Українською
  In English
Feed aggregator
Top 10 UAV Manufacturers in India
India’s unmanned aerial vehicle (UAV) industry is soaring to new heights, fueled by rapid technological advancements, policy support, and increasing demand across diverse sectors. From bolstering national security to revolutionizing precision agriculture and infrastructure monitoring, drones are becoming indispensable assets. As the Indian government pushes for self-reliance under the “Make in India” initiative, domestic UAV manufacturers are stepping up with cutting-edge innovations and indigenous designs. In this evolving landscape, several companies are leading the charge, redefining aerial intelligence and automation. Here’s a look at the top 10 UAV manufacturers shaping India’s drone ecosystem in 2025.
- ideaForge Technology Limited
Established in 2007, ideaForge is a Mumbai-based UAV manufacturer renowned for designing and developing drones tailored for mapping, security, and surveillance applications. Serving defense forces and various government departments, ideaForge holds a significant position in the Indian drone industry. In July 2023, the company marked a milestone by launching its initial public offering (IPO), underscoring its growth trajectory. At Aero India 2025, ideaForge unveiled four new UAVs: NETRA 5, SWITCH V2, a Tactical UAV concept, and a Logistics UAV concept, each designed to address operational challenges in high-stakes environments.
- Asteria Aerospace
Asteria Aerospace is a prominent player in the Indian drone industry, focusing on the development of UAVs for diverse applications across defense and industrial sectors. The company offers a range of drone solutions tailored to meet specific operational requirements, emphasizing innovation and reliability in its products.
- Zen Technologies
Specializing in defense training solutions, Zen Technologies has expanded its portfolio to include UAVs and related systems for military applications. Leveraging its expertise in simulation and training, the company provides comprehensive drone solutions that enhance defense capabilities and operational readiness.
- Paras Defence and Space Technologies
Paras Defence is engaged in the design, development, and manufacturing of a wide array of defense and space engineering products, including UAVs. Catering to various segments of the Indian defense industry, the company contributes to the nation’s strategic capabilities by delivering advanced drone technologies and solutions.
- Garuda Aerospace
Based in Chennai, Garuda Aerospace offers drone-based solutions across multiple sectors, including agriculture, infrastructure, and surveillance. The company’s focus on delivering cost-effective and efficient UAV services has positioned it as a key player in the Indian drone ecosystem, addressing diverse industry needs with innovative approaches.
- Aarav Unmanned Systems
Aarav Unmanned Systems specializes in providing drone solutions for industrial applications such as mining, urban planning, and agriculture. Their UAVs are engineered to deliver high-quality data, facilitating informed decision-making processes and enhancing operational efficiency across various sectors.
- NewSpace Research & Technologies
Headquartered in Bengaluru, NewSpace Research & Technologies focuses on developing persistent drones for earth observation and communications. Collaborating with Hindustan Aeronautics Limited (HAL), the company is instrumental in projects like the Combat Air Teaming System (CATS) Infinity, a high-altitude pseudo-satellite UAV designed for extended endurance and strategic operations.
- Throttle Aerospace Systems Pvt Ltd
Throttle Aerospace Systems (TAS), based in Bengaluru, is a leading entity in the Indian drone manufacturing sector. As the first Directorate General of Civil Aviation (DGCA)-approved maker of civil drones and licensed to produce military drones, TAS offers a range of innovative products and solutions aimed at transforming mobility across various industries.
- Drones Origin Private Limited
Located in Hyderabad, Drones Origin Private Limited specializes in the indigenous design and manufacturing of drone and UAV components. Positioning itself as a one-stop solution for various drone-related needs, including propulsion and custom designs, the company emphasizes self-reliance and aligns with the ‘Make in India’ initiative, contributing to the nation’s growing drone manufacturing industry.
- IG Drones
IG Drones is recognized as one of the top ‘Made-in-India’ drone manufacturers, contributing significantly to the country’s UAV landscape. The company focuses on delivering innovative drone solutions that cater to various industry requirements, enhancing operational efficiency and productivity.
The rapid expansion of India’s UAV industry is a testament to the technological advancements and entrepreneurial spirit driving the sector. These top 10 manufacturers exemplify the country’s commitment to innovation, self-reliance, and the strategic integration of drone technology across multiple domains.
The post Top 10 UAV Manufacturers in India appeared first on ELE Times.
Braun 6550/5704 PCB dismantled
![]() | submitted by /u/Loud_Construction998 [link] [comments] |
NORD DRIVESYSTEMS SUSTAINABILITY STRATEGY FOR 2025
At NORD DRIVESYSTEMS, our sustainability strategy for 2025 focuses on acting in an environmentally conscious, responsible and integer manner. A cross-divisional team as well as the management and owners are part of the implementation. Besides NORD’s products, it includes four further fields of action.
“Our sustainability strategy for 2025 is a promise to our customers, to the public and to ourselves to consequently act in an ecological, economic and socially responsible manner”, emphasizes Carolin von Rönne from the area of Process and Organisational Development & Corporate Sustainability Management at NORD DRIVESYSTEMS. The strategy comprises five key aspects:
ProductsWhen it comes to sustainability, our products at NORD are also our top priority. This is because the design, life cycle and application areas have an impact on the environment. The concept of sustainability is therefore already rooted in the product development process. “Drives can be found in many areas of industry, where they consume a large proportion of the energy used,” explains Carolin von Rönne. “With efficient drive solutions such as the IE5+ synchronous motor, we want to make a significant contribution to reducing CO₂ emissions.“ The NORD ECO service furthermore supports companies in finding the most efficient drive solutions for them.
Governance & processesThe sustainability management was introduced at NORD in 2022. Since then, the company has achieved important milestones such as an annual sustainability report according to GRI, environmental certifications and the integration of international structures. The central objective in this field of action is the establishment of an international governance structure and CSRD-compliant reporting for the entire NORD DRIVESYSTEMS Group with 48 subsidiaries in 36 countries because the success of other factors – in
EnvironmentIn order to coordinate structured measures and document them in a legally secure manner, international environmental management is essential for NORD. This is implemented in accordance with ISO14001 for the largest subsidiaries. In addition, the climate balance for Scope 1–3 is determined group-wide. NORD DRIVESYSTEMS Group further aims to reduce its energy consumption and amount of waste as well as increase the share of self-produced electric power and the use of renewable energies. Existing biodiversity areas are to be further expanded.
PeopleIn times of skills shortage, NORD continues to increase its attractiveness as an employer. The company is currently rolling out a global digital learning management system to offer all employees the opportunity for further individual development. Further targeted campaigns and measures are intended to promote diversity among the workforce. “Inclusion, respect for human rights, strengthening our work culture, safety and continuous transfer of knowledge are only some of the topics we would like to promote”, says Carolin von Rönne.
Supply chainNORD wants to reassure its customers and employees that sustainable production is given high priority both at manufacturing facilities and in the upstream supply chain. Risk analyses and other processes are carried out within the framework of the Germany Act on Corporate Due Diligence Obligations in Supply Chains (LKSG).
The post NORD DRIVESYSTEMS SUSTAINABILITY STRATEGY FOR 2025 appeared first on ELE Times.
Vintage and not so vintage electronics, the photos are just the tip of the iceberg. My father passed away last year ,he was a lab technician customs officer and a communications/electronics enthusiast that knew more about electronics than I could ever...
![]() | submitted by /u/Advanced_Director358 [link] [comments] |
DRAM basics and its quest for thermal stability by optimizing peripheral transistors

For decades, compute architectures have relied on dynamic random-access memory (DRAM) as their main memory, providing temporary storage from which processing units retrieve data and program code. The high-speed operation, large integration density, cost-effectiveness, and excellent reliability have contributed to the widespread adoption of DRAM technology in many electronic devices.
DRAM bit cell—the element that stores one bit of information—has a very basic structure. It consists of one capacitor (1C) and one transistor (1T) integrated close to the capacitor. While the capacitor’s role is to store a charge, the transistor is used to access the capacitor, either to read how much charge is stored or to store a new charge.
The 1T-1C bit cells are arranged in arrays containing word and bit lines, and the word line is connected to the transistors’ gate, which controls access to the capacitor. The memory state can be read by sensing the stored charge on the capacitor via the bit line.
Over the years, the memory community introduced subsequent generations of DRAM technology, enabled by continuous bit-cell density scaling. Current DRAM chips belong to the ’10-nm class’ (denoted as D1x, D1y, D1z, D1a…), where the half pitches of the active area in the memory cell array range from 19 nm down to 10 nm. However, the AI-driven demand for better performing and larger capacity DRAM is propelling R&D into beyond 10-nm generations.
This requires innovations in capacitors, access transistors, and bit cell architectures. Examples of such innovations are high-aspect ratio pillar capacitors, the move from saddle-shaped (FinFET-based) access transistors to vertical-gate architectures, and the transition from 6F2 to 4F2 cell designs—F being the minimum feature size for a given technology node.
A closer look inside a planar 1T-1C DRAM chip: The peripheral circuit
To enable full functionality of the DRAM chip, several other transistors are needed besides the access transistors. These additional transistors play a role in, for example, the address decoder, sense amplifier, or output buffer function. They are called DRAM peripheral transistors and are traditionally fabricated next to the DRAM memory array area.
Figure 1 The 1T-1C-based DRAM memory array and DRAM peripheral area are shown inside a DRAM chip. Source: imec
DRAM peripheral transistors can be grouped into three main categories. The first category is regular logic transistors: digital switches that are repeatedly turned on and off. The second category is sense amplifiers—analog types of transistors that sense the difference in charge between two-bit cells. A small positive change is amplified into a high voltage (representing a logic 1) and a small negative change into zero voltage (representing a logical 0).
These logical values are then stored in a structure of latches called the row buffer. The sense amplifiers typically reside close to the memory array, consuming a significant area of the DRAM chip. The third category is row decoders: transistors that pass a relatively high bias (typically around 3 V) to the memory element to support the write operation.
To keep pace with the node-to-node improvement of the memory array, the DRAM periphery evolves accordingly in terms of area reduction and performance enhancement. In the longer term, more disruptive solutions may be envisioned that break the traditional ‘2D’ DRAM chip architecture. One option is to fabricate the DRAM periphery on a separate wafer, and bond it to the wafer that contains the memory array, following an approach introduced in 3D NAND.
Toward a single and thermally stable platform optimized for peripheral transistors
The three groups of peripheral transistors come with their own requirements. The regular logic transistors must have good short channel control, high on current (Ion), and low off current (Ioff). With these characteristics, they closely resemble the logic transistors that are part of typical systems-on-chips (SoCs). They also need to enable multiple threshold voltages (Vth) to satisfy different design requirements.
The other two categories have more dissimilar characteristics and do not exist in typical logic SoCs. The analog sense amplifier requires good amplification, benefitting from a low threshold voltage (Vth). In addition, since signals are amplified, the mismatch between two neighboring sense amplifiers must be as low as possible. The ideal sense amplifier, therefore, is a very repeatable transistor with good analog functionality.
Finally, the row decoder is a digital transistor that needs an exceptionally thick gate oxide—compared to an advanced logic node—to sustain the higher bias. This makes the transistor inherently more reliable at the expense of being slower in operation.
Figure 2 Here are the main steps needed to fabricate a transistor for DRAM peripheral applications; the critical modules requiring specific developments are underlined. Source: PSS
In addition to these specific requirements, there are a number of constraints that apply to all peripheral transistors. One critical issue is the thermal stability. In current DRAM process flows with DRAM memory arrays sitting next to the periphery, peripheral transistors are fabricated before DRAM memory elements. The periphery is thus subjected to several thermal treatments imposed by the fabrication of the storage capacitor, access transistor, and memory back-end-of-line.
Peripheral transistors must, therefore, be able to withstand ‘DRAM memory anneal’ temperatures as high as 550-600°C for several hours. Next, the cost-effectiveness of DRAM chips must be preserved, driving the integration choices toward simpler process solutions than what logic flows are generally using.
To keep costs down, the memory industry also favors a single technology platform for various peripheral transistors—despite their individual needs. Additionally, there is a more aggressive requirement for low leakage and low power consumption, which benefits multiple DRAM use cases, especially mobile ones.
The combination of all these specifications makes a direct copy of the standard logic process flow impossible. It requires optimization of specific modules, including the transistors’ gate stack, source/drain junctions, and source/drain metal contacts.
Editor’s Note: This is first part of the article series about the latest advancements in DRAM designs. This part focuses on DRAM basics, peripheral circuits, and the journey toward a single, cost-effective, and thermally stable technology platform optimized for peripheral transistors. The second part will provide a detailed account of DRAM periphery advancements.
Alessio Spessot, technical account director, has been involved in developing advanced CMOS, DRAM, NAND, emerging memory array, and periphery during his stints at Micron, Numonyx, and STMicroelectronics.
Naoto Horiguchi, director of CMOS device technology at imec, has worked at Fujitsu and the University of California Santa Barbara while being involved in advanced CMOS device R&D.
Related Content
- DRAM gets more exotic
- FCRAM 101: Understanding the Basics
- DRAM: the field for material and process innovation
- Winbond’s innovative DRAM design and the legacy of Qimonda
- DRAM technology for SOC designers and—maybe—their customers
The post DRAM basics and its quest for thermal stability by optimizing peripheral transistors appeared first on EDN.
Візит делегації компанії NZIA Connect Inc.
До нашого університету завітала делегація компанії NZIA Connect Inc. — потужного південнокорейського стартапу в галузі телекомунікаційних технологій, в яких за плечима передові розробки цифрової валюти та технології для охорони кордонів.
DIY custom Tektronix 576 & 577 curve tracer adapters

Older folks may recall the famous Tektronix 576 and 577 curve tracers from half a century ago. A few of these have survived the decades and ended up in some lucky engineer’s home/work lab.
Wow the engineering world with your unique design: Design Ideas Submission Guide
We were able to acquire a Tek 577 curve tracer with a Tek 177 standard test fixture from a local surplus house that had been used at Sandia Labs, but it was not functional. Even being non-functional, these old relics still command a high price, which set us back $500!! With the help of an on-line service manual and some detailed troubleshooting, the old 577 was revived by replacing all the power supply’s electrolytic capacitors and a few op-amps, plus removing the modifications Sandia had installed.
Once operational we went looking for the various Tek device under test (DUT) adapters for the Tek 177 standard test fixture, these adapters are indeed rare and likewise expensive which sent us on the DIY journey!
The DIY journeyObserving a similar path to Jay_Diddy_B1 [1], we set out to develop a DIY adapter to replace the rare and expensive Tek versions. Like the popular T7 multi-function component tester, which employs a small ZIF socket for leaded-component attachment that works very well; we decided to do the same for the custom Tek adapter using the right and left sides of the ZIF socket to facilitate DUT comparisons with the Tek 177 standard test fixture. This can be seen in Figure 1.
Figure 1 Custom ZIF-based Tek 577 adapter where the right and left sides of the ZIF socket facilitate DUT comparisons with the Tek 177 standard test fixture.
As shown in Figure 2, a low-cost PCB was developed with SMD ferrites added to the nominal “Collector” and “Base” 577 terminals to help suppress any parasitic DUT oscillations. Connectors were also added to allow for external cables if desired (something we have never used). The general idea was to use the 6 banana jacks as support for holding the PCB in place with the ZIF on top of the PCB where one can directly attach various DUTs.
This approach has worked well and allows easy attachment of various leaded-components including the T0-126 and T0-220 power devices.
Figure 2 The custom adapter installed on the Tek 177 standard test fixture.
Applying the curve tracer to an SMD DUTHowever, this still leaves the SMD types in need of a simple means to apply with the Tek 577 curve tracer with the 177 fixture; we set out to investigate this.
After studying the methods Tektronix utilized, we discovered some low-cost toggle clamps (found on AliExpress and elsewhere) which are used for clamping planar objects to a surface for machining. Figure 3 shows the custom toggle clamps used on a custom SMD DUT along with the custom adapter installed on the Tek 177 standard text fixture.
Figure 3 Custom toggle-type SMD adapter for the Tek 577 where using the pair of toggle arms allows both the right and left sides of the Tek 177 fixture to be utilized for direct SMD component comparisons.
These clamps could be repurposed to act as a clamp to hold a SMD DUT in place, which resulted in a custom PCB being developed to mount directly on top of the ZIF-based PCB previously discussed (Figure 4).
Figure 4 The custom SMD PCB that can be used with toggle clamps. This can be installed on the Tek 177 fixture for the Tek 577.
The toggle arms allow slight pressure to be applied to the SMD DUT where the leads make contact with the PCB’s exposed surfaces. Using a pair of toggle arms allows both the right and left sides of the Tek 177 fixture to be utilized for direct SMD component comparisons.
A connector on the rear of the PCB is mounted on the bottom side and mates with another connector on the ZIF type PCB, which allows connection to the 6 banana jacks that plug into the Tek 177 Fixture. Four nylon standoffs provide mechanical support and hold the two PCBs together. This setup allows easy SMD component installation and removal with little effort. Figure 5 shows both adapters for the Tek 577 with 177 standard test fixture.
Figure 5 Both adapters for the Tek 577 with 177 standard test fixture.
Both the ZIF and the SMD Adapters have served well and allow most components to be easily evaluated with the old Tektronix 576 and 577 curve tracers. Figure 6 shows the custom toggle-type SMD adapter in action with pair of DUTs.
Figure 6 Custom toggle-type SMD adapter in operation with pair of DUTs.
A word of cautionJust a word of caution when using these and any adapters, fixtures, or leads with the Tek 576 and 577 curve tracers: these instruments can produce lethal voltages across the exposed terminals. The Tek 177 standard test fixtures were originally supplied with plastic protective covers and sensor switches which removed the DUT stimulus when the plastic cover was open. In the old Tek service manuals, there was a modification method to defeat the Tek 177 sensor switch which many engineers employed, and many also removed the plastic protective covers.
Anyway, I hope some folks lucky enough to have an old Tek 576 or 577 curve tracer with Tek 177 standard test fixture find these custom DIY adapters useful if they don’t already have the old Tek OEM elusive adapters!
Michael A Wyatt is a life member with IEEE and has continued to enjoy electronics ever since his childhood. Mike has a long career spanning Honeywell, Northrop Grumman, Insyte/ITT/Ex-elis/Harris, ViaSat and retiring (semi) with Wyatt Labs. During his career he accumulated 32 US Patents and in the past published a few EDN Articles including Best Idea of the Year in 1989. All posts by Mike Wyatt below:
References
- “EEVblog Electronics Community Forum.” SMD Test Fixture for the Tektronix 576 Curve Tracer – Page 1, www.eevblog.com/forum/projects/smd-test-fixture-for-the-tektronix-576-curve-tracer/.
Related Content
- Tracing a transistor’s curves
- Throw it a curve (tracer)
- Trace voltage-current curves on your PC
- Using oscilloscope X-Y displays
The post DIY custom Tektronix 576 & 577 curve tracer adapters appeared first on EDN.
Top 10 Anti Drone Manufacturers in India
In recent years, the proliferation of unmanned aerial vehicles (UAVs) has necessitated the development of robust counter-drone technologies to address security concerns. India, recognizing this imperative, has seen a surge in companies specializing in anti-drone systems.
This article highlights ten leading Indian manufacturers at the forefront of this critical sector, detailing their technological innovations and contributions.
- Zen Technologies
Established in 1993, Zen Technologies has been a pioneer in defense training solutions and has expanded into anti-drone technologies. Their comprehensive anti-drone system encompasses detection, tracking, and neutralization capabilities. Utilizing radar, radio frequency (RF) sensors, and electro-optical systems, Zen’s solution can detect and track multiple drones simultaneously. For neutralization, they offer both ‘soft kill’ options, such as RF jamming to disrupt drone communications, and ‘hard kill’ measures, including kinetic systems to physically eliminate threats. Notably, Zen Technologies provides a net-based drone capture mechanism, deploying a dedicated drone equipped with a hanging net to intercept and secure rogue UAVs safely.
- Bharat Electronics Limited (BEL)
A state-owned enterprise, BEL has collaborated with the Defence Research and Development Organisation (DRDO) to produce an advanced anti-drone system. This system is capable of real-time detection, tracking, and neutralization of micro and small UAVs. It integrates radar, RF detectors, and electro-optical sensors to provide comprehensive situational awareness. The neutralization suite includes both ‘soft kill’ options, like jamming the drone’s communication and navigation signals, and ‘hard kill’ solutions, such as laser-based directed energy weapons to destroy the target.
- Alpha Design Technologies
Specializing in electronic warfare systems, Alpha Design Technologies has developed advanced solutions to counter UAV threats. Their anti-drone systems are designed to detect, track, and neutralize unauthorized drones using a combination of radar, RF monitoring, and electro-optical tracking. The neutralization methods include jamming and spoofing techniques to disrupt the drone’s control and navigation systems, effectively mitigating potential threats.
- Adani Defence & Aerospace
A significant player in India’s defense sector, Adani Defence & Aerospace is actively engaged in developing counter-drone technologies. Their approach focuses on creating integrated systems that combine detection and neutralization capabilities. Utilizing radar and RF sensors for detection, their systems can identify and track multiple drone threats. For neutralization, they employ electronic countermeasures to disrupt drone operations, ensuring the protection of critical infrastructure and airspace.
- Indo Wings Private Limited
As one of India’s fastest-growing drone and anti-drone manufacturers, Indo Wings specializes in advanced UAVs and counter-UAV systems. Their anti-drone solutions are equipped with sophisticated detection technologies, including radar and RF sensors, to identify and track unauthorized drones. Neutralization is achieved through electronic jamming and other countermeasures, effectively addressing potential threats in various environments.
- Hindustan Aeronautics Limited (HAL)
A state-owned aerospace and defense company, HAL is developing artificial intelligence-driven advanced drones and counter-drone systems for strategic missions. Their focus includes creating solutions capable of operating in high-altitude areas, addressing security challenges along India’s frontiers. HAL’s anti-drone technologies aim to detect and neutralize UAV threats, enhancing the country’s defense capabilities.
- Paras Aerospace
A subsidiary of Paras Defence and Space Technologies, Paras Aerospace offers a range of UAVs and counter-drone solutions. Their anti-drone systems are designed to detect and neutralize rogue drones using advanced sensor technologies and electronic countermeasures. These systems are suitable for protecting critical infrastructure, public events, and sensitive areas from unauthorized drone activities.
- Kadet Defence Systems
Specializing in defense technologies, Kadet Defence Systems has developed anti-drone solutions focusing on detection and neutralization. Their systems utilize radar and RF sensors to detect unauthorized drones and employ jamming technologies to disrupt their operations. These solutions are designed to protect military installations, government facilities, and other critical assets from potential drone threats.
- Throttle Aerospace Systems
Throttle Aerospace Systems has developed the ‘Defender,’ an innovative anti-drone platform that employs vision-based techniques and artificial intelligence. The Defender is capable of actively tracking and neutralizing rogue drones weighing up to 5 kg. This system enhances security by providing an effective solution to counter unauthorized UAVs in various environments.
- DSE Technologies Pvt. Ltd.
DSE Technologies has secured projects for high-end tactical drone detection and neutralization systems. Their solutions offer both ‘soft-kill’ and ‘hard-kill’ options, emphasizing their expertise in security solutions for Indian forces and national security agencies. These systems are designed to detect, track, and neutralize unauthorized drones, ensuring the protection of critical assets and airspace.
India’s anti-drone industry is rapidly evolving, with these companies leading the charge in developing advanced technologies to counter the growing threat of unauthorized UAVs. Through continuous innovation and collaboration, they are enhancing the nation’s security infrastructure and contributing to global counter-drone capabilities.
The post Top 10 Anti Drone Manufacturers in India appeared first on ELE Times.
Top 10 Drone Startups in USA
The drone industry in the United States has witnessed remarkable growth, driven by startups pioneering advancements across various sectors. From defense and agriculture to public safety and logistics, these companies are redefining the capabilities of unmanned aerial systems (UAS).
This article highlights ten leading U.S.-based drone startups, delving into their innovative technologies and contributions to the industry.
- Anduril Industries
Founded in 2017, Anduril Industries specializes in AI-driven surveillance and reconnaissance solutions for the defense sector. Their flagship product, the Lattice platform, integrates sensor fusion, machine learning, and mesh networking to provide autonomous monitoring and control of defense assets. Additionally, Anduril has developed the Ghost drone, an autonomous single-rotor UAV controllable via web platforms or mobile applications, enhancing situational awareness in complex environments.
- Skydio
Established in 2014, Skydio is renowned for its autonomous drones equipped with advanced AI and computer vision. Their drones, such as the Skydio 2+, utilize six 4K navigation cameras to construct a 3D map of their surroundings, enabling obstacle avoidance and autonomous navigation even in GPS-denied environments. Skydio’s technology serves various applications, including infrastructure inspection, public safety, and cinematic content creation.
- Shield AI
Founded in 2015 by former Navy SEAL Brandon Tseng and his brother Ryan, Shield AI focuses on developing AI-powered drones for military applications. Their V-BAT drone is notable for its vertical takeoff and landing (VTOL) capabilities and autonomous navigation without reliance on GPS or remote control. The V-BAT has demonstrated resilience in electronic warfare environments, successfully identifying and aiding in the neutralization of hostile assets.
- DroneDeploy
Since its inception in 2013, DroneDeploy has become a leading provider of drone software solutions, enabling users to create detailed aerial maps and 3D models. Their platform supports various industries, including agriculture, construction, and mining, by offering tools for real-time data analysis, progress tracking, and resource management. DroneDeploy’s software is compatible with a wide range of drone hardware, providing flexibility for enterprise applications.
- Epirus
Epirus, established in 2018, specializes in directed energy systems designed to counter unmanned aerial threats. Their flagship product, the Leonidas system, employs high-power microwave technology to disable swarms of drones instantaneously. This compact and mobile system offers a scalable solution for defense against evolving aerial threats, providing protection for critical infrastructure and military assets.
- Zipline
Founded in 2014, Zipline has revolutionized logistics through autonomous drone delivery services. Initially focusing on medical supply deliveries in remote regions, Zipline has expanded its operations to include commercial partnerships, such as delivering retail products in urban areas. Their drones are designed for long-range missions, capable of operating in diverse weather conditions to ensure timely deliveries.
- Corvus Robotics
A participant in Y Combinator’s 2018 cohort, Corvus Robotics develops autonomous indoor drones for warehouse inventory management. Their drones navigate complex indoor environments to perform automated inventory scans, reducing the need for manual counts and increasing operational efficiency. Equipped with advanced sensors and AI algorithms, these drones can operate in GPS-denied spaces, providing real-time data to warehouse management systems.
- Rotor Technologies
Established in 2021, Rotor Technologies focuses on converting traditional helicopters into unmanned aerial systems. Their Sprayhawk model, based on the Robinson R44 platform, is designed for agricultural applications, featuring a 120-gallon spray tank and autonomous flight capabilities. This approach leverages existing aircraft designs, retrofitting them with advanced avionics and control systems to perform tasks such as crop spraying and cargo transport autonomously.
- BRINC Drones
Founded in 2018, BRINC Drones develops UAVs tailored for public safety and emergency response. Their drones are designed for both indoor and outdoor operations, featuring two-way communication systems, the ability to breach barriers, and payload delivery capabilities. These features enable first responders to assess situations remotely, communicate with individuals in hazardous environments, and deliver essential supplies during emergencies.
- Unusual Machines
Unusual Machines, based in Florida, specializes in the manufacturing of drone components and systems. In November 2024, the company garnered attention by appointing Donald Trump Jr. to its advisory board, aiming to repatriate drone manufacturing to the United States. This strategic move aligns with broader efforts to reduce dependence on foreign technology and strengthen domestic production capabilities in the drone industry.
These startups exemplify the dynamic and rapidly evolving landscape of the U.S. drone industry. Through innovative technologies and applications, they are expanding the horizons of what unmanned aerial systems can achieve across various sectors.
The post Top 10 Drone Startups in USA appeared first on ELE Times.
У співпраці з НАЕК "Енергоатом"
Ядерна енергетика й атомно-промисловий комплекс завжди були найвагомішими складовими економічної, енергетичної та екологічної безпеки України. Сьогодні ключовим питанням розвитку цієї галузі є підготовка кадрів. Серед трьох ЗВО України, в яких безпосередньо готують фахівців для атомної енергетики, КПІ ім. Ігоря Сікорського є найбільш потужним і стабільним, недарма ж рівень працевлаштування його випускників за фахом перевищує 60%.
SPEAG combines CMX500 OBT with the DASY83D system for automated SAR testing of 5G NR devices
SPEAG and Rohde & Schwarz expand their long-term collaboration with the combination of the CMX500 wideband radio communication tester with the DASY8-3D utilising the enhanced DASY8 Application Programming Interface. This combination allows manufacturers of wireless devices to perform Specific Absorption Rate tests of 5G FR1 devices using the future-proof CMX500 multi-technology, multi-channel one-box signaling tester.
SPEAG, a global leader of dosimetric test systems, has combined the CMX500 OBT from Rohde & Schwarz with its advanced specific absorption rate (SAR) measurement system, DASY83D. The CMX500 OBT emulates a 5G new radio (NR) FR1 base station, fulfilling the requirements for SAR testing of 5G NR devices and providing ease of use for the test engineer. The CMX500 radio communication tester supports cellular technologies such as LTE, 5G NR, as well as non-cellular technologies like Wi-Fi, all in a single instrument. The latest test feature sets, including state-of-the-art wireless technologies like NR-NTN, 5G RedCap, and Wi-Fi 7, provides a long-term, future-proof callbox platform.
The evolution of wireless technology has enabled the creation of an increasing number of wireless products that function close to the human body. These products range from cell phones and smart watches to AR/XR goggles, all of which need to ensure their SAR values meet the essential regulatory requirements imposed by many countries. For instance, the Federal Communications Commission (FCC) in the USA, Innovation, Science and Economic Development (ISED) in Canada, and the European Union have all established stringent SAR regulations and continuously developed safety standards for decades. Several other countries, including China, Vietnam, and India, have gradually adopted similar market access regulation requirements regarding the SAR of radio equipment in recent years. Globally, numerous regulatory test labs and market surveillance test labs are equipped with SPEAG systems for SAR testing.
The successful collaboration between SPEAG and Rohde & Schwarz is testimony to the long-term strategy of both companies for leadership and innovation in test and measurement applications for the wireless industry.
The post SPEAG combines CMX500 OBT with the DASY83D system for automated SAR testing of 5G NR devices appeared first on ELE Times.
Intel: The disintegration of a semiconductor giant?

What’s going on at Intel, the largest beneficiary of the U.S. push to onshore chip manufacturing? While the semiconductor industry was still reeling from a Bloomberg report about TSMC in talks for a controlling stake in Intel Foundry at the Trump administration’s request, The Wall Street Journal threw another stunner about Broadcom considering a bid for Intel’s CPU business.
Figure 1 Despite its financial woes, Intel has the largest and most advanced chip manufacturing operation owned by a U.S. company.
Intel, once a paragon of semiconductor technology excellence, has been on a losing streak for nearly a decade. Pat Gelsinger, the company’s overly ambitious former CEO, made an expensive bid to take Intel into the chip contract manufacturing business, which eventually became a liability for the Santa Clara, California-based semiconductor giant.
Meanwhile, it continued to lose market share in its bread-and-butter CPU business to archrival AMD and largely ceded the artificial intelligence (AI) chips boom to Nvidia. In this backdrop, according to Bloomberg, the previous U.S. administration considered Intel Foundry’s merger with GlobalFoundries (GF), which produces older generation chips and abandoned cutting-edge process nodes years ago.
While that was a non-starter, the present U.S. administration seems to have taken a more pragmatic approach by engaging TSMC to take partial ownership of Intel’s fabs, thus throwing a financial lifeline to money-losing Intel. Moreover, TSMC, in full control of its chip manufacturing operations, is expected to bring stability with its highly successful fabrication process recipes.
However, as the Bloomberg report points out, these talks are in an early stage and it’s not clear what’s in it for TSMC. While Taiwanese super fab expressed its lack of interest in Intel’s foundries a few months ago, its about-face on this matter seems to be linked to the current geopolitical turmoil. More details on this matter are expected to emerge in the coming days.
Broadcom eying Intel’s CPU business
The case for Broadcom potentially acquiring Intel’s CPU and related design businesses is less mysterious. The WSJ story claims that Broadcom is studying the possibility of acquiring Intel’s chip design business. If this matures alongside TSMC’s potential takeover of Intel Foundry, it’ll be the end of the road for the Intel brand as we know it.
However, the report clarifies that, like the TSMC matter, Broadcom’s talks regarding Intel are preliminary and largely informal. Furthermore, Broadcom will only proceed if Intel finds a manufacturing partner; here, it’s important to note that Broadcom and TSMC are working separately.
Figure 2 Despite losing market share to AMD and Nvidia, Intel owns a rich array of semiconductor design resources and patents.
The semiconductor industry rumor mill is in full swing, and we are likely witnessing the fall of an American corporate icon in real-time. This is a stark remainder of the semiconductor industry’s hyper competitive nature, which doesn’t spare missteps of even storied companies like Intel.
Intel’s woes are clearly beyond the reflection phase, and the damage done during Gelsinger’s tenure seems irreparable. However, the U.S. administration also sees Intel as an entity critical to national security. Will that be a blessing in disguise or a catalyst for its quick demise? Time will tell.
Related Content
- EU Chips Act: After Theory, Practice
- Intel Will Rely on TSMC for its Rebound
- Intel: Gelsinger’s foundry gamble enters crunch
- Intel Foundry: Leveraging Process Edge for Profit
- Intel Halts Products, Slows Roadmap in Years-Long Turnaround
The post Intel: The disintegration of a semiconductor giant? appeared first on EDN.
New industrial CoolSiC MOSFETs 650 V G2 in Q-DPAK and TOLL packages offer improved power density
The electronics industry is experiencing a significant shift towards more compact and powerful systems. To support this trend and further drive innovation at the system level, Infineon Technologies AG is expanding its portfolio of discrete CoolSiC MOSFETs 650 V with two new product families housed in Q-DPAK and TOLL packages.
These diverse product families, with top- and bottom-side cooling, are based on the CoolSiC Generation 2 (G2) technology and offer significantly improved performance, reliability, and ease of use. The product families target high- and medium-power switched-mode power supplies (SMPS) including AI servers, renewable energy, chargers for electric vehicles, e-mobility and humanoid robots, televisions, drives and solid-state circuit breakers.
The TOLL package offers outstanding Thermal Cycling on Board (TCoB) capability, enabling compact system designs by reducing the printed circuit board (PCB) footprint. When used in SMPS, it can also reduce system-level manufacturing costs. The TOLL package now fits an extended list of target applications, enabling PCB designers to further reduce costs and better meet market demands.
The introduction of the Q-DPAK package complements the ongoing development of Infineon’s new family of Topside Cooled (TSC) products, which includes CoolMOS 8, CoolSiC, CoolGaN and OptiMOS. The TSC family enables customers to achieve excellent robustness with maximum power density and system efficiency at low cost. It also enables direct heat dissipation of 95 percent, allowing the use of both sides of the PCB for better space management and reduction of parasitic effects.
The post New industrial CoolSiC MOSFETs 650 V G2 in Q-DPAK and TOLL packages offer improved power density appeared first on ELE Times.
Wolfspeed’s revenue falls 7% in December quarter
The hidden car revolution: zonal architecture
By: STMicroelectronics
Zonal platform. Domain architecture. Those are words people almost never hear in the context of the car they will drive in the next decade. When most people think of the future, they imagine an electric vehicle with a high level of driver assistance or autonomous driving capabilities – and all the latest digital media capabilities built in. While we might wonder what such a car would look like and how it would drive, we rarely think about what would need to take place in the unseen parts of the vehicle to make this reality. Yet, it’s exactly what is driving a hidden revolution: the move to zonal architecture and software-defined vehicles.
Let’s take a step back. A few years ago, most industry pundits foresaw the growing popularity of EVs (electric vehicles), and governments set ambitious goals, such as phasing out fossil fuel vehicles in the European Union by 2035. Many of these objectives are still in effect. And while some consumer adoption has slowed, the hype curve forecasts that the industry is about to pick up steam. Certain analysts simply think that consumers are waiting for longer-range, more reliable and extensive charging networks, as well as more affordable options.
Why is everyone talking about architecture? Understanding what’s unseen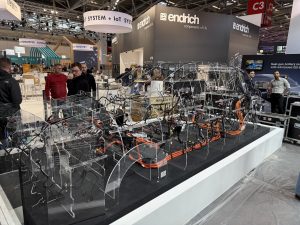
So why is the car of tomorrow not here already? Because building the kind of vehicles consumers are clamoring for requires the industry to rethink how cars are designed. OEMs, Tier 1 suppliers, and others have realized that one of their best solutions was to create new platforms to enable greater efficiency and more quickly introduce technological advancements. For instance, in May 2024, Audi revealed its Premium Platform Electric (PPE). Developed jointly with Porsche, the platform makes its Q6 e-tron series significantly more efficient and capable.
Yet, despite a renewed emphasis on the car architecture, almost no one ever gets to see this “platform.” It’s for this reason that the ST Booth at electronica 2024 in Munich, Germany, will give attendees the unique opportunity to see one of the most hidden aspects of modern vehicles: an electronic/electrical (E/E) architecture. The exhibit shows the wiring harness of an actual car currently on the market, peeling back the curtain to expose the quiet revolution happening in the automotive industry.
What is a car architecture and how has it evolved?
The first electronic system to make its way into mainstream vehicles was the electronic fuel injector (EFI) in the 70s, which replaced the carburetor. It used an Electronic Control Unit (ECU) to inject fuel into the engine, improving performance and reducing air pollution. As more ECUs brought electric windows or seats, for instance, engineers moved to a distributed architecture where one central gateway talked to multiple ECUs around the car. It enabled the prioritization of ECUs, ensuring that safety features, such as steering or braking, took precedence.
Afterward, as advanced driver assistance systems and new functionalities were invented and the industry maxed out the number of ECUs it could on a single platform, the industry moved to the domain architecture. This structure categorizes ECUs into domains, such as advanced driver-assistance systems (ADAS), powertrain, chassis, safety, infotainment, and more. Each domain has a gateway that talks to ECUs that control numerous devices and sensors. Many car makers have adopted this architecture today, for good reasons, optimizing it with each new iteration to make it more efficient. In the same vein, other car makers with the same goal in mind are exploring zonal architectures.
What is a zonal architecture?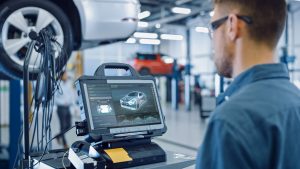
The zonal architecture organizes ECUs by their physical location inside the vehicle. It leverages a new generation of ECUs with powerful processing functions and a central High-Performance Computing Unit (HPCU) that supports fast communication protocols like Ethernet. Consequently, it simplifies platform design by reducing cable lengths and gauges, among other things. A central HPCU can also deal with the amount of data, computational throughput, and power required by high-performance ADAS functions, as well as new applications, such as AI.
This helps car makers move toward software-defined vehicles – an important step in speeding up innovation and allowing smartphone-like upgrades over time, thanks to over-the-air updates. This explains why S&P Global Mobility predicts that nearly 40% of the new cars manufactured in 2034 will feature a zonal architecture.
The Q6 e-tron onboard network exhibit on the ST booth at electronica is a great example of a car maker optimizing its architecture. The domain platform features 1,500 cables totaling over 3,500 meters (about 3,900 yards) and weighing nearly 60 kilograms (130 lb). It also includes over 400 connectors that can interconnect around 100 ECUs. It’s rare to see this harness laid out in public. The exhibit exemplifies the expertise it takes to ensure that all ECUs and connectors serve to optimize the platform rather than weighing it down. It’s a new way of thinking that demands highly specialized know-how and extensive knowledge of the overall product.
The move to a zonal architecture demonstrates this point even more. Conservatively, a vehicle switching to a zonal architecture would see its overall harness weight shrink by around 20%, increasing the battery’s range or gas mileage. A lighter car takes less energy to travel a set distance, thus improving its efficiency and reducing operating costs since consumers can drive more for less. Hence, it is fascinating that while the lighter and simpler harness is entirely hidden from the user, its impact is very visible.
Software is taking the wheel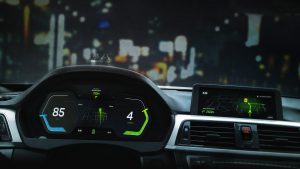
Another way the hidden architecture makes itself known to users is through the many software features consumers want to use and see improved throughout the life of their vehicle. Not many realize how applications govern cars, but they still demand features like 360º camera vision as well as connected and cloud-based systems that provide entertainment, over-the-air updates, and other smartphone-like capabilities. Most drivers don’t know that the harness is directly responsible for enabling a new generation of software-defined vehicles, but they expect predictive maintenance applications for a better experience. And car makers know that instead of a recall, a software update can help save a lot of time, significantly reduce costs, and improve brand appreciation.
Today, software increasingly controls every aspect of the car, thanks in part to the rise of real-time virtualization, which improves the use of hardware resources by ensuring developers can do more with the same components. It’s all about decoupling the code from what it runs on. Thanks to containers and hypervisors, it is possible to run multiple software modules on one hardware ecosystem and still enjoy proper segregation to protect against interference. The technology is already popular in servers and data centers to create secure, safe, and efficient systems. It’s no wonder car makers are bringing it to their new vehicles.
Another advantage of this software paradigm is that it is responsible for the explosion of data generation and the centralization of processing capabilities for improved analysis and decision-making. New architectures have enabled car makers to install hundreds of sensors when they were limited to a few dozen in previous platforms. And more importantly, thanks to the more powerful ECUs and HPCUs, OEMs can future-proof systems and run powerful algorithms but still enjoy a more straightforward development experience. If one software platform can run more applications, it will enable car makers to offer more and richer features while keeping costs down, and ensure consumers get more value out of their vehicles.
Hardware metamorphosisAs we alluded to, the advent of software-defined vehicles and the decoupling of the hardware from the application is only possible if car makers choose microcontrollers and microprocessors that can meet their safety requirements while also offering the computational power and hardware IPs necessary to make this a reality. Engineers must find devices that can support real-time virtualization, numerous I/Os, and a large, embedded, and fast memory that facilitates over-the-air updates. MCUs must be designed and certified for automotive use with specialized safe redundancy built-in, especially as ECUs handle more and more safety applications.
It’s easy to see that this new evolution in car architecture represents a unique electrical challenge, as engineers must create robust, safe, and efficient power distribution mechanisms. It’s the reason why many are adopting smart switches. Unlike the classic melting fuses and mechanical relays, these new electronic switches are faster. As a result, they can offer far greater protection against an adverse electrical event because they respond much quicker than classical components. Their electronic nature also makes them vastly more accurate and flexible. Indeed, they come with monitoring features to enable real-time load management and control. Moreover, they are resettable, which saves from having to replace them manually.
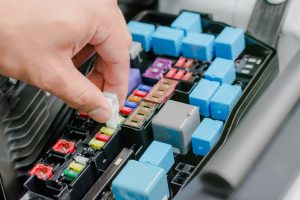
Another critical benefit of smart fuses is their tiny size compared to traditional switches and relays. Because eFuses are so small and electronically controlled, car makers can use shorter harnesses since, among other things, they no longer need to route cables to a large fuse box that must be user accessible. Moreover, the significantly higher accuracy means that the harness can be thinner, thus further contributing to weight reduction. A smaller design with fewer components that are more robust and accurate also helps improve overall reliability. Hence, while some engineers are still evaluating the cost of eFuses, the overall savings over the architecture’s lifetime explain their increasing popularity.
Taking a step back, we see that power distribution is also a much more critical engineering challenge because vehicles are dealing with far greater loads. Most architectures must handle 12 V, but the industry is moving to 48 V. EV chargers must also be able to handle very high voltages and power levels (up to 3,500 kW today). Hence, one of the most popular solutions is to use wide bandgap devices, such as silicon carbide (SiC). The fast switching frequencies of SiC MOSFETs and diodes mean they can handle a lot more power without the energy losses of previous devices, enabling smaller traction inverters, faster charging modules, and more efficient compressors, among other things.
The evolving role of semiconductor companies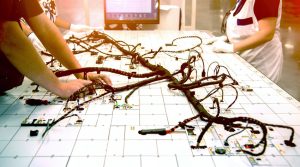
The domain and zonal car architectures emerging today testify to a new reality: everything is connected, and all roads (harnesses, in this case) lead to close cooperation between the key actors of the industry – car makers, Tier 1s, and semiconductor companies. Companies like ST understand how to support platform designers in their quest to decouple the hardware from the software and improve efficiency, safety, and robustness. Together, they create the innovations essential to the future of vehicles that will drive demand for the next generation of cars. It’s for this reason that existing carmakers and new startups are creating ever more intimate partnerships with semiconductor makers and why the market is going through such a disruption.
ST’s ability to grasp new engineering challenges is evidenced through its products. The Stellar family of devices has unique virtualization capabilities to future-proof the software-driven vehicles of tomorrow while its software ecosystem helps reduce development times and meet regulatory requirements. Similarly, STi²Fuse can shrink the overall harness, reduce the bill of materials, and optimize the overall power distribution. Additionally, silicon carbide power devices continue to bring new levels of efficiency. In essence, it’s by offering a wide range of solutions that semiconductor companies can be the close partners that car makers need them to be as they drive the new architectures that will meet the hopes and expectations of their customers.
The post The hidden car revolution: zonal architecture appeared first on ELE Times.
Project “Genial”: Joint electronics roadmap for innovations in the automotive value chain
The automotive industry is facing significant technological challenges in developing new and innovative features and services. When defining their products, vehicle manufacturers must anticipate future technical advancements in microelectronic platforms, sensors, and semiconductor technologies. At the same time, suppliers and semiconductor manufacturers need early insights into the requirements for upcoming features and services to be able to invest in technology development with confidence.
As part of the “GENIAL!” project funded by the Federal Ministry of Education and Research (BMBF), eleven partners collaborated to develop concepts and methods that help companies in the automotive industry work together more effectively and prepare for the future. The project specifically focused on optimizing the collaboration between automotive manufacturers and their component and technology suppliers to accelerate innovation across the automotive value chain.
The prototypical automotive microelectronics roadmap developed in GENIAL! provides a strategic framework for identifying future market needs, use cases, system models, and technical requirements in the field of automotive microelectronics. This roadmap establishes a shared understanding of the microelectronics requirements of future highly innovative vehicles across the entire value chain. The results enable all market participants, as well as research institutions and policymakers, to manage investments and research activities more effectively. In turn, this facilitates the implementation of significantly shorter and more reliable development processes, allowing new, innovative automotive components to be realized more quickly.
The project was based on a model-based system development approach that utilizes the Systems Modeling Language (SysML) as a modeling language, now integrated into SysML v2. This approach is supported by the AGILA database and further enhanced by the IRIS (Interactive Roadmapping of Innovative Systems) tool, both developed within the project. AGILA serves as a centralized database for capturing the essential information and providing documentation, consistency checks, and version control.
The IRIS tool enables collaborative modeling, exploration, planning, and evaluation of solution alternatives. It also supports non-technical information, allowing considerations such as security of supply, and enables visualizations for roadmapping. To encourage widespread adoption, the project participants will release tools such as AGILA and IRIS as open-source solutions, making them accessible for anyone interested in creating and maintaining roadmaps.
The innovation modeling methodology “IMoG” (Innovation Modelling Grid) defines activities, roles, and process models for the collaborative creation of roadmaps. This spans from the initial comparison of models in the problem and solution space to the practical application of the AGILA and IRIS tools. Documentation of the methodology, along with several training videos, is available for free download.
The post Project “Genial”: Joint electronics roadmap for innovations in the automotive value chain appeared first on ELE Times.
I have an x ray tube in my workshop
![]() | submitted by /u/antek_g_animations [link] [comments] |
Violated a few regulations, but it works soo well, why doesnt anyone make sth like this
![]() | submitted by /u/Formal-Fan-3107 [link] [comments] |
Student calls International Space Station with his Magnetometer+Accelerometer-based Satellite Tracker
![]() | submitted by /u/KJ7LNW [link] [comments] |
Відкрита реєстрація на весняний семестр проєкту Dillugis!
Проєкт міжнародної академічної онлайн мобільності DILLUGIS (Digital Labs & Lectures for Ukrainian, German & International Students) продовжено на весняний семестр 2025 року.
Pages
