cycle. In the end, the answer depends on the application. But I’m sure a Zen master would have a better answer to the question than “it depends.”
Wow the engineering world with your unique design: Design Ideas Submission Guide
Even without the capacitor, the time constant and non-linear nature of the design idea’s (DI’s) PWM-driven circuit has limitations if used as a source of AC signals. Of course, the title of the DI makes it clear that supplying AC current to the load was not a performance goal. But one of the commenters was interested in delivering both AC and DC currents.
Basic LM317 current sourceI wondered if the subcircuit consisting of the LM317 and resistors Rs and Rc could form the basis for such a circuit if it were driven from a suitable control current. In Figure 1, the first step to investigating this was to simulate a basic LM317 current source [1] made of U1 and Rs1 to drive load RL1. The load current is 10 mA.
Figure 1 A series of LM317 circuits investigated in simulation and on the test bench for suitability as a current source.
The circuit’s broadband PSRR was simulated, measured in ohms, and defined as the ratio of the AC voltage of the V1 supply to the AC current through RL1. From DC to almost 1 kHz, the result was a little over 100 kΩ, falling to a bit below 10kΩ at 10kHz. So far, so good. Next, the candidate subcircuit containing U2 was tested. Ideal infinite impedance DC current source I1 (chosen to ensure no degradation of subcircuit performance) arranged for RL2 to also receive 10 mA DC. I expected pretty much the same PSRR here. But to my surprise, the DC to 1kHz impedance had fallen to a little under 2 kΩ and to a bit more than 100 Ω at 10 kHz!
Looking closer, there was no current at all flowing through the LM317 ADJ pin, not even the datasheet’s nominal 50 µA DC. As a result, nor was there any AC current flowing through either Rc2 or the ADJ to explain the PSRR drop. Clearly, the LM317 file [2] I was using for simulation was not suitable for testing PSRR. There are other files from the site listed in the footnote which I’ll investigate at a later date, but for now I decided instead to do some good old lab bench tests.
Bench TestsThe circuit I’ve bench-tested for PSRR is the one which has U3 as its central element. The result was much closer to but also better than the simulated U1: 500 kΩ from DC to 1 kHz, falling to 360 kΩ at 10 kHz and 80 kΩ at 50 kHz. But while I was on the bench, I started to look closely at some other things.
The U3 circuit works by subtracting a voltage drop, Vdrop, across Rc3 from the LM317’s Vref (the voltage difference between OUT and ADJ) and applying Vref – Vdrop across Rs3. Careful attention must be paid to the accuracy of Vdrop, which is challenge enough. But then there is Vref; what are its limits?
I decided to make some DC measurements. I have eight Texas Instruments LM317KCS IC’s (TO-220 package), all with same date code marking. Using the U4 circuit, I measured the Vo (OUT) of each of them with V4 set to 12 VDC. Vo ranged from 1.243 V to 1.263 V, a 20-mV difference. For one of them, I set V4 to 15 V for 5 minutes, and then to 25 V for the same time period.
After these time intervals elapsed, the measurements revealed a drop of 27 mV in Vo. This is more than the 5 mV at 25°C that comes from the spec’s line regulation of .04% per 1-V line voltage change. So, I rechecked my measurements but got the same result. From all these measurements, it’s impossible to determine the limits of Vref over different IC’s, load currents, DC input voltages, and junction temperatures of an arbitrary circuit. Then of course, there’s Noah’s revenge: every 40 days the long-term stability parameter could gift us with a 1% of Vref shift: 12.5 mV. Looking at all of this, I settled on the spec’s reference voltage limit of 1.25 V ± 50 mV for Vref. So what is the impact of this ambiguity?
ImplicationsWe do want a programmable supply, so let’s stick with the U2 configuration and defer considerations for a practical programmable current source in place of I1. Regardless of the resistor values, the current that that circuit delivers to the load is:
ILoad = Vref / Rs + (Iadj – I1) * Rc / Rs
The maximum value of ILoad, Imax, occurs when I1 is zero. When the circuit is asked to deliver Imax/10, (Iadj – I1) * Rc will ideally be set to about .9 * Vref. But now ILoad is equal to 125 ± 50mV; a ± 40% variation! Things get worse if less than Imax/10 is required. I welcome suggestions as to how to deal with the limited accuracy and operational range seen here. But for now, let’s consider the Figure 2 circuit.
Figure 2 Darlington Q1/Q2 feeds 0-Ω load, V_LOAD, with a current. R2, R5, R4 and C2 establish stability and should be checked in assembled circuits. R1 establishes the minimum Q1 DC bias.
In Figure 2, V_Supply provides power at 12 VDC. V_IN takes on DC voltages of 10, 100 and 1000 mV to produce DC currents of 10, 100 and 1000 mA through V_LOAD. Each voltage source in the schematic produces a sine wave at a frequency of 1, 10, 100, 1000 or 10000 Hz to test PSRR (Figure 3), output impedance (Figure 4), and signal transfer (Figure 5); but only one sinusoidal source is active at a time.
Sine amplitudes for V_LOAD and V_Supply when active are 1-V peak, whereas that for V_IN is 1 mV; so that when summed with the three different DC voltages that V_IN takes on, the net voltage and current will remain positive. All simulation measurements are of currents through V_LOAD. Table 1 lists the simulated verses desired DC currents flowing through that load.
Figure 3 The PSRR impedances in ohms verses frequency as seen by V_LOAD for three different DC currents. Higher impedances are associated with more nearly ideal current sources. (The dots on the curves represent simulation measurements.)
Figure 4 The Impedance in ohms seen by V_LOAD at three different DC currents. Higher impedances are associated with more nearly ideal current sources. The dots on the curves represent simulation measurements.
Figure 5 Transfer impedances in ohms verses frequency from V_IN to V_LOAD. The design goal is a value of 1.0000. The dots on the curves represent simulation measurements.
DESIRED CURRENT, mA |
V_FET_OUT CURRENT, mA |
10 |
10.011 |
100 |
100.009 |
1000 |
999.987 |
Table 1 Desired and simulated DC currents for the circuit. Op-amp input offset voltages and other aspects of the circuit will contribute errors not accounted for here.
The AD4084-2 op-amp has a worst-case input offset voltage of 300 µV. The two of them could together contribute up to ± 600 µA in error to the load. There are also the tolerances of resistors Rc1, Rc2 and RsM to consider. The limited beta of the 2N3906 could “steal” up to 10 µA from the load; replacing it with the BC857C could significantly reduce that number. And I have conveniently avoided discussing how to generate the signals produced by the voltage source V_IN, which undoubtedly will contribute their own accuracy errors. But the goal of this DI was to investigate potential power current sources capable of handling both AC and DC currents, and I believe that what was presented here is a candidate that is worth consideration for that.
Christopher Paul has worked in various engineering positions in the communications industry for over 40 years.
Related Content
- PWM-programmed LM317 constant current source
- 1 A, 20 V PWM DAC current source with tracking preregulator
- Optimizing a simple analog filter for any PWM
- A class of programmable rheostats
- LM317 smooths but doesn’t regulate
References
- https://www.ti.com/product/LM317#tech-docs See Figure 18 of the LM317 datasheet accessible from this site.
- https://groups.io/g/LTspice/filessearch?p=created%2C%2C%2C20%2C2%2C0%2C0&q=lm317, LM317A_002.zip
The post A high-performance current source appeared first on EDN.
До зеленої трансформації спільно з Асоціацією професіоналів довкілля (PAEW)
Робитимемо спільні кроки до зеленої трансформації нашої держави спільно з Асоціацією професіоналів довкілля (PAEW) — організацією, що обʼєднує понад 7 тисяч топових енвайронменталістів, науковців і практиків (інженерів, юристів, підприємців), які реалізують ефективні реформи у сфері охорони довкі
FPGA learning made easy with a virtual university program

Altera University aims to affordably and easily introduce students to the world of FPGAs and digital logic programming tools by unveiling the curriculum, tutorials, and lab exercises that bridge the gap between academia and real-world design work. The program comprises four courses focused on digital logic, digital systems, computer organization, and embedded systems.
This university program will offer professors, researchers, and students access to a broad collection of pre-developed curricula, software tools, and programmable hardware to help accelerate the FPGA learning experience. Moreover, professors can restructure the lab work with pre-developed curricula and hands-on lab kits.
The program aims to accelerate the FPGA learning experience by making available a broad collection of pre-developed curricula, software tools, and programmable hardware. Source: Altera
“We established Altera University with the singular goal of training the next generation of FPGA developers with both the AI and logic development skills needed to thrive in today’s modern workforce,” said Deepali Trehan, head of product management and marketing at Altera. “Through Altera University, we’re enabling professors to bring real-world experiences to their students using cutting-edge programmable solutions.”
Altera is also offering discounts on select FPGAs for developing custom hardware solutions. Then there is a 20% discount on select Agilex 7 FPGA-based development kits. The company also offers a 50% discount on using LabsLand, a remote laboratory with access to Altera FPGAs.
Altera University also offers higher-level FPGA courses that include an AI curriculum to ensure that students can stay aligned with the latest industry trends and develop an understanding of usage models for FPGAs in the AI workflow.
Altera University’s academic program website provides more information on curricula, software tools, and programmable hardware.
Related Content
- All About FPGAs
- FPGAs for beginners
- Power-aware FPGA design
- FPGA programming step by step
- Embedded design with FPGAs: Development process
The post FPGA learning made easy with a virtual university program appeared first on EDN.
ST’s Automotive MCU technology for next-generation vehicles
Author: STMicroelectronics
ST has been serving customers in the automotive market for over 30 years and provides them with a range of products and solutions covering most applications in a typical vehicle. As the market has evolved, so has ST’s offering, a key part of which is automotive microcontrollers (MCUs).
ST pioneered embedded non-volatile memory (eNVM) with ST10 and then introduced automotive microcontrollers with its SPC5 range based on PowerPC architecture, shipping more than one billion MCUs in automotive. Cost-effective automotive controllers from the STM8 family complemented this offer.
ST’s Stellar FamilyST’s latest generation of automotive microcontrollers is the Stellar family, which is the industry’s first Arm®-based portfolio that spans the entire automotive MCU spectrum, from low-end to high-end solutions. These advanced microcontrollers reduce complexity, ensure safety and security, and deliver optimal performance and efficiency of next-gen vehicle architectures and features. Customers can benefit from shorter development times and focus on bringing innovation and differentiation for their software-defined vehicles (SDVs) in this highly competitive market. For these reasons Stellar products are gaining momentum, particularly among our customers in Asia and Europe.
Stellar is the industry’s first family of emerging technologies after eFlash, representing the most mature and smallest memory cell automotive grade solution on the market. The Stellar family is optimized for electrification, including X-in-1 vehicle motion control computing, new vehicle architectures, zonal and domains, and safety MCUs for safety-critical subsystems, such as ADAS.
It fully supports automotive transformation by integrating multiple functions safely into a single device and allowing the continuous integration of new features in vehicles. This is made possible with key technologies, including a right choice of core technology, virtualization, Ethernet support and ground-breaking memory technology embedded in the automotive MCUs–a game changer for customers faces challenges with application memory sizing.
Stellar MCUs are based on Arm® Cortex®-R52+ technology. This high-performance processor delivers real-time virtualization support for time-critical secure and safety systems. It can run multiple applications simultaneously with freedom from interference. And thanks to fully programmable auxiliary cores it is possible to accelerate specific functions, such as routing, low power management, digital filtering while offloading the main cores.
“As the driver experience continues to evolve in the age of AI and software-defined vehicles, advancing automotive functional safety, flexibility and real-time performance capabilities is essential,” said Dipti Vachani, senior vice president and general manager, Automotive Line of Business, Arm. “Built on Arm, the Stellar microcontroller family taps into the Arm compute platform’s advanced safety and real-time features, as well as the broad Arm software ecosystem. This enables car manufacturers to comply with strict safety regulations while implementing innovative features that keep them at the forefront of the automotive industry.”
Stellar MCUs enable the introduction of ethernet capabilities in vehicles and is the first ST MCU embedding an Ethernet switch. Thanks to Ethernet, data exchange is more efficient, and flexible, supporting the needed gigabit throughput, with a higher level of security. By supporting various in-vehicle communication topologies, such as Ethernet ring, automotive MCUs fulfill the promise of halving the length of the cross-car wiring cables and manufacturing costs.
Phase Change Memory is set to redefine what is possible in vehicle softwareStellar MCUs, with the embedded Phase Change Memory (PCM) technology and its flexibility, transform the process of Over-the-Air (OTA) updates. In the automotive industry, OTA updates are crucial for adding new features and safety or security patches without physical intervention. However, this flexibility often requires careful consideration of future memory needs, which can lead to increased costs and complex planning.
ST’s PCM innovation is no ordinary memory. Not only is it the industry’s smallest memory cell for automotive MCU, but it is pioneering a transformative breakthrough in automotive and set to redefine what is possible in vehicle software. Thanks to ST’s innovative PCM technology, memory capabilities are reaching a new level of sophistication. This is not just about memory performance. It is a forward-thinking solution that brings adaptability and lasting value to the automotive landscape enabling the final developers to continuously improve and upgrade functions.
As vehicles become increasingly software-defined, the ability to introduce new features and enhancements is essential. PCM’s groundbreaking technology will support the shift toward more adaptable, future-focused vehicles, giving automakers new ways to refine experiences as vehicles continue to advance.
Additionally, PCM delivers the ability to support uninterrupted OTA updates. PCM securely stores updates without impacting the vehicle’s current operations. Thanks to concurrent read and write capabilities, the new software download does not interfere with the application code already running on the MCU, ensuring continuous performance during the update process.
Stellar P, designed for the integration of multiple functions, and Stellar G, for the realization of Software-Defined Vehicles (SDV) zonal controllers, are two series leveraging ST’s internally developed eNVM. They are built on 28nm FD-SOI technology, allowing them to achieve maximum frequency with lower power consumption and enhanced radiation immunity. Stellar is the first 28nm product certified for functional safety and will enter production by the end of this year.
The Stellar family also enables the X-in-1 growing trend toward more affordable electromobility, with the decisive switch from fossil to electrically powered vehicles. X-in-1 powertrain solutions combine multiple components into a single ECU, allowing manufacturers to create efficient, compact, and cost-effective performing vehicles.
Stellar offers scalable X-in-1 implementation, accommodating a growing number of ECUs from low to high integration levels. This solution supports increasingly complex X-in-1 systems by providing enhanced availability of cores, analog components, and I/O capabilities.
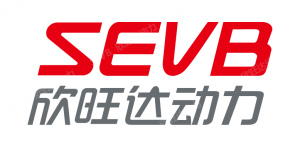
“As a global leader in lithium-ion batteries, Sunwoda provides stable and reliable electronic system solutions for automotive suppliers worldwide. Our new collaboration with STMicroelectronics focuses on developing solutions using ST’s advanced Stellar microcontrollers and proprietary production processes, which primarily include battery management systems, and VDC/Zonal and body control functions. Together, we aim to provide intelligent solutions that enhance the next generation of energy vehicles in China and globally,” said Wang Mingwang, founder, Sunwoda.
2. FD-SOI technology to achieve the max possible frequency at the lower power consumption and to strengthen radiation immunity
3. New powerful over-the-air methodology and true EEPROM capabilities
4. A set of ethernet-related IPs (MAC, MACSec, switches) that enable distribution of high volume data, allow different topologies of in-vehicle communication, and reduce the vehicle manufacturing cost
5. Fully programmable auxiliary cores that accelerate specific functions such as routing, low power management, digital filtering while offloading the main cores
As part of the expanded roadmap for automotive MCUs, ST will introduce its market-leading general-purpose STM32 microcontroller platform to the automotive sector. The STM32 platform is well recognized for its cost optimization, simplicity, and reliability. Augmented with automotive grade quality and safety, STM32A will achieve up to ASIL B standards. This platform will be designed to handle edge actuation, from the simplest functions to more sophisticated single tasks, all at optimized costs. It will be particularly well-suited for applications like motor control in vehicle systems, including windows, mirrors, and roofs.
Best of industrial and automotive worlds: towards converged futureOver time, the convergence of the industrial and automotive hardware and software platforms will combine the best of both worlds. Automotive brings strong security expertise and industrial is built on strong Internet of Things and artificial intelligence solutions. The converged future will share hardware technologies, cores, and a common ecosystem of tools and software support. Such convergence will enable customers to seamlessly transition between solutions, offering simplification and full scalability to innovate faster.
Edge AI technology is one example where we see what is being adopted now in industrial applications benefiting automotive in the future. Neural accelerator technology and the associated tools that enable developers to easily implement AI in their applications, whatever their level of data science expertise, will enhance automotive systems in the future. ST has spent approximately 10 years investing in the development of microcontrollers, smart sensors, and AI software tools to meet the needs of our customers and harness the power of edge AI.
While AI adoption in automotive—beyond autonomous driving—is still in its initial stages, there are emerging trends of promising use cases for system optimization, energy efficiency, and problem-solving. For example, virtual sensors can measure rotor temperatures, and predictive maintenance can ensure vehicle reliability. As the number of sensors in vehicles heavily increases, AI will play a key role in virtualizing many of them, further enhancing automotive performance. Security is another area where we see the convergence of industrial and automotive bringing significant benefits.
This future will be based on the most advanced and more efficient 18nm process technologies. ST’s advanced technology portfolio for automotive MCUs spans from 40 to 28 to 18nm, selected to optimize product performance and cost.
The benefits of the IDM model for our customersAs an integrated device manufacturer (IDM), ST develops fundamental semiconductor process technologies, creates core intellectual property (IP), designs products using these technologies and IP, and manufactures, tests and packages them using owned facilities or through partnerships. This brings several benefits for our customers:
- Processes designed and refined to meet the applications needs of our customers in various markets.
- IP blocks optimized for specific functions and systems, owned by ST.
- Manufacturing processes are optimized for key performance and yield through the tight teamwork between process, product, and operational teams.
- Control of manufacturing capacity and creation of flexible, reliable supply chains.
This is particularly important for our automotive customers.
An example of these benefits is the combination of FD-SOI and PCM technologies that ST has developed for its Stellar microcontrollers. ST was one of the key innovators in both technologies, working with partners to bring them to market. ST’s ability to master the technology and tailor it to automotive applications has resulted in products with unique benefits. ST’s implementation of PCM technology has allowed the creation of the smallest physical memory cell in the industry delivering 2x the memory density of alternatives.
Thanks to the high-energy efficiency, high reliability, and radiation immunity of this memory technology, ICs designed in FD-SOI with embedded PCM meet the most stringent requirements of automotive applications. ST’s PCM technology achieves automotive requirements for AEC-Q100 Grade 0 with an operating temperature up to +165°C. The patented technology supports high-temperature data retention, including during solder reflow, so firmware can be uploaded before soldering.
Ecosystem plays a key role for transformationAn extensive partner ecosystem from developer tools to specific libraries for safety, security, and data exchange and distribution, augmenting ST’s portfolio capabilities further complements this leading technology. This will also provide the necessary simplification, aiding our customers in their transformation journey towards software-defined vehicles.
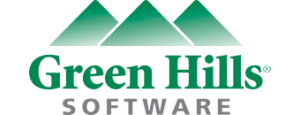
“STMicroelectronics and Green Hills Software are working closely together to deliver innovative integrated hardware and software solutions that address the growing challenges automotive OEMs and Tier 1s face in next generation vehicle zonal architectures.” said Dan O’Dowd, Founder and CEO at Green Hills Software. “Green Hills production-proven safety-certified RTOS and tools, coupled with ST’s Stellar SR6’s unique communication IP, deliver advanced fault tolerant zonal networking that enables significant per-vehicle cost savings while reducing time-to-market.”
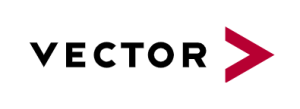
“With MICROSAR Classic, we enable our customers with safe and secure basic software for ECUs for a wide range of use cases. Thanks to many years of close cooperation with ST, the corresponding support for the new Stellar MCUs is already available,” says Jochen Rein, Director of the Product Line Embedded Software and Systems at Vector. “By integrating Stellar’s advanced hardware with Vector’s robust software, customers get the highest level of safety and reliability for both ADAS applications and to successfully manage the transition to Software-Defined Vehicles.”
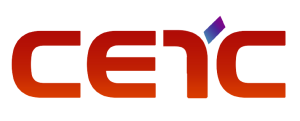
“iSOFT is a leading developer of automotive operating systems in China and the premium partner of AUTOSAR for China’s infrastructure software. Since the introduction of its collaboration with ST in 2016, iSOFT has become ST MCAL agent in China. This includes multiple microcontrollers such as SPC58/SPC56/STM8A, and the companies will also engage in a deeper strategic cooperation on the newly introduced Stellar family that will support EasyXMen Open Source Operating System in the future.” Luo Tong, Vice President, iSOFT

“Neusoft Reach’s software platform, NeuSAR, leads the mass production of China’s full-stack “AUTOSAR +Middleware,” widely used in next-gen ADAS, chassis, power, and body control systems. Neusoft Reach provides complete solutions based on ST’s SPC5 and Stellar E series automotive MCU, including application/basic software, bootloader, refresh, and simulation, which will be complemented with the new gen of Stellar P and G series. Both companies will work together to create a higher level of automotive-grade software and hardware integrated solutions to help OEMs and tier 1s to bring efficient, personalized, and differentiated functions and accelerate SDV innovation.” Jipeng Wang, Director, NeuSAR CP Products BU, Neusoft Reach
ConclusionBy building on common foundations across product dimensions and focusing on robust automotive quality, ST serves a wide market with a comprehensive product range that is both “broad”—spanning from as low as 128 KB to 64 MB memory, single to multicore computation with virtualization—and “deep,” with each series tailored for specific functions: Stellar P and G series focus on integration, and STM32A will be optimized for value, targeting single-core applications that prioritize efficiency and simplicity.
ST’s expanded automotive microcontrollers roadmap focuses on helping its customers to reduce complexity, improve efficiency, while ensuring the highest security and safety standards for next-gen cars. It addresses electrification, personalization, automation, and connectivity.
The post ST’s Automotive MCU technology for next-generation vehicles appeared first on ELE Times.
Trump’s Tariff Surge Rattles Global Electronics Industry: Can India Rise Amid Disruption?
As the Trump administration proposes the introduction of “reciprocal tariffs”—taxing imports at the same rate foreign governments impose on U.S. goods—the global electronics and semiconductor industry is bracing for ripple effects that could redefine supply chains, trade routes, and strategic investments. With India emerging as a serious contender in global electronics manufacturing, these policy shifts could present both opportunities and challenges for the country’s growing semiconductor ambitions.
Global Supply Chains in FluxThe electronics and semiconductor sectors are among the most intricately connected global industries. From chip design in the U.S. and Taiwan, to wafer fabrication in South Korea and China, to final assembly in India and Vietnam—every component in a finished product typically crosses multiple borders. A tariff war threatens to disrupt these finely tuned global supply chains.
This risk was underscored recently when President Donald Trump announced a staggering 104% tariff on Chinese electric vehicles, shaking global markets. Reacting to the tariff hike, Tata-owned Jaguar Land Rover halted its shipments to the U.S. for a month in response to a separate 25% import tariff, citing sudden cost pressures and logistical uncertainty. These developments signal a volatile phase for companies relying heavily on cross-border operations.
For India, which imports up to 88% of its semiconductor requirements, disruptions in sourcing from East Asian hubs could cause short-term volatility in the availability and pricing of key components. Additionally, higher tariffs could push up input costs for Indian manufacturers exporting to the U.S., making pricing less competitive.
A Tailwind for ‘Make in India’?However, there’s a silver lining. As geopolitical tensions rise and multinationals seek “China Plus One” strategies, India is increasingly viewed as a viable alternative. The Indian government’s push under the Production Linked Incentive (PLI) scheme, coupled with new semiconductor fabrication plans and robust demand for electronics, places the country in a favorable position to absorb diverted investments.
This shift is already underway. Apple and Samsung are reportedly accelerating plans to shift manufacturing to India, partly to hedge against Trump’s rising tariffs on Chinese goods. Apple, for instance, has already begun iPhone production at Foxconn’s Tamil Nadu facility, with plans to ramp up output in 2025. These strategic realignments bolster India’s role in the global value chain.
If reciprocal tariffs deter trade between the U.S. and China, Indian manufacturers may gain a competitive edge—particularly in segments like PCB assembly, mobile manufacturing, and back-end chip packaging. This could catalyze India’s ambition to become a $300 billion electronics manufacturing hub by 2026.
Impact on CompetitivenessOver 80% of the U.S. semiconductor industry’s production is destined for international markets, making it highly dependent on global exports. Imposing higher tariffs may weaken its global competitiveness, particularly if retaliatory measures by other countries kick in. On the flip side, Chinese manufacturers could double down on building self-reliant supply chains, while Indian firms may find new export opportunities if trade patterns realign.
Yet, uncertainties remain. India’s electronics industry still depends significantly on imports of chips and sub-components. Tariff-induced disruptions could lead to cost escalations, affecting price-sensitive consumer markets both in India and abroad.
Export Pressures & Strategic RealignmentWith India expanding its export capabilities in smartphones, consumer electronics, and electric vehicle components, increased trade barriers may force a rethinking of pricing strategies. Electronics brands exporting to the U.S. could face squeezed margins or may need to reroute operations to avoid tariffs.
To stay competitive, global electronics firms may explore shifting part of their production from China to tariff-neutral zones such as India, Mexico, or Southeast Asia. This trend, already underway post-COVID-19, may accelerate under tariff-driven pressure.
Policy Implications for IndiaIndia must walk a fine line. While these global shifts could open up new export windows, there’s also a risk of becoming collateral damage in a broader trade conflict. To safeguard domestic manufacturers and leverage emerging opportunities, the Indian government should consider:
- Negotiating strategic trade agreements with the U.S., EU, and ASEAN nations.
- Providing greater ease-of-doing-business incentives for relocating manufacturers.
- Accelerating semiconductor ecosystem development to reduce import dependencies.
- Offer temporary tariff shelters or rebates for affected MSMEs in electronics exports.
The Trump administration’s proposed tariffs may well be a turning point for the global semiconductor and electronics industry. For India, this could serve as both a test and an opportunity—to deepen its electronics manufacturing base, attract foreign investments, and reposition itself as a trusted global partner in a rapidly changing trade environment. Strategic foresight, nimble policy responses, and continued innovation will be key to navigating the challenges ahead.
The post Trump’s Tariff Surge Rattles Global Electronics Industry: Can India Rise Amid Disruption? appeared first on ELE Times.
Transforming Edge Software Development with Arm-based Virtual Prototyping
Courtesy: Synopsys
We’re excited to announce Virtualizer Native Execution for Arm-based machines. This groundbreaking virtual prototyping technology will transform how software is developed for edge devices and applications — particularly in the automotive, HPC, IoT, and mobile industries.
Virtualizer Native Execution enables a paradigm shift in edge-focused software development via improved:
- Simulation performance. Virtualizer Native Execution significantly boosts the performance of virtual prototypes — speeding up software development, debugging, and testing.
- Development productivity. Virtualizer Native Execution leverages cloud-native approaches to enhance productivity, reduce toolchain silos, and make modern development workflows more accessible for embedded software engineers.
The market-leading virtual prototyping solution with the largest library of models and IP,Virtualizer enables developers to work with virtual prototypes of target hardware instead of physical setups that are location-dependent and difficult to scale.
Virtualizer Native Execution extends the complete Virtualizer tool suite to the Arm ecosystem, allowing virtual prototypes to be built, executed, and tested directly on Arm-based machines. And because it can be leveraged across development and computing environments — on-premises, in the cloud, and at the edge — it eliminates toolchain and workflow silos and helps increase development flexibility and agility.
Virtualizer Native Execution significantly boosts development speed and efficiency via:
- Native execution. Instead of simulating the target hardware’s CPU on an Instruction Set Simulator (ISS), Virtualizer Native Execution enables virtual prototypes to be executed directly on the host CPU. This significantly reduces boot times (from 20 minutes to tens of seconds for a typical Android boot).
- Scalability. Modern Arm host machines offer more than 96 cores, and Virtualizer Native Execution can directly map each core of the virtual system-on-chip (SoC) to a physical core to greatly accelerate prototype performance.
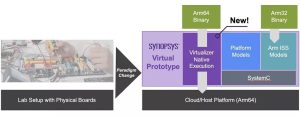
Arm-based CPUs have long dominated the mobile market, and in recent years they’ve been increasingly used for automotive, IoT, consumer, and other edge-based applications. Those in the cloud and HPC markets have also embraced Arm CPUs and IP, which provide an alternative to traditional x86-based solutions and deliver exceptional performance, power, and cost benefits.
This widespread adoption is leading to greater alignment and uniformity of the CPUs and toolsets being used across on-premises, cloud, and edge environments. Often referred to as Instruction Set Architecture (ISA) parity, this uniformity provides new opportunities to streamline development efficiency and flexibility.
Virtualizer Native Execution supports the increased adoption and development of Arm-based solutions and takes advantage of ISA parity to supercharge software development and edge innovation.
Combining virtual prototyping with hardware-assisted verification (HAV)Virtualizer Native Execution also supports hybrid emulation, which combines the unique strengths of virtual prototyping and hardware-assisted verification (HAV). Tightly integrated with Synopsys HAV solutions, Virtualizer Native Execution supports hybrid setups where the CPU subsystem is virtualized and the rest of the device under test (DUT) is emulated. And because it eliminates ISS overhead and runs natively on the host CPU, Virtualizer Native Execution is able to keep up with the fastest emulation systems (including the new ZeBu-200).The speed and scalability of Virtualizer Native Execution also enable new emulation use cases, like application-driven performance and power validation.
Taking embedded software development to the cloudDeveloping embedded software for edge devices has long been a fragmented process involving complicated lab setups, delicate test boards and cables, and disparate toolsets. Not only has this hindered efficiency and scalability, but it has prevented the adoption of modern, agile development processes.
With Virtualizer Native Execution, developers can:
- Build and scale CI/CD pipelines in the cloud.
- Take advantage of higher performance and throughput as well as faster boot times.
- Replicate and align virtual prototypes across development and operating environments — on-premises, in the cloud, and at the edge.
Virtualizer Native Execution for Arm marks a significant leap forward in edge-focused software development. With better performance and scalability, native execution on Arm-based machines, and cloud-to-edge parity, developers can supercharge their virtual prototyping workflows.
The post Transforming Edge Software Development with Arm-based Virtual Prototyping appeared first on ELE Times.
High-Speed Data Centers Owe a Debt of Gratitude to DRAM Memory Interfaces
Courtesy: Renesas
High-performance AI data centers are reshaping semiconductor design and investment trajectories like no technology we’ve seen. As recently as 2022, spending on AI infrastructure was in the vicinity of $15 billion. This year, expenditures could easily top $60 billion. Yes, that sucking sound you hear is the oxygen being pulled from every investment plan and breathed into data centers.
We are clearly operating in an era of unprecedented artificial intelligence capital outlays – notwithstanding the potential impact of newcomers like DeepSeek. But while high-performance computing processors from Nvidia, AMD, and others are busy stealing the limelight, the high-bandwidth memory that stores training and inference models is having its day too – with 2024 DRAM revenue setting a record of nearly $116 billion.
Data center servers are driving a continuous increase in CPU core count, which requires more memory capacity to make higher-bandwidth data available to each processor core. But the laws of physics are quickly catching up. A CPU signal can only go so fast and far. That’s where memory interface devices such as register-clock drivers and data buffers come into play. By allowing the clock, command, address, and data signals to be re-driven with much-improved signal integrity, these interfaces enable the entire memory subsystem to scale in speed and capacity.
Today, RCD empowers registered DIMMs (RDIMMs) to operate up to 8 Giga Transfers per Second (GT/s). Most data center servers use RDIMMs, although some HPC systems need even greater memory subsystem performance.
Memory Interfaces Further Accelerate DRAM and Processor PerformanceNotable for the vital role it plays in data center server systems, DRAM architecture hasn’t actually changed dramatically over the past three decades. Increases in density, speed, and power efficiency can be attributed largely to deep-submicron semiconductor scaling, while new 2.5D and 3D stacked DRAM packaging allows for higher-capacity DIMM modules.
As explained above, advances in memory interface technology – beginning with synchronous DRAM and carrying across multiple generations of double data rate DRAM – have played an outsized role in helping the interface keep pace with processor speeds.
Multi-rank DIMMs (MRDIMMs) are an innovative technology designed for AI and HPC data center applications. Made possible through a partnership between Renesas, Intel, and memory suppliers, MRDIMMs allow the memory subsystem to scale to much higher bandwidths compared to RDIMMs on corresponding server systems. Specifically, MRDIMMs double the data transfer speeds of the host interface by enabling two ranks of memory to fetch data simultaneously, which yields a six percent to 33 percent improvement in memory bandwidth.
Renesas DRAM Interfaces Help Close the Processor-to-Memory Performance GapLate last year, Renesas released the first complete memory interface chipset solution for second-generation DDR5 MRDIMMs. With an operating speed of 12.8GT/s, this represented a huge improvement in terms of how fast we can drive the interface compared to the 8.0GT/s maximum for a standard DIMM.
How did we get there? Through a combination of highly orchestrated component technologies. Since its inception at Integrated Device Technology, before it was acquired by Renesas, we’ve been on a mission to solve one problem confounding memory performance: signal integrity.
As the speed gap between DRAM and the CPU began to grow, the physical loading of the DRAM was becoming a problem for system architects. We saw an opportunity to address the challenge through our analog and mixed-signal design competency. The first in line was an RCD we used to intercept and redrive the clock signal and command address between the DRAM and processor. Subsequently, we developed a line of fully buffered DIMMs, which encapsulated all types of signals on the system memory interface, including clocks, command addresses, and data.
Fast forward, and our newest DDR5 memory interfaces include second-generation RCDs and data buffers for MRDIMMs in addition to a power management IC (PMIC), making us the only company to offer a complete chipset solution for the next-generation of RDIMMs and MRDIMMs. In addition, Renesas has made a significant contribution in helping power efficiency by evangelizing a concept called “voltage regulation on DIMM.” Voltage regulation circuitry now sits directly on the DIMM, as opposed to the motherboard, which allows for a more efficient, distributed power model. This is done using PMICs that locally generate and regulate all the necessary voltages needed by various DIMM components.
Leveraging the Electronics Design Ecosystem for the FutureRenesas has amassed a vast base of in-house expertise by collaborating with a large design ecosystem of leading CPU and memory providers, hyperscale data center customers, and standards bodies like JEDEC. That gives us the freedom to remove the bottlenecks that stand in the way of our ability to continue increasing DIMM speeds and capacity by determining how many DRAM components can be populated and how fast they can run.
It also opens opportunities to leverage technologies developed for AI data centers and redirect them to emerging use cases. That’s true for the higher processing and memory bandwidth requirements influencing designs at the edge of industrial network controls, where data must be captured and turned into actionable insights. And, it applies to the surging data volumes required by automotive safety and autonomous driving applications, which are quickly turning our vehicles into servers on wheels.
The post High-Speed Data Centers Owe a Debt of Gratitude to DRAM Memory Interfaces appeared first on ELE Times.
VIGO and PCO partner on type-II superlattice cooled IR detector arrays
Mission Moon — how CubeRover makes autonomous docking for space possible
Courtesy : Bosch
The moon — an environment full of extremes that can push even the most advanced technologies to their limits. Abrasive dust blocks sensitive sensors, temperatures as low as -150°C challenge conventional electronics, and the complete absence of GPS makes precise navigation nearly impossible. Such conditions demand innovative solutions tailored to the unique requirements of this extraordinary environment.
Bosch brings its technological expertise to a visionary project funded by NASA’s Tipping Point program with $5.8 million. In collaboration with Astrobotic, WiBotic, the University of Washington, and NASA’s Glenn Research Center, the project unites contributions from leading innovators. CubeRover(TM), developed by Astrobotic, is the mission’s lightweight and modular exploration vehicle. WiBotic contributes wireless charging technology, enabling efficient energy transfer under lunar conditions. Bosch focuses on autonomous docking, providing critical systems that ensure the CubeRover(TM) can navigate and connect reliably in this extreme environment. The University of Washington and NASA Glenn Research Center contribute by offering performance characterization and testing of the wireless charging system.
Together, these efforts promise to revolutionize space exploration while paving the way for future innovations in autonomous systems development.
The minds behind the mission — Vivek Jain and his teamOne of them is Vivek Jain, a lead expert at Bosch Research. Astrobotic serves as the principal investigator for this project, working closely with Bosch, which contributes its expertise in sensing, software, and autonomous docking for wireless power transmission.
Together, the partners are developing technologies that enable the rovers to navigate the moon with precision — without GPS. To achieve this, Bosch relies on a combination of camera data, Wi-Fi fingerprinting and sensor fusion. These approaches ensure that the rovers operate reliably even under extreme conditions such as intense light or presence of sticky lunar dust. With these innovative solutions, Bosch plays a crucial role in advancing the development of autonomous systems designed for the moon’s demanding environment.
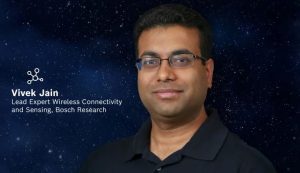
CubeRover(TM) is the centerpiece of the lunar mission, designed specifically for operation on the moon’s surface. A modular, ultra-lightweight, and compact rover, its smallest form factor weighs less than 5 pounds and is roughly the size of a shoebox. These characteristics enable the simultaneous transport of multiple rovers on a central platform (lander), which lands on the lunar surface and serves as a base station for power and navigation.
This makes missions not only more flexible but also more cost-effective, as multiple rovers can be deployed with a single launch. In addition to its compact size, CubeRover(TM) impresses with its versatility. It can carry scientific instruments such as cameras or spectrometers, opening up new approaches to lunar exploration. With its innovative technology and ability to operate reliably even in extreme environments, it represents a turning point in the exploration of new worlds.
Reaching the destination without GPS — the challenges of navigating the moonHow Bosch develops creative solutions for navigation.
Orientation with visual markers and sensor fusionHow do you navigate on the moon, where GPS is not an option? Bosch has the answer with innovative technologies that guide the CubeRover(TM) safely through the extreme conditions of the lunar surface. The lander, a platform on the moon’s surface, serves as a central base station for the CubeRover(TM), providing energy and orientation. Special visual markers, known as AprilTags, are attached to the lander and function like QR codes. These markers are detected by the CubeRover(TM)’s camera, enabling it to accurately calculate its position and navigate securely.
In addition, the CubeRover(TM) employs sensor fusion, combining camera data with information from motion sensors and wheel speed sensors. This technology ensures stability even on uneven or slippery surfaces — performing reliably amidst dust, intense light, or wheel slips.
Wi-Fi fingerprinting as a backup solutionIn addition to visual markers, Bosch uses Wi-Fi fingerprinting to ensure the CubeRover(TM)’s navigation. The lander, the central platform on the lunar surface, emits Wi-Fi signals that the rover receives. Based on the signal strength and characteristics, the CubeRover(TM) determines its position and creates a map of the surroundings.
This method acts as a backup when visual markers are obscured by dust or shadows, ensuring the CubeRover(TM) remains navigable even under challenging conditions. By combining visual markers, sensor fusion, and Wi-Fi fingerprinting, Bosch enables precise navigation – entirely without GPS.
Wireless chargingThe small rover presents unique challenges for energy supply. Being too small for large solar panels, the CubeRover(TM) employs an innovative solution: wireless charging. The lander collects solar energy and transfers it wirelessly to the rover.
An additional benefit of this technology is the heat generated during the charging process. This heat is used to protect the rover from the extreme temperatures of the lunar night. Intelligent charging algorithms ensure that the rover aligns its position optimally for efficient energy transfer.
The post Mission Moon — how CubeRover makes autonomous docking for space possible appeared first on ELE Times.
Delta Electronics Fuels India’s Digital Ambitions with Scalable, Sustainable ICT Solutions
In an exclusive conversation with Rashi Bajpai of ELE Times, Pankaj Singh, Head of Data Center & Telecom Business Solutions at Delta Electronics India, delves into the company’s groundbreaking strides in energy-efficient ICT infrastructure.
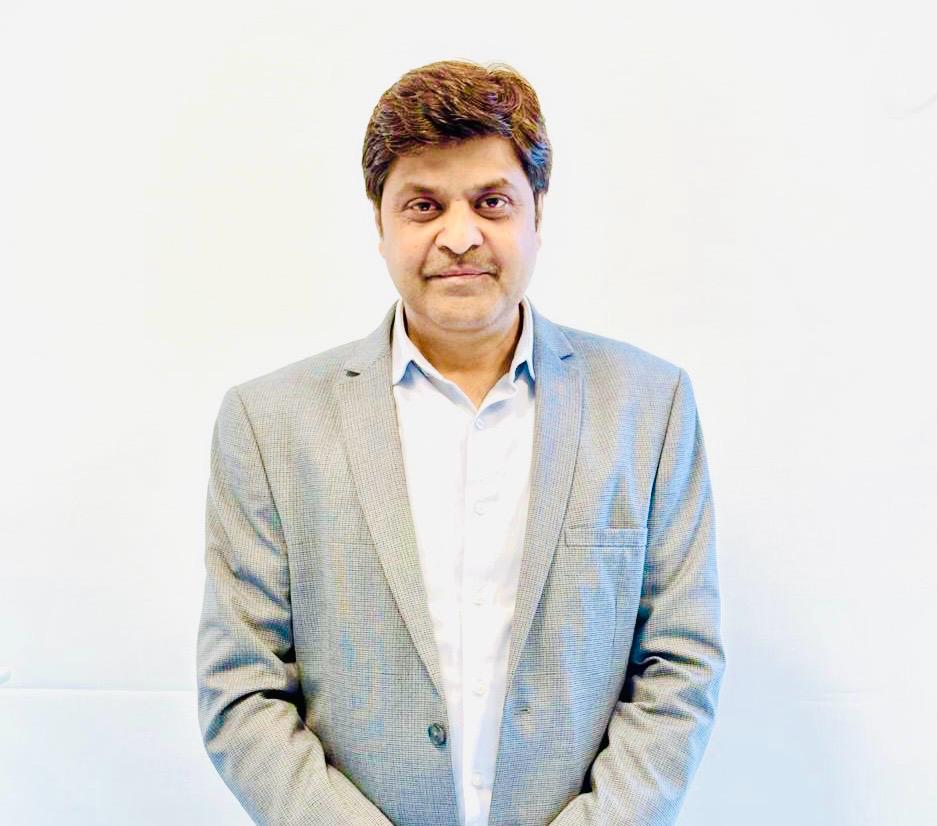
Highlighting innovations tailored for India’s unique needs and global scalability, he discusses Delta’s pivotal role in shaping sustainable, high-performance telecom and data center ecosystems aligned with the Digital India vision.
Here is the excerpt:
ELE Times: Delta Electronics has long been a leader in energy-efficient ICT solutions. Could you elaborate on the latest innovations in your telecom and data center products that optimize energy consumption without compromising on performance?
Mr. Pankaj Singh: Delta continues to innovate in the ICT sector by developing high-efficiency power and cooling solutions that optimize energy consumption while maintaining superior performance. Our telecom and data center solutions incorporate 97% efficiency rectifiers, modular UPS systems exceeding 97% efficiency, and AI-driven thermal management that dynamically adjusts cooling based on real-time data, significantly improving Power Usage Effectiveness (PUE). Additionally, our hybrid power systems seamlessly integrate renewable energy sources, reducing reliance on conventional power grids. These innovations help businesses enhance operational efficiency while reducing carbon footprints and energy costs, reinforcing Delta’s commitment to sustainability and technological advancement.
ELE Times: As a company committed to both local and global markets, how does Delta ensure that its telecom and data center products are specifically tailored to meet India’s unique requirements while also being scalable for international use?
Mr. Pankaj Singh: Delta adopts a localization-with-scalability approach to develop telecom and data center solutions that address India’s unique challenges while remaining adaptable for global markets. Last year, we inaugurated our global R&D Center in India with the vision of “Design in India, for the World.” Our India-based R&D team develops products tailored to the country’s diverse climatic conditions, including extreme temperatures and humidity, while ensuring power reliability through high-efficiency rectifiers and advanced battery storage solutions. Our grid-resilient hybrid power systems enable seamless connectivity even in remote areas with unstable power supply. Additionally, Delta ensures compliance with Indian (BIS, TEC) and global (UL, CE, IEC) standards, making our products viable for both domestic and international markets. By integrating modular and scalable architectures, we deliver future-ready ICT solutions that evolve with business needs while maintaining high efficiency and reliability.
ELE Times: With the ambitious goal of powering 5 lakh telecom towers across India, how are Delta’s cutting-edge solutions addressing the increasing demand for reliable connectivity, and how does energy efficiency factor into this large-scale initiative?
Mr. Pankaj Singh: Delta is committed to supporting India’s telecom expansion by delivering energy-efficient and reliable power solutions for 5 lakh telecom towers across the country. Our advanced high-efficiency rectifiers, lithium-ion battery energy storage solutions, and hybrid power systems ensure uninterrupted connectivity, even in regions with unstable grid power. By integrating renewable energy sources such as solar and wind with intelligent power management systems, we help telecom operators reduce operational costs and carbon footprints. Additionally, our comprehensive telecom customer service ensures 24/7 technical support, proactive maintenance, and remote monitoring capabilities, enabling seamless network operations. With a strong focus on energy efficiency, grid resilience, and smart automation, Delta empowers telecom providers to enhance network uptime while meeting sustainability goals.
ELE Times: At ELECRAMA 2025, Delta introduced several new products designed to support India’s Digital India vision. Could you highlight the key technical features of these products and explain how they will contribute to the enhancement of India’s digital infrastructure?
Mr. Pankaj Singh: At ELECRAMA 2025, Delta unveiled a range of next-generation power and ICT solutions aimed at strengthening India’s digital infrastructure. Our new high-density UPS systems offer industry-leading >97% efficiency, ensuring maximum power protection for critical IT applications. We also introduced prefabricated modular data centers, which provide a plug-and-play, scalable approach to IT infrastructure expansion, allowing rapid deployment with optimized energy consumption. Our 5G-ready telecom power systems integrate solar energy, lithium-ion storage, and AI-based thermal management, reducing energy costs while enhancing network reliability. These solutions are set to support India’s Digital India vision by providing efficient, scalable, and sustainable infrastructure for the country’s growing data needs.
ELE Times: Sustainability is a key focus for Delta. How do your product development strategies balance the need for technological innovation with the imperative for environmental sustainability, particularly in the context of energy-efficient data centers and telecom networks?
Mr. Pankaj Singh: Sustainability is at the core of Delta’s product development strategy, ensuring that every innovation balances technological advancement with environmental responsibility. Our data center and telecom solutions are designed to minimize energy consumption by incorporating high-efficiency power conversion, intelligent thermal management, and renewable energy integration. We use recyclable materials, lead-free components, and eco-friendly manufacturing processes to reduce environmental impact. Additionally, our solar-powered energy solutions and AI-driven cooling systems significantly cut carbon emissions and operational costs. By prioritizing energy efficiency, sustainable materials, and intelligent automation, Delta is driving the ICT industry toward a greener, more sustainable future without compromising on performance or scalability.
ELE Times: The telecom and data center industries are evolving at an unprecedented pace. What are the most significant challenges Delta faces in designing solutions for this rapidly changing environment, and how do your latest technologies address these challenges to ensure long-term scalability and efficiency?
Mr. Pankaj Singh: The telecom and data center industries are evolving rapidly, driven by increasing data demand, emerging technologies like 5G and AI, and the need for energy-efficient infrastructure. Delta faces several key challenges in designing solutions that ensure long-term scalability and efficiency.
One major challenge is scalability, as networks and data centers must accommodate exponential growth in bandwidth, processing power, and storage. Delta addresses this by implementing modular and cloud-native architectures, allowing seamless expansion while maintaining cost efficiency. Another challenge is energy consumption, as data centers are among the largest consumers of electricity. Delta integrates high-efficiency power solutions, intelligent cooling systems, and renewable energy integration to minimize energy use and reduce environmental impact.
Delta’s latest technologies also focus on 5G, edge computing, and AI-driven network management, enabling faster connectivity, real-time data processing, and reduced latency. By integrating automation, energy efficiency, and scalable architectures, Delta ensures its telecom and data center solutions remain future-ready, adaptable, and optimized for performance in a rapidly evolving digital landscape.
The post Delta Electronics Fuels India’s Digital Ambitions with Scalable, Sustainable ICT Solutions appeared first on ELE Times.
The Revised Industrial Robot Safety Standard
Courtesy: ANALOG DEVICES
ISO 10218, third edition, was released at the start of 2025. This standard covers industrial robot safety. Typically, this means fixed industrial robots, including what are known as cobots. A HAS consultant assessed the standard, which will hopefully be published shortly in the OJEU (official journal of the European Union) giving a presumption of conformity with all relevant machinery directive clauses.
Note – ISO TC 299 WG 3: avoid using the word cobot, as there is no such thing. The assertion is that the application is collaborative and not the robot. Any robot can work in a collaborative application with the right external equipment, e.g., a laser scanner or 3D TOF may allow implementation
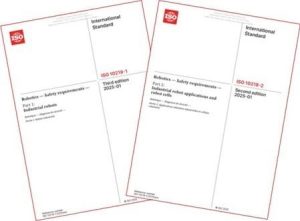
I think I started on this committee in 2018, and Ireland hosted a meeting on the committee in 2019, but I believe WG3 was already working on this revision well before that time. The convenor was Roberta Nelson Shea of Universal Robots, which meant we had much experience right there, but there was a lot. I mean a lot, of experience in both the application and design of robots within the group. It also included health and safety professionals, independent assessors, and a human factors expert. It was a well-attended group, with over 50 in some cases, leading to restrictions on how many from each country were allowed to attend. Countries with big teams attending included Canada, Japan, Korea, Sweden, Germany, the USA, the UK, Ireland, Denmark, and Italy…. I must admit, I’m a robot safety expert who has never used a robot. My other major functional safety contributor is on the IEC 61508 committee, where I lead the semiconductor group, including the new IEC 61508-2-1. Therefore, once we strayed into the use of robots, as opposed to their design, I was out of my depth. For this reason, I am sure that the highlights I have chosen below from the new version would be very different from those chosen by someone with a different background.
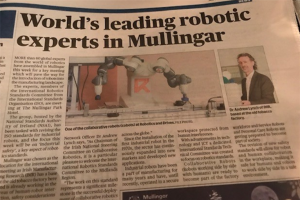
My highlights are:
- Removal of mandatory redundancy requirements
- New security guidance
- New comms requirements
Removal of Mandatory Redundancy Requirements
Let’s start with the mandatory redundancy requirements. The older 2011 version required a default SIL 2 with HFT=1 or PL d CAT 3 safety function. This offended me on several levels, including:
- With complex technology, systematic failure modes are more of a concern than random hardware failures
- HFT= 1 and CAT 3 are not even the same thing (CAT 3 allows the impact of diagnostics in achieving single fault tolerance to be considered, HFT does not)
- Modern technology based on semiconductors can be far more reliable than older mechanical technology and with higher diagnostic rates and lower diagnostic test intervals
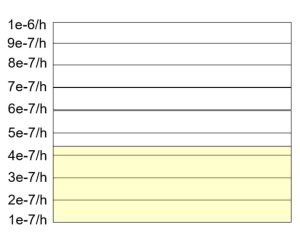
Even after many years of debate (yes years and I am not exaggerating) the following was agreed. If you weren’t involved, the number of 4.43e-7/h might seem random. Both PL d and SIL 2 require a failure rate in the range 1e-6/h to 1e-7/h, so it’s just below the midpoint of the range. It’s in the better half, indicating lower-than-average risk. But if lower-than-average was all we required, we could have used 5.0e-7/h. Shown another way, it can be compared to what is traditionally achieved with a CAT 3 architecture. The graphic above also shows it exceeds what is generally considered possible with a CAT 2 (non-redundant) architecture. However, the best way to show it is by highlighting it using ISO 13849-1:2015 Annex K. To get to this number with a CAT 2 architecture (single channel with diagnostics) you need an MTTFd (mean time to failure dangerous) of 62 years and a DC of 90%. It also shows that previously with your CAT 3 architecture a DC of 60% would have been acceptable but that would deliver a much worse PFHd unless you got your MTTFd to at least 43 years and that with CAT 3 and a DC of 90% you can easily reach down into PL e type performance.
It’s good to write this down while I still remember the reasoning. These changes will make it easier to adopt new technologies into robots but reduce the robot cost and increase the robot’s capabilities, which hopefully will all contribute to a higher adoption of robots. Such new technologies might include 3D TOF and novel encoders.
New Security Guidance
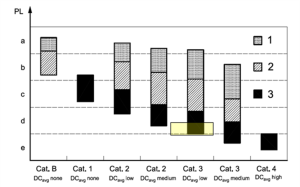
My next highlight is the new cyber security guidance. It’s always controversial whether safety standards should include anything on cyber security or whether the two disciplines should remain separate. However, it is good that we added something as the new EU machinery regulation (replacing the old machinery directive) places more emphasis on cyber security than the old machinery regulation. We also now have the CRA . I would have liked to add more emphasis on IEC 62443 compliance, but what we got is good. A cyber security risk assessment is now required, and IEC TS 63074:2023 is called out, which then defers to IEC 62443. I spoke on cyber security for robots at last year’s international robot safety conference in Cincinnati. Unfortunately, the presentations from this excellent conference are not available on the web.
New Comms Requirements
Lastly, in a world with more and more requirements for always being connected, data is the new oil; it is good that the standard now includes requirements for industrial communications. There was nothing in the old version on safety data to be transmitted over a network. Previously, the best guidance would have been in IEC 61508-2010 7.4.11, which mentions a white channel design with no further details and defers to either IEC 61784-3 or IEC 62280/EN 50519 for the black channel designs. The new version of ISO 10218 concentrates on the more common black channel approach and, despite being short, shows how the black channel requirements can be tailored differently for the internal robot network (controller to the various axes) and the external robot network, e.g., controller to a PLC.
This is an area I continue to work on; we are revamping IEC 61508-2 7.4.11 with more details on the white channel in particular, which I think might be especially relevant for robot internal networks since it is more suitable in my view for hard real-time requirements. I have also, for my sins, been appointed as the liaison between IEC TC 65 SC65A(system) and SC 65C. The black channel will continue to be the most important for the controller to the PLC network, and the 1km range offered by 10BASE-TIL and even Ethernet APL / 2-WISEcould be important here.
Other information I like in the new version includes:
- The long list of safety functions in Annex C
- The allowances for small robots in 5.1.17 (<10kg, <250mm/s, <50N)
- The nice figure in Annex B shows maximum, restricted, operating, and safe-guarded spaces
ISO TC 299 WG 3 is continuing to work on ISO 20218-3, which will give more guidance on the limited information on cyber security within ISO 10218. I don’t know whether ISO 10218 already needs a refresh to allow for machinery regulation.
The post The Revised Industrial Robot Safety Standard appeared first on ELE Times.
Pages
