Українською
  In English
Новини світу мікро- та наноелектроніки
TVS Electronics Expands Its Footprint in the Enterprise AIDC Market with a Comprehensive Portfolio of Mobility, Products & Solutions Across India
- The expansion opens new opportunities for end customers in industries such as manufacturing (automobile/electronics), ports, pharma, retail, e-commerce, q-commerce, logistics and healthcare
- Its AIDC portfolio includes an array of products such as Mobile Computers (HHDs), High-Definition Scanners, Industrial Grade Label Printers, and more
TVS Electronics, a leading player in offering integrated end-to-end electronic solutions, has announced the launch of its Enterprise Automatic Identification and Data Capture (AIDC) with an aim to make it simple and accessible to everyone. Leveraging its comprehensive range of enterprise-grade product solutions, TVS Electronics is set to expand beyond its retail offerings and compete strongly in the enterprise AIDC segment, moving beyond its trusted retail offerings.
This move will help Indian businesses digitize operations with affordable, locally supported technology. TVSE’s strong service network ensures quick maintenance, while its end-to-end solutions—from sales to refurbished equipment auction reducing long-term costs. TVS Electronics focus is to introduce practical, scalable tech that improves accuracy and efficiency in inventory, tracking, and data management. By combining global-grade AIDC tech with India-specific needs, TVS Electronics aims to be a one-stop partner for companies embracing automation. Their approach simplifies digital transformation, making advanced tools accessible to enterprises of all sizes.
India’s track and trace sector is accelerating fast, projected to grow at a strong CAGR of 21.3% by 2030. This surge is powered by the integration of AIDC technology with smart tracking software, delivering real-time visibility and seamless automation across the supply chain. Logistics operations are becoming more agile, manufacturers gain better control and efficiency, e-commerce fulfillment is faster and more accurate, and warehousing is undergoing a high-tech makeover. Together, these innovations are driving a smarter, connected, and more responsive supply chain ecosystem across India.
TVS Electronics’ AIDC portfolio includes a broad range of solutions designed to meet the demanding requirements of enterprise operations, such as:
- Mobile Computers (HHDs):Handheld devices for seamless mobility and real time data capture.
- Rugged Scanners:Industrial grade wired, and Bluetooth enabled wireless scanners that provide reliability in harsh environments.
- High-Definition Scanners:Precision scanners (HD, HHD, XHD, UHD) for electronics industries requiring barcode scanning below 3 mil size.
- Industrial-Grade Label Printers:Label printers designed for durability, offering 203 dpi/300 dpi resolutions.
- Mobile Printers:Compact, Bluetooth-enabled printers designed for mobile workforces.
- Rugged Tablets:Tablets built to withstand tough industrial environments, enabling better data management and communication in the field.
TVS Electronics delivers more than just hardware—it’s building a full-fledged automation ecosystem. By integrating with ERP platforms like SAP and Oracle, and leveraging tools such as SOTI for WMS and MDM, TVSE offers seamless end-to-end solutions that elevate operational efficiency and supply chain visibility. Its approach goes far beyond product delivery, prioritizing strategic alliances with software providers, IoT platform innovators, and system integrators. From consultation to training and ongoing support, the company ensures each solution is tailored, enterprise-ready, and optimized across every layer of the tech stack.
Mr. C. Balaji, Vice President, PSG Business, TVS Electronics, said, “TVS Electronics aims to not only provide superior AIDC devices but to also bring tailored, customizable solutions to enterprises across industries. This launch marks a significant milestone for TVS Electronics as we reposition ourselves as a key player in the enterprise AIDC segment, breaking the stereotype of being a retail-focused brand. By building a robust partner ecosystem, we aim to foster customer trust and drive enterprise growth. Our shift towards value-based selling drives sustainable growth while addressing niche industry needs with tailored solutions. With this move, TVS Electronics solidifies its position as a full-spectrum solutions provider in enterprise technology, leveraging the ‘Make in India’ initiative and digital transformation trends to drive growth and innovation.”
TVS Electronics showcases its competitive advantage through highly customizable Enterprise AIDC solutions that integrate seamlessly with leading ERP (Enterprise Resource Planning) platforms, enabling AI-powered insights and real-time analytics for enhanced operational efficiency. Its advanced Tumakuru facility ensures top-tier quality, reduced lead times, and cost-effective production—fueling innovation and strengthening global competitiveness. With tailored end-to-end offerings like Warehouse Management Systems (WMS) and Real-Time Locating Systems (RTLS), and strategic collaborations with Independent Software Vendors (ISVs) and system integrators, TVSE empowers businesses across sectors with scalable automation and intelligent tracking solutions.
With this, TVS Electronics continues to be a reliable OEM supplier in the enterprise AIDC market, expanding its focus beyond retail to serve large enterprises. Committed to staying ahead of trends like automation and IoT, TVS Electronics will deliver enterprise-grade AIDC solutions to empower businesses.
TVS Electronics strengthens its market position and drives enterprise growth by offering tailored solutions backed by a shift to value-based selling, boosting profitability. The company’s focus on digital transformation reinforces its role as a full-spectrum enterprise technology provider. With one of the largest service networks in India, TVS Electronics delivers industry-best turnaround times and exceptional customer support. Its end-to-end IT lifecycle offerings—from after-sales service to second-hand product auctions—ensure optimal efficiency and cost-effectiveness, making it a reliable one-stop solution for businesses.
The post TVS Electronics Expands Its Footprint in the Enterprise AIDC Market with a Comprehensive Portfolio of Mobility, Products & Solutions Across India appeared first on ELE Times.
Strangeworks Expands Into India and Sri Lanka to Accelerate Quantum and AI Innovation
Strangeworks, the Austin-based quantum computing company known for making advanced compute accessible, is planting deeper roots globally with a major expansion into India and Sri Lanka. The move marks a strategic leap for the company, extending its existing footprint in the U.S., Europe, and Japan to one of the most rapidly advancing regions in quantum and AI technology.
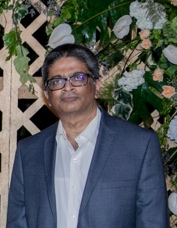
At the heart of this expansion is a simple but bold idea: empower more people (enterprise researchers, engineers, and scientists) to harness the power of quantum and AI without needing a PhD in theoretical physics. Strangeworks’ platform provides access to the largest catalog of quantum, quantum-inspired, and classical compute tools, abstracting away complexity so users can focus on solving real-world problems.
And in India, the timing couldn’t be better.
With its National Quantum Mission (NQM) funneling hundreds of millions into developing indigenous quantum capabilities, India is fast becoming a global hub for next-gen computing. Add to that a vibrant ecosystem of startups, top-tier research institutions, and cross-sector demand from industries like energy, pharma, finance, and logistics, and it’s clear: the region is primed for a quantum leap.
Strangeworks is no stranger to India’s quantum scene. Since 2022, the company has collaborated with BQP, a Quantum-Accelerated Digital Twin software company with Indian origin, to explore real-world applications of quantum-inspired computing—including engineering simulations for high-performance race cars. That partnership not only validated the market—it set the tone for what comes next.
To lead regional growth, Strangeworks has tapped industry veteran Pathy Iyer as Director of India Sales and Marketing. Based in Bengaluru, Pathy brings nearly 30 years of experience from HP, Agilent, and Keysight, where he focused on tech for research and education. He’ll be responsible for forging strategic partnerships, supporting customers, and aligning Strangeworks’ global mission with regional needs.
“India’s bold investments in quantum and AI make it one of the most exciting markets on the planet,” said Steven Gibson, Chief Commercial Officer of Strangeworks. “With Pathy at the helm and strong regional partnerships in place, we’re bolstering our mission to democratize advanced computing globally.”
Pathy is equally enthusiastic. “The potential for quantum and AI to revolutionize industries here is immense,” he said. “Strangeworks has the platform to make that potential real, fast.”
With support from its European teams and centralized marketing operations, Strangeworks aims to offer seamless onboarding and consistent service quality across new regions. But make no mistake—this isn’t just a geographic expansion. It’s a mission move: accelerating access to transformative technologies where the appetite for innovation is sky-high.
The post Strangeworks Expands Into India and Sri Lanka to Accelerate Quantum and AI Innovation appeared first on ELE Times.
PoE+ M12 M.2 Power Delivery PCB
![]() | Does’t get much cooler than this. [link] [comments] |
3D Printing a CubeSat Mockup with an All-Metal Conductive Filament on an Bambu A1 Mini
![]() | submitted by /u/Kupros1 [link] [comments] |
Diodes Inc Reveals Ideal Diode Controllers for New 48 V Automotive Systems
My failed ugly hack job PCB (Class B Audio power amplifier) Don't be dumb like me.
![]() | Ok I'm not a noob but I haven't built anything for a long long time, this PCB circuit was a complete fail haha I didn't expect to have issues with it but it's on me for not thinking properly. Simple OpAmp driving a class B output stage (unbiased, the opamp is fast enough to prevent crossover distortion) I was using TO-3 transistors with 30 volts power supply input. This circuit worked great on a breadboard. I thought I could hack together a PCB and instead of taking time to do proper design I just hack and slashed the PCB "pads" with a dremel bit. Probably not the best idea... The amplifier simply refused to amplify symmetrically - almost all the signal was in the upper NPN transistor, and in fact I could hear the output capacitor vibrating at the 1Khz tone I was feeding into the circuit. See that potentiometer? It was meant to adjust the OpAmp's voltage on the positive input so I could fine tune the symmetry of the amplifier, but it wouldn't affect anything. The upper NPN would get super hot and the PNP wasn't do much at all. Also the circuit was drawing like 250ma without any input signal (whereas when it was on the breadboard it would only draw 5ma, because the OPAMP was keeping the transistors off when there was no signal) At first I thought I possibly had a bad connection somewhere, like wired wrong I looked at this thing for a few hours, all the parts were in the right place. I could not find any weird shorts either. Tested different sections with a multimeter to see. The main thing that would always come back wrong was the voltage on the OPamp + input, it was like in millivolt range, I even replaced the POT and still nothing. I think it was probably oscillating, you can see my thicker output wires? They *twice* cross over the wires that are inputs to the transistor base. Ya, that's probably a really stupid thing to do. Power transistors with a gain of around 70 (beta). Anyway, I don't know how I though this was ever going to work LOL. I guess I should have more patience next time and design a proper layout. Probably use perfboard instead I was using big TO-3 transistors and attaching them to a heatsink . I cut the transistors off of this board . I put them back into my circuit on a breadboard and everything works perfectly again haha. So ya, layout is important DERP. One thing I didn't think to try was lowering the gain of the OpAmp to see if it was oscillating. Right now the gain is at 33 (AC gain) I could have tried dropping that to like 5 to see if it changed anything. Anyway, time to start over and build a proper board that keeps the input lines well away from the higher current output lines. [link] [comments] |
STMicro to buy part of NXP Semiconductors' sensor business for up to $950 million
![]() | submitted by /u/1Davide [link] [comments] |
TIL about ceramic heat sinks. Almost as good as aluminum, inherently isolated.
![]() | submitted by /u/1Davide [link] [comments] |
Most useless bit in your kit?
![]() | This isn't a gender changer. It's a gender conformer. Plug one gender DE-9 into one end, get that same gender on the other. At best, it's a ⅞" extension "cord". And before anyone suggests it can turn a straight-through cable into a cross-over cable, or vice-versa, I've already signal-traced the pins. It's 1:1. So, what's the most useless bit of kit you have? [link] [comments] |
Quad-core MPU adds AI edge to HMI apps

The Renesas 64-bit RZ/G3E microprocessor powers HMI applications with a quad-core Arm Cortex-A55 CPU and Ethos-U55 neural processing unit (NPU) for AI tasks. Running at up to 1.8 GHz, the Cortex-A55 handles both HMI and edge computing functions, while an integrated Cortex-M33 core performs real-time tasks independently of the main CPU to enable low-power operation.
With Full HD graphics and high-speed connectivity, the RZ/G3E is well-suited for industrial and consumer HMI systems, including factory equipment, medical monitors, retail terminals, and building automation. It outputs 1920×1080 video at 60 fps on two independent displays via an LVDS (dual-link) interface. MIPI-DSI and parallel RGB outputs are also available, along with a MIPI-CSI interface for video input and sensing tasks.
The microprocessor’s 1-GHz NPU delivers 512 GOPS for AI workloads such as image classification, object and voice recognition, and anomaly detection—while offloading the CPU. Power management features in the RZ/G3S reduce standby consumption by maintaining sub-CPU operation and peripheral functions at approximately 50 mW, dropping to about 1 mW in deep standby mode.
The RZ/G3E microprocessor is available now. Visit the product page below to check distributor availability.
The post Quad-core MPU adds AI edge to HMI apps appeared first on EDN.
Fuel gauges ensure accurate battery tracking

TI’s single-chip battery fuel gauges, the BQ41Z90 and BQ41Z50, extend battery runtime by up to 30% using a predictive modeling algorithm. Their adaptive Dynamic Z-Track algorithm delivers state-of-charge and state-of-health accuracy within 1%, enabling precise monitoring in battery-powered devices such as laptops and e-bikes.
The fuel gauges provide accurate battery capacity readings under varying load conditions, allowing designers to right-size batteries without overprovisioning. The BQ41Z90 integrates a fuel gauge, monitor, and protector for 3- to 16-cell Li-ion battery packs, while the BQ41Z50 supports 2 to 4 cells. Integration reduces board complexity and can shrink footprint by up to 25% compared to discrete implementations.
Each battery pack manager monitors voltage, current, temperature, available capacity, and other key parameters using integrated analog peripherals and an ultra-low-power 32-bit RISC processor. Both devices report data to the host system over an SMBus v3.2-compatible interface, while the BQ41Z90 also supports I²C. It additionally enables simultaneous current and voltage conversion for real-time power calculations and supports sense resistors as low as 0.25 mΩ.
Pre-production quantities of the BQ41Z90 and production quantities of the BQ41Z50 are available now on TI.com. Evaluation modules, reference designs, and simulation models are also available.
The post Fuel gauges ensure accurate battery tracking appeared first on EDN.
DDR4 memory streamlines rugged system design

Teledyne’s 16-Gbyte DDR4 memory module, designated TDD416Y12NEPBM01, is screened and qualified as an Enhanced Product (EP) for high-reliability aerospace and defense systems. The solder-down device is smaller than a postage stamp, making it well-suited for space-constrained systems where performance is critical.
Rated for -40°C to +105°C operation, the module delivers 3200 MT/s (3200 MHz) and integrates memory, termination, and passives in a compact 22×22- mm, 216-ball BGA package. It replaces multiple discrete components, helping to simplify board layout. An optional companion ECC chip is available for applications requiring error correction.
The TDD416Y12NEPBM01 interfaces with x64 and x72 memory buses and supports a range of processors and FPGAs, including those from Xilinx, Microchip, NXP, and Intel, as well as Teledyne’s LS1046-Space. According to Teledyne, the DDR4 module achieves 42% lower power, 42% less jitter, and 39% PK/PK reduction compared to conventional SODIMMs.
To request further information on the TDD416Y12NEPBM01, click here.
The post DDR4 memory streamlines rugged system design appeared first on EDN.
Accelerator speeds data, cuts latency

With over twice the throughput of its predecessor, MaxLinear’s Panther V storage accelerator achieves 450 Gbps, scalable to 3.2 Tbps. It enables low-latency data processing across file, block, and object storage in HPC, hyperscale, hyperconverged, and AI/ML environments.
Panther V offloads the CPU from compute-intensive data transformation tasks—including compression, deduplication, encryption, and real-time verification. According to MaxLinear, the hardware-based approach offers higher performance, lower storage costs, and improved energy efficiency compared to conventional software-only, FPGA-based, and other competing solutions.
Panther V features a PCIe Gen5 x16 interface to fully leverage the bandwidth of next-generation server platforms. Its MaxHash-based deduplication, combined with deep compression algorithms, achieves data reduction ratios of up to 15:1 for structured data. By reducing CPU and memory bandwidth demands, as well as storage device usage, Panther V helps lower both capital and operating costs. Built-in reliability features ensure high data integrity and six-nines availability.
MaxLinear will unveil Panther V at the upcoming Flash Memory Summit (FMS25).
The post Accelerator speeds data, cuts latency appeared first on EDN.
TIA advances PAM4 optical performance

Designed for 400G and 800G optical networks, Coherent’s CHR1065 100G transimpedance amplifier (TIA) operates at 56 Gbaud using PAM4 modulation. It joins the company’s open-market ASIC portfolio, offering four channels with a 750-µm optical pitch suited for compact DR, FR, and LR module configurations.
The CHR1065 minimizes input-referred noise to 2.3 µA RMS, enhancing receiver sensitivity for longer reach. High linearity up to 2.5 mA ensures reliable performance across varying link budgets. Consuming just 227 mW per channel at 25°C, the TIA supports dense deployments in power-constrained data centers. An I²C interface enables integration with system-level monitoring and control functions.
Tested to JEDEC standards for lifetime reliability, the CHR1065 is now available as a wire-bondable bare die and in full volume production. Engineering samples ship in 25-piece waffle packs. For more information or to request samples, click here.
The post TIA advances PAM4 optical performance appeared first on EDN.
Testing the led with a ps4 battery pack. Gonna get the rest soldered up and tested on my raspi pico so I can light them all up instead of one at a time. Not sure what I’m using this for besides fun. Maybe a temp gauge for something.
![]() | submitted by /u/Grid_Rider [link] [comments] |
PCB houses hate this one simple trick
![]() | Professional bodge wires, with silkscreen and everything. 2oz copper left the chat. [link] [comments] |
Aixtron’s revenue grows 22% in Q2, driven by AI data-center communications
Rohm Unveils Tiny MOSFET Aimed at Fast Charging Applications
Following the trend, here is my first pcb
![]() | This project is a compact evaluation PCB designed for the nPM1100 Power Management IC by Nordic Semiconductor. The board provides the essential circuitry to evaluate the core features of the PMIC in a minimal footprint while exposing all IO pins for external interfacing. PCB dimensions: 22 mm × 16 mm PCB layers: 2 All components: Surface-mounted on the top layer Header pitch: Standard 2.54 mm (0.1") More info on GitHub https://github.com/P-rth/LIPL-Assessment/blob/main/ProblemStatemet2%2Freadme.md [link] [comments] |
My first pcb
![]() | It's not finished yet, but it will be soon. Only one PCB is left once I finish that and do the wiring, it'll be done. [link] [comments] |
Сторінки
