Українською
  In English
Feed aggregator
Infineon and the BSI pave the way for a quantum-resilient future: World’s first Common Criteria Certification for post-quantum cryptography algorithm on a security controller
- Infineon receives world’s first Common Criteria EAL6 certification for implementing a post-quantum cryptography (PQC) algorithm in a security controller
- Internationally accepted certification is a crucial step towards a quantum-resilient world
- Post-quantum cryptography supports the protection of digital infrastructure from the future threats of quantum computers
Infineon Technologies AG has achieved a milestone on the way to a quantum-resilient world in collaboration with the German Federal Office for Information Security (BSI). Infineon is the first company ever to receive the Common Criteria EAL6, an industry-leading certification level, for the implementation of a post-quantum cryptography algorithm in a security controller. Such cryptography enhances security for eSIM, 5G SIM and smart card applications, including personal IDs, payment cards and eHealth cards, against threats resulting from highly capable quantum computers. The world’s first certification is a milestone on the way to a quantum-safe future in our daily lives.
Within the next ten to twenty years, quantum computers are expected to become powerful enough to break current cryptographic algorithms, compromising the security of our digital lives. Documents like eIDs that currently being issued and are valid for many years need to be resistant against future attacks by quantum computers. The same is true of encrypted messages and emails that are sent now, because when stored these can be attacked by quantum computers later. Post-quantum cryptography algorithms such as Module-Lattice-Based Key Encapsulation Mechanisms (ML-KEM) are designed to resist these attacks, fortifying the integrity of our digital infrastructure. A secured implementation of these algorithms is crucial to withstanding classical security attacks.
Infineon’s latest achievement demonstrates the company’s commitment to providing future-proof security solutions. “With our innovations in post-quantum cryptography and active contribution to algorithm development, Infineon is an integral part in finding future-proof PQC solutions,” said Thomas Rosteck, Division President Connected Secure Systems at Infineon. “There is no question that quantum computers will be a reality; Therefore, we need to push forward with the migration to post-quantum cryptography decisively. Being the first company to receive the Common Criteria EAL 6 certification for post-quantum security is a testament to our dedication in protecting critical infrastructure and helping maintain the security of our customers’ data in a post-quantum world. This once again underpins Infineon’s leadership in the security industry.”
“The threats posed by quantum computers are becoming more and more real and are within reach,” said Claudia Plattner, President of the German Federal Office for Information Security (BSI). “The BSI consistently supports and demands the switch to post-quantum cryptography in order to make files and applications secure in the long term. The availability of quantum-safe IT products, which can also be found in numerous everyday applications, is therefore a real milestone!”
The international Common Criteria standard sets guidelines and criteria for the security of IT products and systems and is internationally recognized. By certifying Infineon’s secured implementation of a PQC algorithm with Common Criteria EAL 6, the BSI underlines the importance of resistance against classic attacks, like fault attacks, as well as quantum computer attacks. The ML-KEM algorithm was implemented on a TEGRION security controller, Infineon’s latest brand of 28 nm security controllers based on Infineon’s revolutionary security architecture Integrity Guard 32. The Common Criteria scheme was developed in collaboration among various governments and is recognized by governments around the globe. The certification itself takes place through various national institutions. Infineon’s TEGRION security controller has been evaluated and certified by the German BSI under the German Certification scheme.
EAL6 is a highly advanced level of assurance, indicating that the product or system has undergone a comprehensive and rigorous evaluation to confirm its security claims. The certified security controller combines high-performance processing with advanced cryptographic capabilities, providing a robust foundation for post-quantum cryptography. With this certification, Infineon is setting a new standard for the industry, paving the way for widespread adoption of post-quantum cryptography and for a safer digital future. And with the PQC era approaching fast, Infineon will continue working on further and more advanced quantum-resistant solutions.
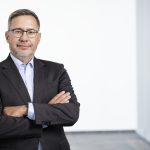
The post Infineon and the BSI pave the way for a quantum-resilient future: World’s first Common Criteria Certification for post-quantum cryptography algorithm on a security controller appeared first on ELE Times.
MACOM signs preliminary memorandum of terms for US CHIPS Act funding
Звіт проректора з адміністративно-фінансової роботи КПІ ім. Ігоря Сікорського Сергія Манзюка
Робимо КПІ краще!
Нещодавно на засіданні Вченої ради розпочалися звіти проректорів. Першим був представлений звіт проректора з адміністративно-фінансової роботи КПІ ім. Ігоря Сікорського Сергія Манзюка.
Rohde & Schwarz presents R&S ScopeStudio, a PC-based oscilloscope solution to boost development teams
Rohde & Schwarz enhances its oscilloscope offerings with the launch of R&S ScopeStudio, an innovative application that brings the functionality of the MXO series oscilloscopes to a PC, often a more convenient and effective workspace. This advanced solution allows engineers to visualize, analyze, document and share oscilloscope measurements, making development teams more efficient.
R&S®ScopeStudio is a new software solution from Rohde & Schwarz that transfers the capabilities of the MXO series oscilloscopes to a computer. This PC-based oscilloscope application facilitates the viewing, analysis, documentation and sharing of oscilloscope measurements away from the oscilloscope hardware, presenting a more accessible solution for individual users and development teams.
Users can import oscilloscope waveforms or entire sessions – a blend of captured waveform data and instrument setup files. The subsequent measurements and analysis capabilities mirror what a user would experience on their MXO oscilloscope. However, the application offers three key advantages. First, since users can view and analyze previously acquired data away from the instrument, it leaves the oscilloscope free for others to use. Second, engineers can use PC tools to more efficiently document designs. This not only enhances productivity but also improves the quality of images and annotations by leveraging the flexibility of additional PC resources. Finally, research and development teams can share measurement results more effectively with remote locations, partners, suppliers and customers. The need to share technical measurement details is common in development teams, and this PC-based oscilloscope application simplifies the process.
The standard features of the application include R&S SmartGrid, cursors, over 40 automated measurements, mathematical functions, filters and spectrum viewing of time-domain signals. Protocol decoding support for I2C, SPI, RS-232/UART, CAN, CAN-FD, CAN-FL, LIN, SENT, MilStd 1553, ARINC 429 and SPMI serial buses will be available soon.
The new R&S ScopeStudio PC application software for the R&SMXO 4 , R&SMXO 5 and R&SMXO 5C oscilloscopes is now available from Rohde & Schwarz with perpetual licenses priced at EUR 550.
The post Rohde & Schwarz presents R&S ScopeStudio, a PC-based oscilloscope solution to boost development teams appeared first on ELE Times.
The Future is Connected Embracing the Advanced Communication Revolution
A complex web of communication systems inextricably links the modern world. From the simple act of placing a phone call to the intricate orchestration of global data networks, these systems have become the lifeblood of our societies, driving innovation and shaping every aspect of our lives.
Advanced communication systems are not only driving technological progress but are also shaping industries, economies, and lifestyles. However, the relentless march of technological progress demands a constant evolution of these systems to meet the ever-growing demands of a hyper-connected world.
From the rapid expansion of 5G to the groundbreaking development of quantum communication, this article explores the latest advancements, challenges, and transformative potential of these systems.
Evolution of Communication SystemsThe journey of communication systems has been marked by exponential growth, from basic telegraphs to sophisticated wireless networks. Each generation of communication technology has introduced faster speeds, higher reliability, and greater accessibility:
- 1G to 4G: Early systems focused on enabling voice communication, followed by text and basic data services. The advent of 4G revolutionized mobile broadband with faster internet and video streaming capabilities.
- 5G Revolution: The fifth generation (5G) marked a paradigm shift, enabling ultra-low latency, high-speed connectivity, and massive device interconnectivity.
As the world moves beyond 5G, research on 6G and other cutting-edge technologies is gaining momentum, promising to redefine communication systems yet again.
Key Advancements in Communication Systems- 5G and Beyond
5G networks are unlocking new possibilities across industries, with key features such as enhanced Mobile Broadband (eMBB), Ultra-Reliable Low-Latency Communication (URLLC), and massive Machine-Type Communication (mMTC). These capabilities are driving applications like autonomous vehicles, smart cities, and industrial automation.
Looking ahead, 6G networks are projected to offer:
- Terahertz (THz) frequency bands for ultra-high data rates.
- AI-driven network optimization.
- Integration of communication and sensing for applications like precision healthcare and environmental monitoring.
- Quantum Communication
Quantum communication is emerging as a revolutionary technology for secure data transmission. Leveraging the principles of quantum mechanics, such as superposition and entanglement, it ensures unparalleled security through Quantum Key Distribution (QKD). Recent advancements include:
- Satellite-based quantum communication networks, exemplified by China’s Micius satellite.
- Integration of quantum repeaters to extend the range of quantum networks.
- Satellite Communication
The rise of Low Earth Orbit (LEO) satellite constellations, such as SpaceX’s Starlink and OneWeb, is transforming global connectivity. These systems offer high-speed internet to remote and underserved regions, addressing the digital divide. Advancements in phased-array antennas and laser-based inter-satellite links are further enhancing satellite communication capabilities.
- Software-Defined Networking (SDN) and Network Function Virtualization (NFV)
SDN and NFV are revolutionizing network architecture by decoupling hardware from software. These technologies enable:
- Dynamic network management and traffic optimization.
- Cost-efficient deployment of virtualized network functions (VNFs).
- Faster rollout of updates and new services.
- Artificial Intelligence and Machine Learning
AI and ML are becoming integral to modern communication systems, enhancing efficiency, reliability, and adaptability. Key applications include:
- Predictive network maintenance to minimize downtime.
- Intelligent resource allocation for optimized bandwidth usage.
- Real-time anomaly detection and cybersecurity.
- Optical Communication
Optical communication, leveraging fibre-optic technology, continues to advance with innovations such as:
- Multi-core and hollow-core fibres for higher data transmission rates.
- Free-space optical communication (FSO) for wireless, high-speed data transfer.
- Integration with 5G networks for enhanced backhaul and fronthaul.
- Healthcare
Telemedicine, remote patient monitoring, and robotic surgeries are becoming more feasible with advanced communication technologies. For instance:
- 5G networks support real-time video consultations and transmission of high-resolution medical imaging.
- IoT-enabled medical devices ensure continuous health monitoring and timely alerts.
- Autonomous Systems
From self-driving cars to unmanned aerial vehicles (UAVs), advanced communication systems are critical for enabling autonomy. Ultra-reliable and low-latency networks ensure seamless data exchange between devices, improving safety and efficiency.
- Smart Cities
Smart cities rely on interconnected systems to optimize urban infrastructure. Advanced communication systems enable:
- Smart grid management for energy efficiency.
- Intelligent transportation systems (ITS) to reduce traffic congestion.
- Real-time environmental monitoring and disaster response.
- Industrial Automation
Industry 4.0 is driven by advanced communication technologies that facilitate:
- Real-time data exchange between machines, robots, and sensors.
- Predictive maintenance to reduce downtime and operational costs.
- Digital twins for process simulation and optimization.
- Spectrum Scarcity
The increasing demand for wireless communication is putting pressure on the available radio frequency spectrum. Efficient spectrum management and the exploration of higher frequency bands, such as millimeter waves and THz waves, are crucial to address this issue.
- Security and Privacy
As networks become more interconnected, they become more vulnerable to cyberattacks. Ensuring robust encryption, secure authentication protocols, and real-time threat detection is imperative.
- Infrastructure Costs
Deploying advanced communication networks, especially in remote or underserved areas, involves significant investment. Innovations in cost-effective technologies and public-private partnerships are needed to bridge this gap.
- Environmental Impact
The energy consumption of communication networks is rising with the proliferation of data-intensive applications. Developing energy-efficient network components and leveraging renewable energy sources are essential for sustainable growth.
Future Directions- Integration of AI and 6G
The synergy between AI and 6G will enable intelligent and adaptive networks, capable of self-optimization and self-healing. AI-driven communication systems will also support advanced applications such as immersive extended reality (XR) and holographic telepresence.
- Global Quantum Internet
The vision of a global quantum internet is becoming a reality, with efforts focused on building scalable quantum networks. This technology will redefine secure communication, scientific research, and even financial systems.
- Interplanetary Communication
As space exploration intensifies, advanced communication systems are being developed to support interplanetary missions. NASA’s Deep Space Optical Communications (DSOC) project aims to enable high-speed data transmission between Earth and spacecraft.
- Convergence of Technologies
The convergence of communication, computing, and sensing technologies will lead to new paradigms, such as the Internet of Everything (IoE), where devices, data, and humans interact seamlessly.
ConclusionAdvanced communication systems are transforming the way we connect, collaborate, and innovate. By pushing the boundaries of speed, security, and scalability, these technologies are laying the foundation for a smarter and more sustainable future. As we navigate the complexities of deployment and adoption, a focus on innovation, inclusivity, and sustainability will be critical in harnessing the full potential of advanced communication systems.
The post The Future is Connected Embracing the Advanced Communication Revolution appeared first on ELE Times.
Quintessent and IQE establish quantum dot laser & SOA epiwafer supply chain for AI optical interconnects
📰 Газета "Київський політехнік" № 3-4 за 2025 (.pdf)
Вийшов 3-4 номер газети "Київський політехнік" за 2025 рік
The Race to Net-Zero: Accelerating Efficiency & Renewables
The escalating global energy crisis, coupled with the urgent need to mitigate climate change, demands a radical shift in our energy consumption patterns. This necessitates a two-pronged approach: enhancing energy efficiency and transitioning to low-carbon emission sources. These two facets are not mutually exclusive but rather symbiotic, driving a virtuous cycle of sustainability.
In the era of climate change and environmental challenges, the twin goals of enhancing energy efficiency and reducing carbon emissions have become pivotal for global sustainability. As industries, governments, and researchers seek solutions to minimize ecological footprints, advancements in technology and policy innovations have opened new pathways toward achieving these goals. This article delves into the latest trends, strategies, and technologies in energy efficiency and low carbon emissions, shedding light on their implications for a sustainable future.
The Energy-Carbon NexusEnergy consumption is a primary contributor to greenhouse gas (GHG) emissions, particularly from sectors such as power generation, transportation, and manufacturing. According to the International Energy Agency (IEA), energy-related CO2 emissions account for nearly 75% of global GHG emissions. Tackling this issue requires a dual approach: improving energy efficiency to reduce consumption and transitioning to low-carbon energy sources.
Innovations Driving Energy Efficiency- Smart Grids and IoT Integration
Smart grids leverage Internet of Things (IoT) devices, sensors, and real-time analytics to optimize energy distribution and consumption. These grids enable demand response strategies, where electricity usage is adjusted based on supply conditions, reducing waste and enhancing grid stability. For instance, smart thermostats and lighting systems can significantly cut residential and commercial energy usage.
- Advanced Building Technologies
Buildings account for 40% of global energy consumption. Modern energy-efficient building materials, such as aerogels and phase-change materials, provide superior insulation and thermal regulation. Additionally, building automation systems (BAS) equipped with AI algorithms can optimize HVAC (heating, ventilation, and air conditioning) systems, further reducing energy needs.
- High-Efficiency Industrial Processes
Industrial processes are energy-intensive, but advancements in technologies like waste heat recovery, precision manufacturing, and energy-efficient motors have made significant progress. For example, deploying variable frequency drives (VFDs) in motor systems can reduce energy consumption by 30-50%.
- Electrification of End-Uses
The electrification of transportation, heating, and cooking—coupled with clean electricity—is a cornerstone of energy efficiency. Electric vehicles (EVs), heat pumps, and induction stoves consume less energy compared to their fossil fuel-based counterparts while eliminating direct emissions.
Decarbonizing the Energy SectorThe transition to low-carbon energy sources is critical for achieving global climate goals. Recent innovations are accelerating this shift:
- Renewable Energy Expansion
The deployment of solar, wind, and hydropower technologies has reached unprecedented levels. Innovations in photovoltaic (PV) materials, such as perovskite solar cells, promise higher efficiency and lower production costs. Offshore wind turbines with capacities exceeding 15 MW are now operational, significantly enhancing energy output.
- Green Hydrogen
Green hydrogen, produced via electrolysis powered by renewable energy, is emerging as a versatile solution for decarbonizing hard-to-abate sectors like steelmaking, aviation, and maritime transport. Recent advancements in electrolyzer efficiency and cost reduction have accelerated its adoption.
- Energy Storage Technologies
The intermittent nature of renewable energy necessitates robust storage solutions. Lithium-ion batteries dominate the market, but next-generation technologies such as solid-state batteries, redox flow batteries, and gravity-based storage systems are gaining traction. These innovations promise longer lifespans, higher energy densities, and reduced environmental impacts.
- Carbon Capture, Utilization, and Storage (CCUS)
CCUS technologies capture CO2 emissions from industrial and power generation processes, preventing them from entering the atmosphere. The captured CO2 can be utilized to produce synthetic fuels, chemicals, or building materials, creating a circular carbon economy. Companies like Climeworks and CarbonCure are pioneering such solutions.
Policy and Market DriversGovernments worldwide are implementing policies to incentivize energy efficiency and low-carbon technologies. Examples include:
- Carbon Pricing Mechanisms: Carbon taxes and cap-and-trade systems encourage industries to reduce emissions by assigning a cost to carbon pollution.
- Energy Efficiency Standards: Mandates for appliances, vehicles, and industrial equipment ensure a baseline level of efficiency.
- Renewable Energy Targets: Countries like India, Germany, and the United States have set ambitious goals for renewable energy capacity.
- Green Financing: Initiatives like green bonds and sustainability-linked loans provide capital for clean energy projects.
Despite progress, significant barriers remain. The high upfront costs of energy-efficient technologies and renewables can deter adoption, particularly in developing regions. Additionally, integrating high shares of renewables into the grid poses technical challenges related to stability and storage.
These challenges also offer opportunities for innovation and investment. Digital twins, for instance, enable virtual simulations of energy systems, optimizing design and operations. Artificial intelligence (AI) and machine learning (ML) are being harnessed to predict energy demand, optimize renewable integration, and enhance grid resilience.
Case Studies: Real-World Impacts- Singapore’s Green Building Initiative
Singapore has implemented stringent green building standards, leading to a 28% reduction in energy consumption per building. The city-state’s Green Mark certification incentivizes energy-efficient designs and retrofits, demonstrating the impact of policy-driven action.
- Tesla’s Energy Ecosystem
Tesla’s integrated approach—combining solar panels, battery storage, and EVs—offers a glimpse into a sustainable energy future. The company’s Gigafactories focus on scaling production while reducing costs, making clean energy solutions more accessible.
- Europe’s Offshore Wind Success
Europe’s offshore wind sector exemplifies the potential of renewable energy. Projects like Dogger Bank in the UK, set to be the world’s largest offshore wind farm, highlight advancements in turbine technology and supply chain efficiencies.
The Road AheadAchieving a sustainable, low-carbon future requires collective effort across sectors. Key priorities include:
- Scaling Innovation: Continued research and development are crucial to drive down costs and improve performance.
- Equitable Access: Ensuring that developing nations benefit from clean technologies and financing mechanisms is essential for global impact.
- Collaboration: Partnerships between governments, private sectors, and academia can accelerate deployment and knowledge sharing.
- Behavioral Change: Public awareness campaigns and incentives can encourage energy-saving behaviors and adoption of clean technologies.
Energy efficiency and low carbon emissions are not just environmental imperatives but also economic opportunities. By embracing cutting-edge technologies, fostering policy innovation, and promoting global collaboration, we can pave the way for a resilient and sustainable future. As we stand at the crossroads of energy transformation, the choices we make today will shape the world for generations to come.
The post The Race to Net-Zero: Accelerating Efficiency & Renewables appeared first on ELE Times.
One of the old parts still hanging around.
![]() | If there's interest I'll post more. [link] [comments] |
Someone had fun writing TI's opamp application report :D
![]() | Source: Single supply opamp design techniques [link] [comments] |
not sure if this counts, but here is a capacitor ball I made
![]() | submitted by /u/le_intrude [link] [comments] |
NUBURU regains compliance with NYSE American Market
MCUs target motor control and power conversion

Infineon’s first PSOC Control MCUs, based on Arm Cortex-M33 processor, enable secured motor control and power conversion. Supported by Modus Toolbox design tools and software, the entry and mainline devices offer varied performance, features, and memory options.
PSOC Control MCUs—C3M for motor control and C3P for power conversion—can be used in appliances, industrial drives, robots, light EVs, solar systems, and HVAC equipment. Their Cortex-M33 processor runs at up to 180 MHz with a DSP and FPU, while a CORDIC math coprocessor accelerates control loop calculations.
Entry-line MCUs (C3M2, C3P2) feature high-resolution, high-precision ADCs and timers, while mainline MCUs (C3M5, C3P5) add high-resolution PWMs for faster real-time response. The devices are PSA Certified Level 2/EPC2 and include Class B and SIL 2 safety libraries. A crypto accelerator, Arm TrustZone, and secure key storage enable IP protection and firmware updates.
The PSOC Control C3 entry and main lineup comprises 34 devices, all available now.
Find more datasheets on products like this one at Datasheets.com, searchable by category, part #, description, manufacturer, and more.
The post MCUs target motor control and power conversion appeared first on EDN.
Keysight elevates chiplet design environment

Chiplet PHY Designer 2025 from Keysight offers simulation capabilities for UCIe 2.0 and support for the Open Compute Project Bunch of Wires (BoW) standard. Tailored to AI and data center applications, this digital chiplet design and die-to-die (D2D) platform enables pre-silicon level validation, streamlining the path to tapeout.
The Chiplet PHY Designer aids chiplet development by ensuring interoperability with UCIe 2.0 and BoW standards, enabling seamless integration within advanced packaging ecosystems. It accelerates time-to-market by automating simulation and compliance testing setup, including Voltage Transfer Function (VTF) analysis, simplifying design workflows.
Enhancing design accuracy, the toolset provides insight into signal integrity, bit error rate (BER), and crosstalk analysis, minimizing the risk of costly silicon re-spins. It also optimizes clocking designs by supporting advanced schemes like quarter-rate data rate (QDR), ensuring precise synchronization for high-speed interconnects.
To read about what’s new in Chiplet PHY Designer 2025, click here.
Chiplet PHY Designer product page
Find more datasheets on products like this one at Datasheets.com, searchable by category, part #, description, manufacturer, and more.
The post Keysight elevates chiplet design environment appeared first on EDN.
GaN die power custom MMICs

Guerrilla RF’s GRF0020D and GRF0030D GaN-on-SiC HEMT power amplifiers deliver up to 50 W of saturated power. Available as bare die, these discrete transistors are intended for wireless infrastructure, military, aerospace, and industrial heating applications, supporting integration into custom MMICs.
Each device operates from either 50-V or 28-V supply rails, covering multiple octaves of operational bandwidth for continuous wave, linear, and pulsed modulation. When using a 50-V rail, the GRF0030D delivers 50 W (PSAT) from DC to 6 GHz, with gain ranging from 13.5 dB to 23.7 dB. At 28 V, it provides up to 27.5 W of saturated output power.
The GRF0020D offers up to 30 W at 50 V and 19 W at 28 V. This lower-power HEMT supports frequencies up to 7 GHz and provides gain between 13.8 dB and 24.3 dB.
The GRF0020D and GRF0030D are 100% DC production tested to ensure known good die (KGD) compliance. They are available for order, with samples ready for distribution. Prices start at $30 each for quantities of 100 units.
Find more datasheets on products like this one at Datasheets.com, searchable by category, part #, description, manufacturer, and more.
The post GaN die power custom MMICs appeared first on EDN.
Scope option enables wideband modulated load pull

R&S offers a load pull test setup with wideband modulated signals using the RTP oscilloscope for non-linear device characterization. Compared to conventional vector network analyzers, this setup enables wideband modulation characterization of RF frontends across varying impedances. It allows precise validation of key performance indicators, such as error vector magnitude and adjacent channel leakage ratio, to support the development of RF components for next-generation wireless technologies.
Designed to verify power amplifier performance when connected to an antenna with dispersive impedance, the setup is based on the RTP084 oscilloscope with the wideband modulated load-pull option RTP-K98, paired with the SMW200A vector signal generator. The oscilloscope’s internal architecture ensures precise phase and time synchronization for forward and reverse wave measurements. Meanwhile, the dual-path vector signal generator provides accurate timing and phase stability between the input and tuning signal for load pull operation.
The RTP-K98 software processes the oscilloscope’s measured data, performs the necessary calculations to achieve the target impedance, and controls the signal generator. It is well-suited for verifying the performance of RF frontends, typically used across wider frequency ranges and multiple transmission bands, such as 5G or Wi-Fi.
Option RTP-K98 is available now. For more information on load pull testing, click here.
Find more datasheets on products like this one at Datasheets.com, searchable by category, part #, description, manufacturer, and more.
The post Scope option enables wideband modulated load pull appeared first on EDN.
TCXO enhances synchronization for 800G networks

The SiT5977 Super-TCXO from SiTime is a single-chip timing device that achieves 3X better synchronization than its predecessor and enables 800G network connectivity. Part of the Elite RF family, this differential-ended TCXO optimizes AI compute efficiency in large data centers.
With a dedicated low-phase-noise MEMS resonator driving its integrated PLL, the SiT5977 simplifies AI system architectures by replacing multiple timing components. This ultra-stable, low-jitter TCXO provides a 156.25-MHz output with 80-fs phase jitter and LVDS outputs, supporting 800G and higher links. Integrated digital control adds system-level programmability.
The SiT5977 offers ±0.1 to ±0.25 ppm frequency stability, ensuring precise timing for high-speed networks and AI systems. Designed for demanding environments, it features a ±1-ppb/°C frequency slope (dF/dT) for resilience against airflow and thermal shock. Its digitally controlled tuning allows fine frequency adjustments with a ±400-ppm pull range and 0.05-ppt (5e-14) resolution via an I2C/SPI interface, facilitating embedded control loops for real-time compensation.
Housed in a compact 5.0×3.5-mm package, the SiT5977 Super-TCXO is now in production, with samples available.
Find more datasheets on products like this one at Datasheets.com, searchable by category, part #, description, manufacturer, and more.
The post TCXO enhances synchronization for 800G networks appeared first on EDN.
my 1st double side pcb! based on the esp32c3wroom2
![]() | [link] [comments] |
Calories, power dissipation, and environmental chambers

I was having a bottle of iced tea one day when I noticed something. Please see this excerpt from the bottle’s label referring to a 2,000 calories per day of personal intake (Figure 1).
I confirmed that caloric number independently to learn that it’s considered an average, but still an essentially correct daily caloric intake number.
Figure 1 Bottle label excerpt referring to a 2000 calories per day standard diet.
If we look up the word “calorie”, we find that one calorie equals 4.184 Joules (Figure 2).
Figure 2 A quick word search reveals that a single calory is the equivalent of 4.184 Joules.
If then we consume 2000 calories per day, we find the following in Figure 3.
Figure 3 The human body power usage based upon the 2,000 calories per day reference for a standard diet.
Two thousand calories per day equals 8368 joules per day which then comes to 0.096852 joules per second which is just under 97 mW. We’ll call that 100 mW just for convenience of thought. We are dealing with approximations, of course.
If all of one’s caloric intake is ultimately dispersed as body heat, that 100 mW of body heat could plausibly be imparted to whatever delicate unit under test (UUT) one happens to be working on while working diligently inside an environmental test chamber.
I once saw such an environmental test chamber in which there was a bank of 100-W lamps mounted “over there”. Those lamps were kept constantly lit and running except that if one more person were to enter the room, one lamp would then be extinguished. This was supposed to help hold the thermal environment of the UUT as invariant as possible.
If we say the following:
- That each light bulb was providing 100 W over a spherical area of 4*π*R² where R is the radial distance from the light bulb
- That the UUT has 1 square foot (1 ft2)of presented area receiving that bulb’s thermal radiation
- That the bulk of the 100 mW of a human body was also impinging on that UUT
We can then seek that value of R for which the 100 W of one bulb was down by a factor of 1000 to yield the equivalent human presentation of 100 mW to that UUT.
Noting that 100 W divided by 100 mW equals 1,000, we seek that value of R at which the area of the posited sphere around the bulb comes to 1,000 ft2.
Where 4*π*R² = 1,000, we find that R is nominally 8.92 ft.
For all of these crude approximations, y’know what?? That is indeed just about how far away those light bulbs were positioned with respect to the UUT at hand in that chamber.
John Dunn is an electronics consultant, and a graduate of The Polytechnic Institute of Brooklyn (BSEE) and of New York University (MSEE).
Related Content
- Measure of holiday calories – the thermodynamic diet
- Adventures with a remote heart monitor
- Avoiding blood pressure measurement errors – Part 3
- Heart rate monitor using a programmable SoC
The post Calories, power dissipation, and environmental chambers appeared first on EDN.
Robot System Products (RSP) Opens Manufacturing Facility in Chennai, India
Robot System Products (RSP), a global leader in high-performance industrial robot accessories, has officially opened its first production facility outside of Sweden, located in Chennai, India, through its subsidiary company, Scandinavian Robot Systems India Private Limited.
RSP’s Indian subsidiary began operations in November 2023 in Tamil Nadu, one of India’s primary automotive hubs. Since then, the company has been supplying its industry-leading range of robot accessories to customers across India. In 2024, RSP experienced significant growth, especially within the automotive and automotive ancillary (Tier-1) sectors in India. To further enhance customer service, the company also established a branch office in Pune, strengthening its presence in western India.
The new facility in Chennai will focus on manufacturing key products or modules such as automatic tool changers, swivels, tool parking stands, and cable & hose management solutions. RSP is leveraging the established supplier network in Tamil Nadu and Karnataka to ensure high-quality production.
According to the International Federation of Robotics (IFR), India was the fastest-growing industrial robot market in 2023, with annual installations increasing by 50%, reaching 8,500 units. This surge in demand has positioned India as the 10th largest robotics market globally. “We are confident in our decision to establish operations in India, and the rapid market growth reinforces that India will deliver on its potential,” said Eddie Eriksson, President and CEO of Robot System Products AB.
RSP’s products are designed to enhance manufacturing flexibility and reliability across all major robot brands. As a leading innovator in the industrial automation space, RSP delivers cutting-edge solutions that improve robot performance and versatility. Among its key products, the automatic tool changers stand out for their efficiency, enabling robots to seamlessly switch between various tools—such as grippers, welders, and drills—without downtime, optimizing productivity and throughput.
Arvind Vasu, Managing Director of RSP’s India subsidiary, commented, “Indian industries are poised to boost productivity through robot-based automation, particularly in automotive electric vehicles, electronics, and other manufacturing sectors. With India’s ambitious ‘Make in India’ initiative, RSP is well-positioned to offer local industries reliable, high-quality, and flexible solutions to help them automate and achieve their goals.”
The post Robot System Products (RSP) Opens Manufacturing Facility in Chennai, India appeared first on ELE Times.
Pages
