Українською
  In English
Feed aggregator
EDA powerhouses align offerings with Intel’s 18A node

The EDA trio—Cadence, Siemens EDA, and Synopsys—was prominent at the Intel Foundry Direct Connect 2025 while lining up AI-driven analog and digital design flows for Intel’s 18A process node. The offerings also included IPs ranging from SerDes to DDR5 to Universal Chiplet Interconnect Express (UCIe).
Next, these EDA outfits inked advanced packaging partnerships by offering workflows for Intel Foundry’s Embedded Multi-die Interconnect Bridge-T (EMIB-T) technology, which combines the benefits of EMIB 2.5D and Foveros 3D packaging technologies for high interconnect densities at die sizes beyond the reticle limit.
Let’s start with EDA flows.
Cadence has certified its RTL-to-GDS flow for 18A process design kit (PDK), which includes the Cerebrus Intelligent Chip Explorer, Genus Synthesis solution, Innovus Implementation System, Quantus Extraction solution, Quantus Field Solver, Tempus Timing solution, and Pegasus Verification System.
Siemens EDA has certified its Calibre nmPlatform sign-off tool and Solido SPICE and Analog FastSPICE (AFS) software tools for 18A production PDK. Likewise, the qualification of Calibre nmPlatform and Solido Simulation Suite offerings for the Intel 18A-P process node is now underway. These EDA tools are also part of the Intel 14A-E process definition and early runsets already available.
Figure 1 Synopsys unveiled an EDA and IP collaboration roadmap with Intel Foundry at the event.
IP and advanced packaging liaison
Cadence has announced a broad range of IPs for the 18A process node. That includes 112G extended long-reach SerDes, 64G MP PHY for PCIe 6.0, CXL 3.0, and 56G Ethernet, LPDDR5X/5 – 8533 Mbps with multi-standard support, and UCIe 1.0 16G for advanced packaging.
Besides IP offerings, Cadence is partnering with Intel Foundry to develop an advanced packaging workflow to leverage EMIB-T technology. This workflow will streamline the integration of complex multi-chiplet architectures while complying with standards.
Figure 2 Cadence is certifying EDA toolsets and IPs for Intel’s 18A process node.
Meanwhile, Siemens EDA has announced the certification of a reference workflow for EMIB-T technology using through silicon via (TSV) technique. It’s driven by the company’s Innovator3D IC solution, which provides a consolidated cockpit for constructing a digital twin. It also features a unified data model for design planning, prototyping, and predictive analysis of complete package assembly.
Synopsys is also employing its 3DIC Compiler to facilitate a reference workflow that enables efficient EMIB-T designs with early bump and TSV planning and optimization. It also features automated UCIe and HBM routing for high quality of results and fast 3D heterogeneous integration. Here, the 3DIC Compiler facilitates feasibility and partitioning, prototyping and floorplanning, and multiphysics signoff in a single environment.
Related Content
- Intel: Gelsinger’s foundry gamble enters crunch
- Intel Financial Risks, Layoffs, Foundry Ambitions
- Intel 18A Advanced Packaging is Key to Tech Leadership
- Partners Applaud Intel Foundry’s Wider Ecosystem Approach
- Intel comes down to earth after CPUs and foundry business review
The post EDA powerhouses align offerings with Intel’s 18A node appeared first on EDN.
Do you use low-side current sensing?

Sensing of current going to a load is a critical and often mandatory requirement in many designs. While there are many contact and non-contact ways to accomplish this sensing, such as using Hall-effect devices, current transformers (for AC only, of course), Rogowski coils, fluxgate sensors, among others, the in-line resistor is among the most popular due to its small size, low cost, and overall convenience. The concept is simple: measure the voltage across an accurate, known resistor, and use Ohm’s law to determine the current; this can be done with analog circuitry or digital computation.
Terminology
A quick terminology note: this inline resistor is almost always called a “shunt” resistor in application notes and data sheets, but that is a misnomer. The reason is that to “shunt” means to divert some of the current around the point being measured, and that was done is some current-measurement arrangements, especially for power in the pre-electronics era. However, the sensor resistor here is in series, so all the current flows through it.
This misleading terminology has become such an embedded part of our established verbiage that I won’t try to fight that battle. It’s similar to the constant misuse of the word “ground” for circuits which have absolutely no physical of figurative connection to Earth ground, and where “common” would be a more accurate and less confusing term.
Current sense topology
Using a sense resistor is only the first step in the current-sensing decision. The other part is topology: whether to use high-side sensing with a resistor placed between the source and the load, or low-side sensing where it is placed between the load and ground return, Figure 1.
Figure 1 The relative position of the sense resistor and the load between the power rail and ground are the only topological difference distinguishing high-side sensing (left) from low-side sensing (right), but there are significant circuit and system implementations. Source: Microchip
Tradeoffs
As with so many engineering situations, designers must also consider the tradeoffs when choosing between low-side and high-side current sensing. The relative pros and cons of each topology are a good example of the ongoing challenge of engineering tradeoffs at the intersection of power-related and classic analog circuitry.
With the high-side approach, there’s good news, at least at first glance:
- The load is grounded (a major advantage and often a requirement).
- The load is not energized even if there is a short circuit at the power connection.
- The high current that flows if the load is shorted is easily detected.
On the other hand, the high-side downsides are not trivial:
- The common-mode voltage across the sense resistor can be very high (even dangerous) and requires special consideration; it may even need galvanic isolation.
- The sensed voltage across the resistor needs to be level-shifted down to the system operating voltage to be measured and used.
- In general, increased circuit complexity and cost.
Low-side sensing has its own attributes, again starting with its positive attributes:
- The voltage across the resistor is ground referenced, a major benefit.
- The common-mode voltage is low.
- It’s fairly easy to design into the circuit with a single supply.
But with the good news, there are unavoidable low-side complications:
- The load is no longer grounded, which can have serious system-level implications.
- The load can be activated by accidental short to ground.
- The sensing arrangement can cause ground loops.
- A high load current due to a short circuit will not be detected.
Designers’ choice
In looking at the analog side of schematic diagrams over the past few years (I know, it’s an unusual “hobby”), as well as seeing what others were doing in their design discussions, I assumed that most designers were opting for high-side sensing. They were doing so despite the challenges it brings with respect to common-mode voltage, possible need for galvanic (ohmic) isolation, and other issues, especially because they wanted to keep the load grounded. Many vendors offer appropriate amplifiers, analog and digital isolation options, and subsystems so the “pain” of using high-sigh sensing is greatly reduced, and the benefits it offers were easily retained.
But maybe I am mistaken about designers’ choices. Perhaps the reason that there has been so much discussion of high-side sensing is not necessarily that it is more popular, but because it is more complicated and so needs more explanation of its details. In other words, was I confused about the cause of all this attention with the effect?
My low-side misconception
What made re-think the presumed absence of low-side sensing was the recent release of the TSC1801, a new amplifier from ST Microelectronics specially targeting low-side sensing. It features high accuracy (0.5%), high bandwidth (2.1 MHz), has a fixed gain of 20 V/V, and is suitable for bidirectional sensing, Figure 2. The accuracy and tracking of the two internal input resistors is critical to performance in this application category.
Figure 2 The block diagram of the TSC1801 low-side current-sensing amplifier is conventional, but it’s the performance that counts; the matching and tracking of the 1-kΩ input-resistor pair is critical. Source: ST Microelectronics
It made me wonder: if only few designers are choosing low-side sensing, and it since it is relatively easy to implement, why would a part like this be needed when there are already many suitable amplifiers available?
The device also challenged another one of my apparent misconceptions: that automotive designs won’t use low-side sensing because their loads must be grounded. If that’s the case, why does ST explicitly call out automotive applications in the part’s collateral (I know, application talk is easy to do) but also provide this part with the automotive AEC-Q100 qualification? Unlike marketing “talk,” that’s a relatively costly step in design and production.
So, my probably unanswerable question is this: what’s the split between use of high-side versus low-side sensing in designs? How does that split vary with end-application? Is some market-research firm willing to look into it for me?
If you want to know more about the two current-sensing options, there are many good sources available online (see References). While there is some overlap among them, as you’d expect, some offer additional interesting perspectives as well based on their products and expertise.
Have you ever had to defend your choice of one or the other in a design? What were the arguments for and against the approach you chose?
Related Content
- The self-powered current loop: Still a viable transducer-interface option
- E-fuses: warming up to higher-current applications
- Sub-milliohm resistors bring current-sense benefits but also challenges
- Use optical fiber as an isolated current sensor?
- Current-sense resistor brings two related and challenging tradeoffs
References (and there are many more!)
- All About Circuits, “Resistive Current Sensing: Low-Side vs. High-Side Sensing”
- Analog Devices, “ AN-105: Current Sense Circuit Collection: Making Sense of Current”
- Microchip Technology, “High-side versus Low-side Current Sensing”
- Renesas, “Current Sensing with Low-Voltage Precision Op-Amps”
- Rohm, “Low-Side Current Sensing Circuit Design”
- Texas Instruments, “Precision, low-side current measurement”
- Texas Instruments, “An Engineer’s Guide to Current Sensing”
- Texas Instruments, “Low-Side Current Sense Circuit Integration”
The post Do you use low-side current sensing? appeared first on EDN.
A decission was made
![]() | 250€ later... [link] [comments] |
Beneq Transform ALD cluster tool qualified for GaN power device production by tier-1 Asian manufacturer
BluGlass completes $2.3m placement and launches up to $6m share purchase plan
SMD opens R&D Innovation Hub at CSA Catapult in Newport
Wolfspeed’s CFO to leave firm at end of May
Стажування в компанії Ajax Systems: для чого, для кого і з якими перспективами
Компанія Ajax Systems у межах ініціативи Ajax Next та в партнерстві з КПІ ім. Ігоря Сікорського вже втретє проводить Mechanical Internship – стажування для студентів університету. Заняття за його програмою розпочато 4 березня, а завершаться вони наприкінці семестру. Для участі відібрано 17 студентів різних факультетів університету. Редакція "Київського політехніка" поспілкувалася з представниками компанії, факультету та одним із випускників програми, щоби краще дізнатися про те, для чого проводиться таке практичне навчання, чого мають навчитися стажери, і які перспективи матимуть ті, хто успішно пройде усю програму.
Is it peak laziness? Or utmost genius?
![]() | Got tired of manually turning on my laptop cooling pad(IETS600). So I used a leftover Arduino to tap into the PWM pin of the fan motor. Communicate via USB Serial from a c# program that monitors which app is open, and if its a game, will send the instruction to the Arduino to turn on the PWM pin at whatever speed I want :) [link] [comments] |
Power Tips #140: Designing a data center power architecture with supply and processor rail-monitoring solutions

Machine intelligence enables a new era of productivity and is becoming an integral part of our lives and societies across many disciplines and functions. Machine intelligence relies on computing platforms that execute code, decipher data, and learn from trillions of data points in fractions of a second. The computing hardware for machine intelligence needs to be fast, extremely reliable, and powerful. Designers must combine solid design practices with self-diagnostics and continuous monitoring schemes to prevent or manage potential faults such as data corruption or communication errors in the system.
An essential element in such monitoring systems is the supervision and monitoring of power rails throughout the system. In this article, I’ll examine and describe some of the best practices for designing supply and processor rail-monitoring solutions in enterprise applications.
Understanding power architecturesEnterprise computing relies upon a complex power architecture that delivers energy from AC sources to every point of load in the system. Figure 1 is a high-level illustration of elements in a server rack.
Figure 1 High-level server rack diagram with distributed battery backup units (BBUs) and power supply units (PSUs) connected to a busbar that then distributes AC power thought to the rack. Source: Texas Instruments
A high-efficiency—typically >91% for a titanium-grade design—PSU converts and then distributes AC power (208 V or 240 V) to 48 V throughout the rack. The power distribution board (PDB) then converts DC power to various voltages, typically 12 V, 5 V, and 3.3 V, for feeding to subsystems including the motherboard, storage, network interface cards (NICs), and switches, and system cooling. Each of these subsystems, in turn, has its own locally managed power architecture. A battery backup unit (BBU) maintains system power during any AC line disruptions.
Designing for durabilityEach subsystem requires a reliable power design and monitoring. Let’s examine some of these subsystems further.
The PSUPSUs have several types of monitoring to ensure reliable operation and delivery. They monitor the AC mains’ output voltage while also detecting internal temperature, over- and under-voltage conditions, and short circuits.
Server designs also require N+1 redundancy: “N” represents the minimum number of necessary PSUs to meet server power needs. An additional PSU (“+1”) is available if one of the other PSUs encounters a temporary or permanent fault or failure.
The PDBAs mentioned earlier, the PDB converts a 48-V input to several DC rails, including 12 V, 5 V, and 3.3 V. Although comparators with simple shunt references can be used to monitor each of these rails for overvoltage and undervoltage conditions, modern-day voltage supervisors offer a small footprint and ease of design and provide additional benefits such as hysteresis and input-sense delay for noise immunity, an adjustable output delay to avoid false triggers during power up, and higher accuracy for the highest detection reliability.
Many new voltage supervisors, such as the Texas Instruments (TI) TPS3760, are rated for voltages as high as 70 V, and can monitor 48 V and other bus voltages directly without needing a low-dropout regulator or dedicated power rail. In addition to real-time supervision, advanced monitoring integrated circuits can provide telemetry data on the most vital rail voltages to enable predictive maintenance and historical fault analysis, significantly reducing system downtime.
Another design consideration is early power failure detection. These circuits monitor specific supply rails for sudden voltage drops and alert the host or processor to take swift action in anticipation of a power loss. A high-speed and precise undervoltage supervisor performs this function. Figure 2 illustrates an example of this type of design and its timing diagram.
Figure 2 A voltage supervisor example with a timing diagram, monitoring the 0.85 to 6.0 V supply rail for sudden voltage drops to take action in the event of a power loss. Source: Texas Instruments
The motherboardMotherboard power rails present designers with a different set of challenges, which I’ll examine in more detail in this section.
Processor rail monitoringModern processors are very sensitive to variations in their power supply rails. There are many reasons for this, but it is mostly because these processors operate at voltages as low as 0.7 V with reduced tolerance for voltage fluctuations and utilize features such as dynamic voltage and frequency scaling.
Consequently, the processors require high-precision window voltage supervisors. Window supervisors monitor the supply voltage for both overvoltage and undervoltage conditions. Devices targeted for these applications, such as TI’s TPS389006, have an accuracy of ±6 mV. Designers can adjust the glitch filter up to 650 ns through the I2C registers.
Another essential aspect of power-rail design is the system’s ability to maintain stability during rapid load transients. Modern processors can shift from idle to full load in microseconds, causing sharp voltage droops or overshoots if the power supply and monitoring systems are not designed with fast loop responses and the appropriate output capacitance.
Proper power-up and power-down supply sequencing is also essential for the motherboard and processor. Sequencing ensures proper system initialization—for instance, a processor may require that the memory controller be operational before executing instructions. Sequencing also prevents large inrush currents and voltage spikes during power-up. During power-down, sequencing maintains data integrity by giving memory and storage devices enough time to save data or complete operations before losing power.
Figure 3 provides a design example for the monitoring and sequencing of the supply rails.
Figure 3 Supply-rail monitoring and sequencing examples for proper system initialization. Source: Texas Instruments
Finally, managing inrush current is vital for systems with hot-swappable components to avoid tripping circuit protection or destabilizing the power bus. Hot-swap controllers equipped with integrated current limiting and fault detection ensure smooth insertion and removal without disrupting other active subsystems.
Future trendsThe enterprise industry is poised to transition to a 400 VDC power-distribution system, which would increase efficiencies by eliminating redundant power-conversion stages and I²R losses and reduce copper usage and costs. Such high-voltage systems will demand even more high-powered rail monitoring, with faster fault detection and isolation, to maintain safety and system uptime. A new generation of high-voltage monitoring solutions is emerging to address the future design needs in this space.
Compelling power architectures are essential for ensuring reliable and uninterrupted operation in enterprise systems. Combining solid power-design practices with real-time monitoring and early fault detection helps prevent unexpected failures and protects critical workloads. As system complexity grows and power architectures evolve, especially with the shift toward higher voltage distribution, careful planning and rail supervision will continue playing a role in delivering safe and efficient performance.
Masoud Beheshti leads application engineering and marketing for Linear Power at Texas Instruments. He brings extensive experience in power management, having held roles in system engineering, product line management, and marketing and applications leadership. Masoud holds a bachelor’s degree in electrical engineering from Ryerson University and an MBA with concentrations in marketing and finance from Southern Methodist University.
Related Content
- Power Tips #139: How to simplify AC/DC flyback design with a self-biased converter
- Data center power meets rising energy demands amid AI boom
- Data center next generation power supply solutions for improved efficiency
- Optimize data-center power delivery architecture
The post Power Tips #140: Designing a data center power architecture with supply and processor rail-monitoring solutions appeared first on EDN.
Clearing out the data clutter

I’ve been working on an article about vacuum tube triodes. Yes, they’re still being used in the manufacture of high-end audio equipment and in musical instrument amplifiers. A triode has three electrodes: a plate (in American parlance, “anode” in the UK), a control grid, and a cathode.
Figure 1 contains a typical graph of plate currents verses plate voltages for different grid voltages, with grid voltages labeled on each curve as 0, -0.5, -1. 0…-5.0. All voltages are with respect to the cathode. Pretty clear, right?
Figure 1 A typical graph of triode characteristics from a manufacturer’s datasheet.
Part of the article involves measuring triode characteristics and constructing graphs in Excel which display the measured data. Figure 2 shows the first attempt to present this graphically.
Figure 2 A simple display of the acquired data, the colors shown are defaults selected by Excel.
The data for the left-most curve was entered first; the one immediately to the right next, and so on. Excel assigns curve colors in the order shown by default. There doesn’t seem to be any order to the progression of colors that might aid in scanning through the LEGEND table on the right to find a curve’s grid-voltage name.
And some of the colors are so similar that it can be challenging to find the right association. There’s also no easy way to label the LEGEND table to indicate the type of information it contains other than adding a text box to the chart. But if you reposition the chart, the text box must be moved separately.
There must be a better way to convey this information to the reader. Suppose the colors could be changed to a more recognizable progression, such as the visible spectrum-related order of the color bands on a resistor which indicates its resistance. Furthermore, what if this reordering could be automated with a keyboard click for any chart? We’re talking Excel macros, right? We could manually make the change for one graph and record the steps as a macro. But we’d have to know how many curves a particular graph had to use such. Hmmm.
Ok, let’s instead create a macro using the subroutine “sub” feature in Excel’s built-in Visual Basic for Applications (VBA) code. The code should be easily able to handle a chart with any number of curves. Now, I’ve worked with VBA, but I’m no expert. So, when I come across a feature I need but I’m not familiar with, I have to do an online search, find a reference that I can understand, and apply and test it. Rinse and repeat. This is tedious. Is there a work-around for a time-crunched, lazy guy like me? Turns out the answer is yes: AI.
I asked one of these well-known beasts how I might automatically re-order the colors assigned to Excel chart curves. The code it returned in reply worked the first time and came with comments! I’ve made a few changes and added some comments of my own to produce the code listed in Appendix 1. Clicking to select the chart shown in Figure 2 and running this code produces the results seen in Figure 3.
Figure 3 The curve colors progress in the same order as the resistance color-code bands on resistors, and backgrounds were colored for better visibility of the yellow and white curves.
In addition to reordering the colors, the code has thickened the curves and added a background color of light grey for better visibility. All the code is commented, and the background and curve thicknesses can be easily modified. You’ll notice that there are eleven curves but only ten colors, so the -5.0-volt curve is the same color as the 0.0-volt curve; the colors automatically repeat.
But one of the features of the code is its ability to change what’s called the “dashstyle” of the curves each time the colors repeat. I believe that the code is adequately commented to allow a user to locate and modify or eliminate this behavior if desired.
Labeling the curves
I was happy with this until I looked back at the chart in Figure 1. Why refer to a legend on the side of the graph if I could put the grid-voltage curve names right next to the curves themselves? I went back to the AI engine to ask for help. This time, I got code that didn’t work the first time. But that didn’t stop me; when I described the problems I was seeing specifically, I got debugging help! Clicking to select the chart rendered in Figure 2, the Appendix 2 code produced the graph seen in Figure 4.
Figure 4 Each curve’s grid-voltage name is placed next to the end of the curve.
Maybe you’d like to combine effects by running the Appendix 1 code on Figure 4’s chart to produce that seen in Figure 5.
Figure 5 The Appendix 1 and Appendix 2 codes are run sequentially: first the code which appends the curve names near the ends of the curves, and then the code which reorders the curve colors.
There’s no longer any need for the legend box, so I manually deleted it after running the codes.
I found the two VBA programs presented in the first two Appendices to provide a simple, quick, and automatic means to enhance the readability of basic graphs in Excel. I’m keeping them in my Excel toolbox. For those unfamiliar with how to use VBA, Appendix 3 should prove helpful.
Christopher Paul has worked in various engineering positions in the communications industry for over 40 years.
Related Content
- Tell us your Tale
- What is the biggest mistake you have made as an engineer?
- Visualizing Data with Arduino
- PUT a reset in its place
Code to specify the colors assigned to curves on a chart. Select a chart and run the macro associated with this code.
Sub ApplySpectrumColors() Dim cht As Chart, series As series, i As Integer Dim colors_ As Variant, line_type As Variant, the_weight As Variant ' Define the spectrum colors as RGB values ' (see https://www.teoalida.com/wordpress/wp-content/uploads/Excel-colors-with-RGB-values-by-Teoalida.png) colors_ = Array(RGB(32, 0, 0), RGB(160, 140, 0), RGB(255, 128, 128), RGB(255, 192, 128), RGB(255, 255, 0), RGB(0, 192, 0), _ RGB(96, 255, 255), RGB(176, 96, 255), RGB(211, 211, 211), RGB(255, 255, 255)) ' Define the line types. See https://learn.microsoft.com/en-us/office/vba/api/office.msolinedashstyle line_type = Array(msoLineSolid, msoLineLongDash, msoLineDashDot, msoLineSquareDot) ' Define line_type weights (thicknesses) the_weight = Array(3, 3, 4, 4) ' Reference the active chart On Error Resume Next Set cht = ActiveChart On Error GoTo 0 If cht Is Nothing Then MsgBox "Please select a chart before running this script.", vbExclamation Exit Sub End If ' Loop through each series and assign spectrum colors,line styles and weights i = 0 For Each series In cht.SeriesCollection series.Format.Line.ForeColor.RGB = colors_(i Mod (UBound(colors_) + 1)) series.Format.Line.DashStyle = line_type(Int(i / (UBound(colors_) + 1)) Mod (UBound(line_type) + 1)) series.Format.Line.Weight = the_weight(Int(i / (UBound(colors_) + 1)) Mod (UBound(the_weight) + 1)) i = i + 1 Next series ' Change Plot Area Background Color cht.PlotArea.Format.Fill.ForeColor.RGB = RGB(236, 236, 236) ' Change Legend Background Color cht.Legend.Format.Fill.ForeColor.RGB = RGB(236, 236, 236) MsgBox "Spectrum colors applied successfully!", vbInformation End Sub APPENDIX 2Code to place the names of each curve next to that curve on a chart. Select a chart and run the macro associated with this code.
Sub LabelCurvesWithStyle() Dim cht As Chart, srs As series, pt As Point, i As Integer, seriesCount As Integer Dim validSeriesCount As Integer, lastValue As Variant On Error Resume Next Set cht = ActiveChart ' Get the active chart On Error GoTo 0 If cht Is Nothing Then ' If no chart is selected MsgBox "No chart is selected. Click on a chart and try again.", vbExclamation, "Error" Exit Sub End If seriesCount = cht.SeriesCollection.Count 'number of series in the chart validSeriesCount = 0 ' Loop through each series in the chart For Each srs In cht.SeriesCollection If srs.Points.Count > 0 Then i = srs.Points.Count ' Last point in the series lastValue = srs.Values(i) ' Get the last Y value ' Check if last value is numeric before labeling If IsNumeric(lastValue) And Not IsEmpty(lastValue) Then Set pt = srs.Points(i) ' Add a label pt.HasDataLabel = True pt.DataLabel.Text = srs.Name pt.DataLabel.Position = xlLabelPositionRight ' for otherlabel positions, see ' https://learn.microsoft.com/en-us/office/vba/api/Excel.XlDataLabelPosition With pt.DataLabel.Font ' Set font styling .Name = "Arial" ' Font type .Size = 10 ' Font size .Bold = True ' Make text bold .Color = RGB(255, 0, 0) ' Font color (Red) '.Italic = True ' Uncomment for italic text End With validSeriesCount = validSeriesCount + 1 Else MsgBox ("Series labeled " & srs.Name & " has non-numeric data.") End If End If Next srs If validSeriesCount < seriesCount Or validSeriesCount = 0 Then MsgBox "Non-numeric data found in at least one series. No labels applied." End If End Sub APPENDIX 3For those unfamiliar with Excel’s VBA, this AI-generated tutorial should be helpful.
The post Clearing out the data clutter appeared first on EDN.
Врятувати життя: тренінг у музеї
Серед цікавих експонатів старовинної техніки та вражаючих світлин присвяченої українським військовим, волонтерам і медикам виставки "Із полум'я зродились" у Державному політехнічному музеї імені Бориса Патона при КПІ ім.Ігоря Сікорського відбулась актуальна, особливо нині, подія.
Rohde & Schwarz pioneers the future of automotive Ethernet using Analog Devices’ 10BASE-T1S solutions
Rohde & Schwarz is accelerating the development of the new automotive Ethernet variant 10BASE-T1S by offering compliance and trigger & decode options
10BASE-T1S (IEEE 802.3cg) is a type of Ethernet networking technology that is designed for use in automotive and industrial applications, and 10BASE-T1S E2B products from ADI enable highly optimized yet flexible hardware-based Ethernet edge node connectivity solutions. The new variant is not just introducing a new lower speed grade of 10 Mbps over distances of 25 meters and beyond but also adding novel capabilities such as multi-drop transmission, thus eliminating the need for a switch. By eliminating the need for microcontrollers at the edge nodes, ADI’s E2B solution enables the centralization of all software to help enable next-gen zonal architectures and software-defined vehicles. This technological advancement is particularly applicable for linking sensors and actuators throughout the car body, powertrain, and beyond to a domain or zonal controller.
On the R&S MXO series oscilloscopes, the decoded packets are displayed in a color-coded manner, thereby making it straightforward for ADI engineers to identify crucial protocol messages such as Beacon, Commit and MAC frames. This allows for more efficient test validation, thus helping to enable shorter time to market. The 10BASE-T1S takes advantage of the new PLCA technology, making it essential to verify the timing and performance of various nodes connected onto the network. The time alignment of all decoded frames with the captured waveform simplifies debugging and facilitates precise timing measurements. ADI engineers can switch between various data representations such as DME symbols, scrambled, or unscrambled, providing valuable insights into the captured network traffic.
10BASE-T1S Ethernet technology offers additional advantages by supporting a high number of nodes on a single network, making it ideal for complex systems. Its short reach and low data-rate make it energy efficient and cost-effective. ADI’s innovative approach to 10BASE-T1S ensures that SDVs can deliver true value to OEMs by reducing form factors, cutting costs at the edge, lowering boot times, and offering bounded low latency, power saving, timestamping, and timed actuation, so that all nodes in the system are synchronized and operate seamlessly.
Fionn Hurley from ADI remarked: “ADI uses Rohde & Schwarz oscilloscopes, delivering reliable and precise measurements for our industry leading 10BASE-T1S solution. This reinforces our commitment to offering high-quality, robust technology solutions to our customers. ADI takes a holistic approach to system design and understands the complexity of the challenges faced by our customers and helps them overcome these challenges. We’re helping to drive the automotive industry towards a smarter, more efficient future.”
With the R&S MXO series oscilloscope, engineers can further leverage its high-performance capability to debug their 10BASE-T1S communication link. Standard debug tool like the spectrum mode, zone triggers and fast acquisitions makes it easy to detect anomalies on the bus. Furthermore, using the MXO’s ability to make standards-compliant 10BASE-T1S measurements in accordance with the IEEE 802.3cg and OPEN Alliance TC14 specifications, enables the automotive industry to ensure performance and interoperability of this growing automotive network technology.
The post Rohde & Schwarz pioneers the future of automotive Ethernet using Analog Devices’ 10BASE-T1S solutions appeared first on ELE Times.
UV-C LED disinfection system maker AquiSense closes Series A investment round
Firmware development: Redefining root cause analysis with AI

As semiconductor devices become smaller and more complex, the product development lifecycle grows increasingly intricate. So, from early builds to pre-qualification testing, firmware development and validation teams face escalating challenges in ensuring quality and performance. As a result, traditional root cause analysis (RCA) methods—performing manual checks, static rules, or post-mortem analysis—struggle to keep up with the complexity and velocity of modern firmware releases.
However, artificial intelligence (AI) and machine learning (ML) are changing the game. These technologies empower firmware teams to detect, diagnose, and prevent failures at scale—across performance testing, qualification cycles, and system integration—ushering in a new era of intelligent RCA.
But first let’s take a closer look at RCA challenges in firmware development.
RCA challenges in firmware development
RCA in firmware development, particularly for SSDs, is like finding a needle in a moving haystack. Engineers face several key challenges:
- Vast amounts of telemetry and debug logs: Firmware systems generate massive telemetry and debug logs. Manually sifting through this data to identify the root cause can be time-consuming, delaying development cycles.
- Elusive, intermittent failures: Firmware failures can be sporadic and difficult to reproduce, especially under high-stress conditions like heavy I/O workloads, making diagnosis even harder.
- Invisible code behavior changes: Minor firmware updates can introduce subtle issues that conventional diagnostics miss, complicating the identification of new bugs.
- Noisy, inconsistent defect signals: Defects often produce erratic and inconsistent signals, making it difficult to pinpoint the true source of failure without extensive testing.
These issues impact product timelines and customer qualifications. AI, rather than replacing engineers, enhances their ability to detect anomalies, reduce troubleshooting time, and improve the overall RCA process, speeding up diagnosis and uncovering hidden issues.
AI-driven approaches in RCA
Below are the AI techniques that streamline the RCA process, speeding up identification of root causes and improving firmware reliability.
- Anomaly detection: Unsupervised models like autoencoders and isolation forests detect abnormal patterns in real-time without requiring labeled failure data. These models learn normal behavior and flag deviations, helping to identify potential issues—like performance degradation—early in the process before they escalate.
- Predictive modeling: Machine learning algorithms such as XGBoost and neural networks analyze trends in historical test and telemetry data to predict future issues, like bugs or regressions. These models allow engineers to act proactively, preventing failures by predicting them before they occur.
- Correlation and pattern discovery: AI connects data across sources like test logs, code commits, and environmental factors to identify hidden relationships. It can pinpoint the root cause of issues faster by correlating failures with specific code changes, configurations, or conditions that traditional methods might overlook.
AI’s role in firmware validation
In firmware development—especially in NVMe devices and embedded systems—code changes can directly impact product stability and customer satisfaction. So, AI is now playing a critical role in this space.
- Monitoring I/O behavior: ML tracks latency, power, and throughput to flag regressions across firmware builds.
- Failure attribution: Historical test and return data are mined to correlate firmware changes with observed anomalies.
- Simulation: Generative models stress-test edge cases—such as power loss scenarios—to uncover potential flaws earlier in the cycle.
In an SSD development project, a firmware update intended to optimize memory management can cause subtle write workload failures during system integration. Traditional quality assurance (QA) can miss these failures, as they are intermittent and appear only under specific conditions.
However, Isolation Forest, an unsupervised machine learning model, is used to monitor real-time system behavior. The model detects timing anomalies tied to the firmware’s background garbage collection process by analyzing telemetry data, including latency and throughput. Isolation Forest identifies deviations from normal patterns, pinpointing the issues like delays introduced by changes in the garbage collection algorithm.
With these insights, engineers can root-cause and fix the issue within days, avoiding qualification delays. Without AI-based detection, there is a chance that this issue goes unnoticed, causing significant delays and customer qualification risks.
Benefits of AI-powered RCA
First and foremost, its speeds up the process by cutting debug time from weeks to hours. The AI-powered RCA also offers accuracy for multi-variable issues. Regarding scalability, it can monitor thousands of signals and logs continuously. Finally, the AI-powered RCA enables predictive action before issues reach customers.
Below is an outline of future directions for AI in RCA methods:
- Explainable AI for building trust in ML decisions.
- Multi-modal models for unifying logs, telemetry, images, and notes.
- Digital twins to simulate firmware behavior under varied scenarios.
AI is no longer optional; it’s becoming central to firmware development. On the other hand, root cause analysis is evolving into a fast, intelligent, and predictive practice. So, as firmware complexity grows, those who harness AI will lead in reliability and time-to-market.
For engineers, adopting AI isn’t about surrendering control—it’s about unlocking superhuman diagnostic capability.
Karan Puniani is a staff test engineer at Micron Technology.
Related Content
- 5 Tips for speeding firmware development
- Development tool evolution – hardware/firmware
- Use virtual machines to ease firmware development
- Will Generative AI Help or Harm Embedded Software Developers?
- No code: Passing Fad or Gaining Adoption for Embedded Development?
The post Firmware development: Redefining root cause analysis with AI appeared first on EDN.
Fraunhofer IAF presents bidirectional 1200V GaN switch with integrated free-wheeling diodes
Keysight Awarded NATO FORACS Contract to Enhance Operational Readiness
- Provides advanced radar target generation and EW threat simulation solutions to strengthen NATO’s radar and electronic support measures capabilities across member nations
Keysight Technologies. Inc. has been awarded a contract with NATO’s Naval Forces Sensor and Weapons Accuracy Check Sites to modernize its testing capabilities for critical radar and electronic support measures systems. Under this agreement, Keysight will deliver Radar Target Generator and Electronic Warfare testing solutions to be deployed at NATO Navy bases, enabling the calibration and maintenance of NATO radar systems and the assessment of ESM effectiveness.
Modern military and naval forces depend heavily on the accuracy and reliability of their radar and ESM systems for maintaining situational awareness, effective targeting, and timely threat detection. In an era of increasingly complex and rapidly evolving electronic warfare threats, defense organizations require sophisticated, high-fidelity test environments. These environments must be capable of replicating real-world scenarios with dynamic multi-emitter signals, advanced threat modeling, and closed loop testing methodologies.
Keysight’s Radar Target Generator and EW solutions are designed to meet these demanding requirements, empowering NATO FORACS to rigorously assess and optimize the operational readiness of radar and ESM systems across all member nations. The contract encompasses the integration and delivery of next-generation Radar Target Generators and EW threat simulators. This will ensure enhanced accuracy verification and thorough system performance testing within complex electromagnetic environments. Notably, the Radar Target Generator leverages commercial-off-the-shelf Keysight components, featuring customized firmware and a graphical user interface developed entirely in Europe and tailored to meet NATO’s specific requirements.
The systems that Keysight will deliver to NATO is defined by several key factors, including:
- High-fidelity Radar Target Generation: Simulates precise radar returns, including Doppler shift, range, and cross-section variability, enabling accurate testing of radar tracking.
- Sophisticated EW threat simulation: Creates complex electromagnetic threat environments with multi-emitter interference, jamming, and deceptive techniques to evaluate ESM system effectiveness.
- Customizable, open-architecture design: The modular hardware and software framework allows for incremental system upgrades, ensuring adaptability to future mission requirements.
- Deployable and modular configuration: Designed for field and lab deployment, providing flexible testing capability across multiple NATO sites.
The NATO FORACS Office in NATO Headquarters in Brussels, reported: “The NATO FORACS Office is pleased to note the placement of this contract which will supply important equipment to restore NATO FORACS’ core radar and ESM testing capabilities in order to meet its users’ evolving demands.”
Thierry Locquette, EMEA VP and GM at Keysight, said: “NATO’s ability to verify and enhance the accuracy of its radar and ESM systems is critical to mission success in today’s contested electromagnetic spectrum environment. Keysight is proud to provide the cutting-edge solutions necessary to enable NATO FORACS to maintain the highest levels of sensor performance, ensuring operational superiority across allied forces. Our Radar Target Generator solution was developed in Europe, working closely with our local R&D and solution centers as well as with European technology partners to provide a highly realistic, flexible, and future-ready test capability for NATO’s evolving defense needs.”
The post Keysight Awarded NATO FORACS Contract to Enhance Operational Readiness appeared first on ELE Times.
Wise-integration to Present a SiC 7kW Demoboard for Onboard Charger For Electric Vehicles with WiseWare Digital Control at PCIM 2025
The Cross-Compatible OBC Enables Flexible, Efficient, And Intelligent Power Systems Across Multiple Wide-Bandgap Platforms
Wise-integration, a pioneer in digital control for gallium nitride (GaN) and GaN IC-based power supplies, will break new ground at PCIM Europe 2025, May 6–8 in Nuremberg. In collaboration with Savoy International Group, the company will debut its digital controller of a silicon carbide (SiC) power demonstrator model, underscoring its expansion into complementary wide-bandgap technologies and showcasing its WiseWare digital controller’s universality and adaptability across those technologies.
This marks a new market entry for Wise-integration—in particular, targeting SiC-based high-voltage applications in automotive and industrial sectors—while reinforcing that WiseWare can serve as a common digital intelligence layer regardless of the underlying semiconductor material.
Building on Wise-integration’s Core GaN Expertise
The WiseWare 1 OBC SIC 7kW power demonstrator model builds on the company’s core expertise in GaN-based systems and digital control ICs, reinforcing its commitment to advancing the full spectrum of power semiconductor technologies. This cross-compatible, digital control solution for both GaN and SiC, enables flexible, efficient, and intelligent power systems across multiple WBG platforms.
“This demonstration of a silicon-carbide onboard charger marks an important step in Wise-integration’s journey toward the automotive market,” said CEO Thierry Bouchet. “By showing that WiseWare can reliably control high-voltage, high-power systems in an EV-relevant application, we’re validating our digital control platform as a strong candidate for next-generation onboard chargers. It’s a first step toward demonstrating that our technology is scalable, adaptable, and aligned with the needs of future EV platforms.”
The demonstrator is a prototype product for the company’s partner, Savoy International Group, a Tier 1 automotive supplier, whose e-mobility division collaborated with Wise-integration on a GaN charger embedded in e-bike batteries in 2023.
“This prototype has been developed specifically to support the electrification of Savoy’s innovative, light electric vehicles under the KILOW brand, as well as their broader ambition to promote fun, accessible, and sustainable mobility solutions,” Bouchet explained.
“Our previous collaboration with Wise-integration on the embedded GaN charger for our e-bike battery met all of our expectations for performance and helps us differentiate KILOW in a crowded field,” said Émile Allamand, CEO of Savoy Group. “The SiC onboard charger will enable us to diversify our EV offerings with a light, four-wheel vehicle under our KILOW brand.”
Major Differentiators of the WiseWare 1 OBC SIC 7kW Demonstrator:
- Technology-agnostic control:WiseWare works seamlessly with both GaN and SiC, allowing OEMs to keep control architecture constant, while optimizing the power stage for each use case (cost, power level, thermal profile, etc.).
- Digital-first approach:Unlike traditional analog control platforms, Wise-integration virtualizes control functions, enabling simplified designs, faster iterations, and more compact systems.
- Open and modular design philosophy:WiseWare is not tied to a proprietary microcontroller or switch brand. This flexibility makes it highly attractive to Tier 1s and system integrators seeking to reduce vendor lock-in.
SiC technology delivers excellent thermal performance and is highly efficient under heavy loads—making it ideal for high-power components like traction inverters and fast chargers. Its ruggedness and maturity also contribute to its reliability in the demanding automotive environment. WiseWare’s SiC demonstration shows that the company’s digital control platform is technology-agnostic, and can bring the same performance, modularity, and intelligence to SiC systems as it does to GaN systems.
The post Wise-integration to Present a SiC 7kW Demoboard for Onboard Charger For Electric Vehicles with WiseWare Digital Control at PCIM 2025 appeared first on ELE Times.
Rohde & Schwarz presents its advanced solutions for power electronics testing and characterization at PCIM Expo 2025
Rohde & Schwarz will showcase its latest solutions and advanced techniques for testing and analyzing power electronic systems and components at PCIM Expo 2025 in Nuremberg, Germany. At the company’s booth (hall 7, booth 166), the spotlight will be on solutions utilizing the company’s cutting-edge test instruments to address the challenges of debugging next generation wide bandgap semiconductors like GaN and SiC.
Rigorous testing and advanced characterization methods help design engineers enhance the performance, efficiency, and reliability of their power electronic designs based on SiC and GaN devices, used in pioneering industries like e-mobility, renewable energy or AI data centers. Rohde & Schwarz will bring a selection of its comprehensive T&M portfolio to booth 166 in hall 7 of PCIM Expo 2025, taking place from May 6 to 8 at the Nuremberg Exhibition Center. The test solutions are tailored for power electronics applications where high efficiency, fast switching speeds, improved power density and high-temperature operation matter.
Wide bandgap analysis
At the center of the presented setups will be the R&S RT-ZISO isolated probing system from Rohde & Schwarz. This next generation isolated probe has set new standards with unprecedented accuracy, sensitivity, dynamic range and bandwidth for wide bandgap power designs with SiC and GaN. Rohde & Schwarz will showcase the advantage of the R&S RT-ZISO over single-ended probes in a setup to investigate the switching behavior of a GaN-MosFET.
Double pulse testing
Double pulse testing is a method for evaluating the switching performance of SiC and GaN based power devices. Rohde & Schwarz is collaborating with industry expert PE-Systems GmbH for a stable and accurate approach to double pulse testing using the MXO 5 next generation oscilloscope from Rohde & Schwarz with eight channels in combination with the R&S RT-ZISO. At PCIM, visitors can experience accurate, reliable and fast double pulse testing on 1200 V SiC devices from Wolfspeed, typically used as traction inverters in the automotive industry.
Automated loadjump testing
Loadjump testing used to be a time-consuming manual process to verify a Buck converter’s load step response at varying input voltage levels, using only a few reference points. For this application, as well, Rohde & Schwarz collaborates with PE-Systems GmbH, who offers a test automation software. In combination with the MXO 5 oscilloscope and the R&S RT-ZISO isolated probing system, this solution not only reduces overall testing time but also maintains the same number of test points. At PCIM, the companies demonstrate automated loadjump testing of a Buck converter of Monolithic Power Systems, Inc. within a voltage range of 6V to 60V. The setup even allows for more reference points within the same timeframe and can be extended to include temperature control, facilitating the full automation of input voltage, load current, and temperature profile variations.
Component characterization
Rohde & Schwarz will also showcase its solutions for component characterization. The R&S LCX LCR meters with customized impedance measurement functions are suitable for all discrete passive components up to 10 MHz. Users can easily characterize the voltage dependence of capacitances in core components of power converters like MLCCs with the R&S LCX. Combined with a sweep software tool, users can perform comprehensive sweep measurements and display them in numerous charts. The MFIA impedance analyzer from Zurich Instruments AG is capable of impedance spectroscopy for both low impedance components such as shunt resistors and DC-link capacitors and high impedance systems. It offers measurement modes for impedance analysis over frequency and time as well as other features such as integrated oscilloscope and spectrum analyzer capabilities.
Dr. Philipp Weigell, Vice President of the Industry, Components, Research & University Market Segment at Rohde & Schwarz, explains: “PCIM Expo is an important venue for us to highlight our advancements in wide bandgap semiconductor testing. Testing plays a critical role to improve power efficiency, reduce size, and manage heat more effectively in power conversion applications used in AI data centers, for instance. Through collaboration with industry experts and with our advanced testing solutions we enable our customers to develop reliable and efficient systems that meet the rigorous demands of modern data processing applications.”
The post Rohde & Schwarz presents its advanced solutions for power electronics testing and characterization at PCIM Expo 2025 appeared first on ELE Times.
Exporting Power: India’s Growing Influence In Global Transformer Supply Chains
Written By: Mr. Rajesh Patawari, Managing Director, National Electrical Equipments Corporation
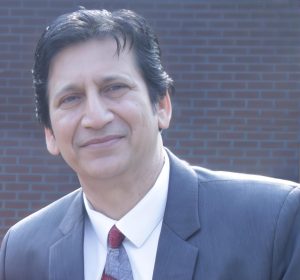
In the intricate world of global energy infrastructure, transformers are essential components, quietly enabling the smooth transmission and distribution of electrical power. These devices are the backbone of energy systems, ensuring that power reaches homes, industries, and businesses across the globe. For decades, countries like China, Germany, and the United States have been the dominant forces in transformer manufacturing, but in recent years, India has been making significant strides in this industry. The country’s growing presence in global transformer supply chains signals a shift that is both intriguing and indicative of its rising industrial influence.
In 2023, India’s export of electrical transformers reached a new peak, totaling $3.59 billion, marking the country as the 10th largest exporter of transformers worldwide. The United States was the largest importer, purchasing $1.02 billion worth of transformers from India, with other nations like the Netherlands, China, and the UK following closely behind. These figures are not just impressive in isolation; they represent a clear upward trajectory, with exports to markets like the Netherlands increasing by 41% compared to previous years. This consistent growth highlights India’s expanding role as a global supplier of high-quality transformers.
What makes India’s emergence in the transformer market particularly noteworthy is the variety of products it now exports. While transformers themselves form the core of these exports, India has also made significant headway in exporting transformer parts and components. In 2023, exports of transformer parts and static converters amounted to $449 million. The United States remained the largest importer of these components, followed by markets in the Middle East and Europe. This expanding product range speaks volumes about India’s ability to meet the varied demands of different international markets, showcasing both its technical expertise and adaptability.
India’s success in this sector is not just about increasing export volume. The country has effectively entered new markets, some of which were previously dominated by other manufacturers. While the US and Europe remain key markets, India is increasingly making inroads into emerging markets like Mexico, Bangladesh, and Hong Kong. This wider market penetration is a reflection of India’s growing reputation for delivering reliable, cost-effective transformers that meet international standards. It’s not just about competing with established players; it’s about carving out a space in markets that are essential for global energy development.
The competitive landscape is still challenging, with countries like China and Germany leading in overall transformer exports. However, India’s increasing share of the global market demonstrates that it can compete on quality and cost, two critical factors that play a central role in today’s global supply chains. While the larger manufacturers may have the advantage in volume, India’s focus on producing high-quality, affordable products has resonated with many customers worldwide.
Domestically, the Indian transformer market remains strong, valued at over INR 12,000 crore, with power transformers and distribution transformers making up nearly equal shares. Although the country faces challenges, such as a slowdown in power generation and transmission infrastructure development, the transformer sector continues to show steady growth. This stability in the domestic market provides India with a solid foundation to build its export capabilities, as the country’s manufacturing and logistics networks continue to improve.
Looking forward, India’s role in global transformer supply chains is set to grow even more. With the world increasingly focused on renewable energy and sustainable power systems, the demand for efficient and reliable transformers will continue to rise. India’s growing manufacturing capabilities, combined with its expanding market presence, position it to meet this global demand. As the country strengthens its energy infrastructure and develops more advanced technologies, its ability to supply transformers for green energy projects, such as wind and solar power, will become even more important.
The future of India’s transformer industry appears bright, with further growth expected in both domestic and international markets. As the world shifts toward cleaner energy, the need for reliable transformers will only increase, and India is well-positioned to meet that demand. The country’s growing presence in global supply chains is a sign of its increasing industrial capabilities and its determination to be a key player in the future of global energy systems. In the years to come, India’s role in transforming the world’s power infrastructure will be one to watch.
The post Exporting Power: India’s Growing Influence In Global Transformer Supply Chains appeared first on ELE Times.
Pages
