Українською
  In English
Новини світу мікро- та наноелектроніки
New industrial CoolSiC MOSFETs 650 V G2 in Q-DPAK and TOLL packages offer improved power density
The electronics industry is experiencing a significant shift towards more compact and powerful systems. To support this trend and further drive innovation at the system level, Infineon Technologies AG is expanding its portfolio of discrete CoolSiC MOSFETs 650 V with two new product families housed in Q-DPAK and TOLL packages.
These diverse product families, with top- and bottom-side cooling, are based on the CoolSiC Generation 2 (G2) technology and offer significantly improved performance, reliability, and ease of use. The product families target high- and medium-power switched-mode power supplies (SMPS) including AI servers, renewable energy, chargers for electric vehicles, e-mobility and humanoid robots, televisions, drives and solid-state circuit breakers.
The TOLL package offers outstanding Thermal Cycling on Board (TCoB) capability, enabling compact system designs by reducing the printed circuit board (PCB) footprint. When used in SMPS, it can also reduce system-level manufacturing costs. The TOLL package now fits an extended list of target applications, enabling PCB designers to further reduce costs and better meet market demands.
The introduction of the Q-DPAK package complements the ongoing development of Infineon’s new family of Topside Cooled (TSC) products, which includes CoolMOS 8, CoolSiC, CoolGaN and OptiMOS. The TSC family enables customers to achieve excellent robustness with maximum power density and system efficiency at low cost. It also enables direct heat dissipation of 95 percent, allowing the use of both sides of the PCB for better space management and reduction of parasitic effects.
The post New industrial CoolSiC MOSFETs 650 V G2 in Q-DPAK and TOLL packages offer improved power density appeared first on ELE Times.
Wolfspeed’s revenue falls 7% in December quarter
The hidden car revolution: zonal architecture
By: STMicroelectronics
Zonal platform. Domain architecture. Those are words people almost never hear in the context of the car they will drive in the next decade. When most people think of the future, they imagine an electric vehicle with a high level of driver assistance or autonomous driving capabilities – and all the latest digital media capabilities built in. While we might wonder what such a car would look like and how it would drive, we rarely think about what would need to take place in the unseen parts of the vehicle to make this reality. Yet, it’s exactly what is driving a hidden revolution: the move to zonal architecture and software-defined vehicles.
Let’s take a step back. A few years ago, most industry pundits foresaw the growing popularity of EVs (electric vehicles), and governments set ambitious goals, such as phasing out fossil fuel vehicles in the European Union by 2035. Many of these objectives are still in effect. And while some consumer adoption has slowed, the hype curve forecasts that the industry is about to pick up steam. Certain analysts simply think that consumers are waiting for longer-range, more reliable and extensive charging networks, as well as more affordable options.
Why is everyone talking about architecture? Understanding what’s unseen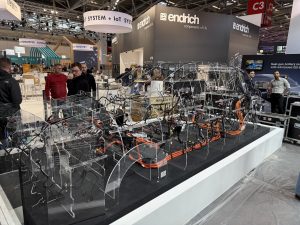
So why is the car of tomorrow not here already? Because building the kind of vehicles consumers are clamoring for requires the industry to rethink how cars are designed. OEMs, Tier 1 suppliers, and others have realized that one of their best solutions was to create new platforms to enable greater efficiency and more quickly introduce technological advancements. For instance, in May 2024, Audi revealed its Premium Platform Electric (PPE). Developed jointly with Porsche, the platform makes its Q6 e-tron series significantly more efficient and capable.
Yet, despite a renewed emphasis on the car architecture, almost no one ever gets to see this “platform.” It’s for this reason that the ST Booth at electronica 2024 in Munich, Germany, will give attendees the unique opportunity to see one of the most hidden aspects of modern vehicles: an electronic/electrical (E/E) architecture. The exhibit shows the wiring harness of an actual car currently on the market, peeling back the curtain to expose the quiet revolution happening in the automotive industry.
What is a car architecture and how has it evolved?
The first electronic system to make its way into mainstream vehicles was the electronic fuel injector (EFI) in the 70s, which replaced the carburetor. It used an Electronic Control Unit (ECU) to inject fuel into the engine, improving performance and reducing air pollution. As more ECUs brought electric windows or seats, for instance, engineers moved to a distributed architecture where one central gateway talked to multiple ECUs around the car. It enabled the prioritization of ECUs, ensuring that safety features, such as steering or braking, took precedence.
Afterward, as advanced driver assistance systems and new functionalities were invented and the industry maxed out the number of ECUs it could on a single platform, the industry moved to the domain architecture. This structure categorizes ECUs into domains, such as advanced driver-assistance systems (ADAS), powertrain, chassis, safety, infotainment, and more. Each domain has a gateway that talks to ECUs that control numerous devices and sensors. Many car makers have adopted this architecture today, for good reasons, optimizing it with each new iteration to make it more efficient. In the same vein, other car makers with the same goal in mind are exploring zonal architectures.
What is a zonal architecture?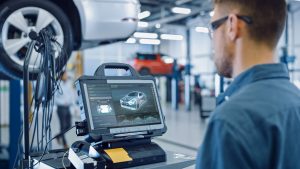
The zonal architecture organizes ECUs by their physical location inside the vehicle. It leverages a new generation of ECUs with powerful processing functions and a central High-Performance Computing Unit (HPCU) that supports fast communication protocols like Ethernet. Consequently, it simplifies platform design by reducing cable lengths and gauges, among other things. A central HPCU can also deal with the amount of data, computational throughput, and power required by high-performance ADAS functions, as well as new applications, such as AI.
This helps car makers move toward software-defined vehicles – an important step in speeding up innovation and allowing smartphone-like upgrades over time, thanks to over-the-air updates. This explains why S&P Global Mobility predicts that nearly 40% of the new cars manufactured in 2034 will feature a zonal architecture.
The Q6 e-tron onboard network exhibit on the ST booth at electronica is a great example of a car maker optimizing its architecture. The domain platform features 1,500 cables totaling over 3,500 meters (about 3,900 yards) and weighing nearly 60 kilograms (130 lb). It also includes over 400 connectors that can interconnect around 100 ECUs. It’s rare to see this harness laid out in public. The exhibit exemplifies the expertise it takes to ensure that all ECUs and connectors serve to optimize the platform rather than weighing it down. It’s a new way of thinking that demands highly specialized know-how and extensive knowledge of the overall product.
The move to a zonal architecture demonstrates this point even more. Conservatively, a vehicle switching to a zonal architecture would see its overall harness weight shrink by around 20%, increasing the battery’s range or gas mileage. A lighter car takes less energy to travel a set distance, thus improving its efficiency and reducing operating costs since consumers can drive more for less. Hence, it is fascinating that while the lighter and simpler harness is entirely hidden from the user, its impact is very visible.
Software is taking the wheel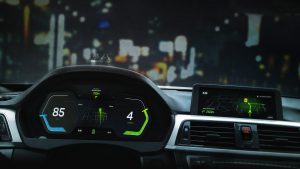
Another way the hidden architecture makes itself known to users is through the many software features consumers want to use and see improved throughout the life of their vehicle. Not many realize how applications govern cars, but they still demand features like 360º camera vision as well as connected and cloud-based systems that provide entertainment, over-the-air updates, and other smartphone-like capabilities. Most drivers don’t know that the harness is directly responsible for enabling a new generation of software-defined vehicles, but they expect predictive maintenance applications for a better experience. And car makers know that instead of a recall, a software update can help save a lot of time, significantly reduce costs, and improve brand appreciation.
Today, software increasingly controls every aspect of the car, thanks in part to the rise of real-time virtualization, which improves the use of hardware resources by ensuring developers can do more with the same components. It’s all about decoupling the code from what it runs on. Thanks to containers and hypervisors, it is possible to run multiple software modules on one hardware ecosystem and still enjoy proper segregation to protect against interference. The technology is already popular in servers and data centers to create secure, safe, and efficient systems. It’s no wonder car makers are bringing it to their new vehicles.
Another advantage of this software paradigm is that it is responsible for the explosion of data generation and the centralization of processing capabilities for improved analysis and decision-making. New architectures have enabled car makers to install hundreds of sensors when they were limited to a few dozen in previous platforms. And more importantly, thanks to the more powerful ECUs and HPCUs, OEMs can future-proof systems and run powerful algorithms but still enjoy a more straightforward development experience. If one software platform can run more applications, it will enable car makers to offer more and richer features while keeping costs down, and ensure consumers get more value out of their vehicles.
Hardware metamorphosisAs we alluded to, the advent of software-defined vehicles and the decoupling of the hardware from the application is only possible if car makers choose microcontrollers and microprocessors that can meet their safety requirements while also offering the computational power and hardware IPs necessary to make this a reality. Engineers must find devices that can support real-time virtualization, numerous I/Os, and a large, embedded, and fast memory that facilitates over-the-air updates. MCUs must be designed and certified for automotive use with specialized safe redundancy built-in, especially as ECUs handle more and more safety applications.
It’s easy to see that this new evolution in car architecture represents a unique electrical challenge, as engineers must create robust, safe, and efficient power distribution mechanisms. It’s the reason why many are adopting smart switches. Unlike the classic melting fuses and mechanical relays, these new electronic switches are faster. As a result, they can offer far greater protection against an adverse electrical event because they respond much quicker than classical components. Their electronic nature also makes them vastly more accurate and flexible. Indeed, they come with monitoring features to enable real-time load management and control. Moreover, they are resettable, which saves from having to replace them manually.
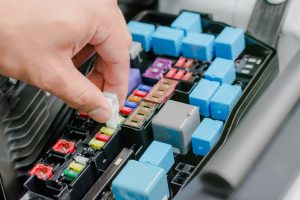
Another critical benefit of smart fuses is their tiny size compared to traditional switches and relays. Because eFuses are so small and electronically controlled, car makers can use shorter harnesses since, among other things, they no longer need to route cables to a large fuse box that must be user accessible. Moreover, the significantly higher accuracy means that the harness can be thinner, thus further contributing to weight reduction. A smaller design with fewer components that are more robust and accurate also helps improve overall reliability. Hence, while some engineers are still evaluating the cost of eFuses, the overall savings over the architecture’s lifetime explain their increasing popularity.
Taking a step back, we see that power distribution is also a much more critical engineering challenge because vehicles are dealing with far greater loads. Most architectures must handle 12 V, but the industry is moving to 48 V. EV chargers must also be able to handle very high voltages and power levels (up to 3,500 kW today). Hence, one of the most popular solutions is to use wide bandgap devices, such as silicon carbide (SiC). The fast switching frequencies of SiC MOSFETs and diodes mean they can handle a lot more power without the energy losses of previous devices, enabling smaller traction inverters, faster charging modules, and more efficient compressors, among other things.
The evolving role of semiconductor companies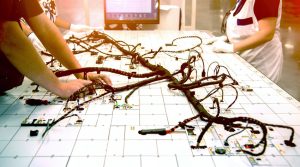
The domain and zonal car architectures emerging today testify to a new reality: everything is connected, and all roads (harnesses, in this case) lead to close cooperation between the key actors of the industry – car makers, Tier 1s, and semiconductor companies. Companies like ST understand how to support platform designers in their quest to decouple the hardware from the software and improve efficiency, safety, and robustness. Together, they create the innovations essential to the future of vehicles that will drive demand for the next generation of cars. It’s for this reason that existing carmakers and new startups are creating ever more intimate partnerships with semiconductor makers and why the market is going through such a disruption.
ST’s ability to grasp new engineering challenges is evidenced through its products. The Stellar family of devices has unique virtualization capabilities to future-proof the software-driven vehicles of tomorrow while its software ecosystem helps reduce development times and meet regulatory requirements. Similarly, STi²Fuse can shrink the overall harness, reduce the bill of materials, and optimize the overall power distribution. Additionally, silicon carbide power devices continue to bring new levels of efficiency. In essence, it’s by offering a wide range of solutions that semiconductor companies can be the close partners that car makers need them to be as they drive the new architectures that will meet the hopes and expectations of their customers.
The post The hidden car revolution: zonal architecture appeared first on ELE Times.
Project “Genial”: Joint electronics roadmap for innovations in the automotive value chain
The automotive industry is facing significant technological challenges in developing new and innovative features and services. When defining their products, vehicle manufacturers must anticipate future technical advancements in microelectronic platforms, sensors, and semiconductor technologies. At the same time, suppliers and semiconductor manufacturers need early insights into the requirements for upcoming features and services to be able to invest in technology development with confidence.
As part of the “GENIAL!” project funded by the Federal Ministry of Education and Research (BMBF), eleven partners collaborated to develop concepts and methods that help companies in the automotive industry work together more effectively and prepare for the future. The project specifically focused on optimizing the collaboration between automotive manufacturers and their component and technology suppliers to accelerate innovation across the automotive value chain.
The prototypical automotive microelectronics roadmap developed in GENIAL! provides a strategic framework for identifying future market needs, use cases, system models, and technical requirements in the field of automotive microelectronics. This roadmap establishes a shared understanding of the microelectronics requirements of future highly innovative vehicles across the entire value chain. The results enable all market participants, as well as research institutions and policymakers, to manage investments and research activities more effectively. In turn, this facilitates the implementation of significantly shorter and more reliable development processes, allowing new, innovative automotive components to be realized more quickly.
The project was based on a model-based system development approach that utilizes the Systems Modeling Language (SysML) as a modeling language, now integrated into SysML v2. This approach is supported by the AGILA database and further enhanced by the IRIS (Interactive Roadmapping of Innovative Systems) tool, both developed within the project. AGILA serves as a centralized database for capturing the essential information and providing documentation, consistency checks, and version control.
The IRIS tool enables collaborative modeling, exploration, planning, and evaluation of solution alternatives. It also supports non-technical information, allowing considerations such as security of supply, and enables visualizations for roadmapping. To encourage widespread adoption, the project participants will release tools such as AGILA and IRIS as open-source solutions, making them accessible for anyone interested in creating and maintaining roadmaps.
The innovation modeling methodology “IMoG” (Innovation Modelling Grid) defines activities, roles, and process models for the collaborative creation of roadmaps. This spans from the initial comparison of models in the problem and solution space to the practical application of the AGILA and IRIS tools. Documentation of the methodology, along with several training videos, is available for free download.
The post Project “Genial”: Joint electronics roadmap for innovations in the automotive value chain appeared first on ELE Times.
I have an x ray tube in my workshop
![]() | submitted by /u/antek_g_animations [link] [comments] |
Violated a few regulations, but it works soo well, why doesnt anyone make sth like this
![]() | submitted by /u/Formal-Fan-3107 [link] [comments] |
Student calls International Space Station with his Magnetometer+Accelerometer-based Satellite Tracker
![]() | submitted by /u/KJ7LNW [link] [comments] |
Weekly discussion, complaint, and rant thread
Open to anything, including discussions, complaints, and rants.
Sub rules do not apply, so don't bother reporting incivility, off-topic, or spam.
Reddit-wide rules do apply.
To see the newest posts, sort the comments by "new" (instead of "best" or "top").
[link] [comments]
Quantum Computing Meets Classical Electronics: Bridging Two Worlds for Next-Generation Computing
The field of computing is undergoing a transformative shift with the advent of quantum computing. While classical electronics have been the backbone of digital technology for decades, quantum computing promises to unlock unprecedented computational capabilities. However, these two paradigms are not mutually exclusive; rather, they can complement each other, leading to more efficient and powerful computing architectures. This article explores the latest developments in integrating quantum computing with classical electronics, detailing the technical challenges, innovative solutions, and future implications.
The Foundations: Understanding Classical and Quantum Computing Classical Electronics: The Workhorse of Modern ComputingClassical computing is built on the foundation of semiconductor-based electronics, primarily leveraging transistors, integrated circuits, and Boolean logic. It operates on bits, which can either be in the state of 0 or 1, and relies on deterministic algorithms to process information.
Quantum Computing: The Next FrontierQuantum computing introduces a fundamentally different approach, utilizing qubits instead of bits. Qubits can exist in superposition, meaning they can represent both 0 and 1 simultaneously, and leverage entanglement for highly efficient parallel computations. This enables quantum systems to solve problems that are infeasible for classical computers, such as complex optimizations, cryptographic analysis, and molecular simulations.
Bridging the Gap: Integrating Quantum and Classical SystemsQuantum processors (QPUs) do not operate in isolation; they require classical electronics for control, measurement, and data processing. The integration of these two domains is critical to making quantum computing practical and scalable.
Classical Control of Quantum Systems- Cryogenic CMOS Electronics: Since qubits operate at extremely low temperatures (near absolute zero), classical control electronics must function reliably at cryogenic conditions. Innovations in cryogenic CMOS technology enable signal processing and qubit manipulation without excessive thermal noise.
- High-Speed Digital-to-Analog and Analog-to-Digital Converters (DAC/ADC): These components are crucial for translating classical instructions into precise qubit operations and reading quantum state measurements.
- Low-Latency Error Correction: Quantum error correction requires real-time classical processing to mitigate decoherence and maintain computational accuracy. Specialized classical processors are being developed to handle these operations efficiently.
Many quantum algorithms require classical pre- and post-processing. Examples include:
- Variational Quantum Eigensolver (VQE): Used in quantum chemistry, where a classical optimizer adjusts quantum circuit parameters to minimize energy states.
- Quantum Approximate Optimization Algorithm (QAOA): A hybrid approach that leverages quantum computation for complex combinatorial problems while using classical methods for optimization refinement.
As quantum processors scale up, the overhead on classical electronics increases significantly. The interconnect complexity, power consumption, and latency must be optimized to handle thousands of qubits efficiently.
Heat DissipationOperating classical electronics near quantum processors requires careful thermal management to prevent interference with qubit coherence. New materials and low-power circuit designs are being explored to address this issue.
Data Transfer BottlenecksQuantum computations generate vast amounts of data that must be efficiently transferred to classical processors for analysis. Advanced data compression and high-speed interconnects are being developed to enhance performance.
Emerging Solutions and Innovations Photonic InterconnectsOptical communication is being explored to connect classical and quantum systems with minimal signal degradation. Photonic links enable faster and more reliable transmission of control signals and readout data.
Neuromorphic Computing for Quantum Error CorrectionNeuromorphic processors, which mimic the human brain’s neural networks, are being investigated to handle real-time quantum error correction more efficiently than traditional digital processors.
AI-Assisted Quantum ControlMachine learning algorithms are being integrated into quantum control systems to optimize pulse sequences, error correction strategies, and system calibrations dynamically.
Future Directions: Towards a Quantum-Classical Hybrid EraThe future of computing lies in a seamless fusion of quantum and classical technologies. Research is progressing towards developing quantum-classical hybrid architectures that harness the best of both worlds. Potential advancements include:
- On-Chip Integration: Embedding quantum and classical components onto the same chip to reduce latency and improve scalability.
- Fault-Tolerant Quantum Systems: Advancements in quantum error correction that minimize the need for excessive classical post-processing.
- Cloud-Based Quantum Computing: Platforms where classical systems offload computationally intensive tasks to quantum processors over high-speed networks.
The integration of quantum computing with classical electronics represents a monumental leap in computational capabilities. By overcoming current technical challenges, researchers are paving the way for a new era of computing where quantum and classical systems work in unison to solve the most complex problems. The convergence of these technologies will not only drive breakthroughs in artificial intelligence, materials science, and cryptography but also redefine the limits of human knowledge and innovation.
The post Quantum Computing Meets Classical Electronics: Bridging Two Worlds for Next-Generation Computing appeared first on ELE Times.
ROHM’s New General-Purpose Chip Resistors Contribute to Greater Miniaturization
Achieves equivalent rated power in a smaller size with guaranteed stable long-term supply
ROHM has expanded its portfolio of general-purpose chip resistors with the MCRx family. It is designed to achieve greater miniaturization and enhanced performance across a variety of applications. The new lineup includes the high-power MCRS series and low-resistance, high-power MCRL series.
In today’s era of advancing functionality and electrification, the increased miniaturization and improved performance of electronic components have become critical issues. This is especially evident in the automotive market, where the proliferation of electric vehicles (xEVs) is accelerating the use of electronic components. Similarly, the industrial equipment market is experiencing growing demand for compact, high performance electronic components as machinery becomes more functional and efficient. ROHM addresses both of these needs with the MCRx family of compact, high-performance resistors.
The MCRS series improves rated power and TCR (Temperature Coefficient of Resistance) characteristics by optimizing the internal structure and incorporating new materials, enabling use in a smaller size compared to conventional products. A broad lineup in sizes ranging from 0402-size (0.04inch × 0.02inch) / 1005-size (1.0mm × 0.5mm) to 2512-size (0.25inch × 0.12inch) / 6432-size (6.4mm × 3.2mm) is available, making it possible to select the ideal product based on mounting space requirements. This leads to a compact, efficient circuit design, significantly increasing design flexibility. Meanwhile, the MCRL series, a low-resistance variant of the MCRS series, is offered in sizes ranging from 0805-size (0.08inch × 0.05inch) / 2012-size (2.0mm × 1.2mm) to 2512-size (0.25inch × 0.12inch) / 6432-size (6.4mm × 3.2mm) ideal for current detection applications.
The MCRx family adopts a redesigned internal structure, improving production efficiency, quality, and product reliability across all sizes. Compliant with the AEC-Q200 automotive reliability standard, this series meets the increasing demand for electric vehicles (xEVs) while contributing to market expansion in communications infrastructure such as base stations and servers as well as factory automation equipment. In addition, the products are designated for long-term stable supply, supporting continuous use in long-life applications such as industrial equipment.
The MCRS series will be expanded to include compact 0201-size (0.024inch × 0.012inch) / 0603-size (0.6mm × 0.3mm) products capable of withstanding temperatures up to +155°C. At the same time, the MCRE series will soon offer completely lead-free 01005-size (0.016inch × 0.008inch) / 0402-size (0.4mm × 0.2mm) products. These additions will allow ROHM to respond to the demand for further miniaturization while complying with environmentally-driven voluntary regulations and export restrictions.
Going forward, ROHM is focused on developing and manufacturing products that cater to the diverse needs of customers worldwide. In particular, ROHM will continue to expand its lineup of resistors (its founding products) that improve miniaturization and reliability while ensuring long-term stable supply. By consistently delivering new value through technological innovation, ROHM seeks to solidify its market position and drive the evolution of electronic components.
Product Lineup MCRS Series <High-Power Type> MCRL Series <Ultra-Low Ohmic ・ High Power Type> MCRE Series <Completely Lead-Free Type> Application ExamplesSuitable for a wide range of applications (excluding medical, military, aerospace, and nuclear control equipment)
Automotive- Electric vehicles (xEVs): Battery Management Systems (BMS), powertrain control, Advanced Driver Assistance Systems (ADAS)
- In-vehicle electronics: Engine Control Units (ECUs), infotainment systems, and more
- Robotics: Control systems for industrial robots
- Factory Automation (FA): Automated product line control systems
- Power conversion equipment: Inverters, converters, and more
- Smart devices: Smartphones, tablets, wearables
- Home appliances: TVs, refrigerators, washing machines
- Network equipment: Routers, switching hubs, communication equipment for data centers, etc.
The post ROHM’s New General-Purpose Chip Resistors Contribute to Greater Miniaturization appeared first on ELE Times.
u-blox expands its NORA-B2 Bluetooth LE modules series using the nRF54L chipsets to address all mass market segments
The new nRF54L chipset-based wireless modules reduce current consumption and double processing capacity, catering to diverse mass market segments.
u-blox a global leader in positioning and short-range communication technologies for automotive, industrial, and consumer markets has expanded its portfolio by introducing six new variants of the NORA-B2 Bluetooth Low Energy modules. Now integrating the entire range of Nordic Semiconductor’s next-level nRF54L Series of ultra-low power wireless Systems-on-Chip (SoCs), NORA-B2 offers a versatile solution for mass market segments thanks to its choices of antennas, architectures and chipsets.
The new additions keep delivering on NORA-B2 promises, providing multiple operational benefits. The wireless modules combine ultra-lower power consumption and high processing efficiency, consuming up to 50% less current than previous-generation devices while doubling process capacity. They also offer outstanding security features, which makes them ideal for a wide range of IoT applications, such as smart home devices, industrial automation, or healthcare.
The entire NORA-B2 series comprises four variants that differ in memory sizes, design architectures and price levels to match almost any device manufacturer’s requirements.
- NORA-B20 uses ultra-low power nRF54L15 SoC and integrates a 128 MHz Arm Cortex-M33 processor, a RISC-V co-processor, and an ultra-low power multiprotocol 2.4 GHz radio. It comes with 1.5 MB of Non-Volatile Memory (NVM) and 256 KB RAM.
- NORA-B21, based on ultra-low power nRF54L10 SoC, is designed for mid-range applications. It has 1.0 MB of NVM and 192 KB of RAM and can handle multiple wireless protocols simultaneously, including Bluetooth LE, Bluetooth Mesh, Thread, Matter, Zigbee, and Amazon Sidewalk.
- NORA-B22 is designed for cost-sensitive applications but still provides access to up to 31 GPIOs. It offers 0.5 MB of NVM and 96 KB of RAM.
- NORA-B26 is designed for customers using the Network Co-Processor architecture and comes pre-flashed with the u-blox u-connectXpress software, allowing customers to easily integrate Bluetooth connectivity into their products with no prior knowledge of Bluetooth LE or wireless security.
All NORA-B2 modules are designed for PSA Certified Level 3 security. They incorporate features such as secure boot and updates, tamper detection, and secure firmware over-the-air (FOTA) updates. These security measures ensure that IoT devices remain protected against any potential threats, safeguarding both data and functionality. NORA-B2 modules are also qualified against Bluetooth Core 6.0 that includes Channel Sounding, enabling endless cost-effective possibilities in tracking and locating use cases.
NORA-B2 variants either come with an antenna pin for connecting an external antenna of choice or are designed with a patented PCB antenna providing best-in-class RF performance. All module versions come with global certification allowing device manufacturers to launch their products worldwide with minimal effort.
“We are excited to see Nordic’s entire nRF54L Series of SoCs seamlessly integrated into the NORA-B2 module series. The market demand for energy-efficient solutions at a competitive cost is growing rapidly, and this product category is well-positioned to meet that need. u-blox’s commitment to staying ahead of industry and market trends reinforces our confidence in this valuable partnership,” says Thomas Holmberg, Regional Sales Director at Nordic Semiconductor.
Samples of NORA-B20 are now available. Early samples of NORA-B21 and NORA-B22 are available for evaluation in limited quantities. The pre-release version of u-connectXpress software for NORA-B26 is also available for early adopters. For more information on the NORA-B2 series and how it can benefit your IoT projects, visit the u-blox website or contact your local u-blox salesperson or distribution partner.
The post u-blox expands its NORA-B2 Bluetooth LE modules series using the nRF54L chipsets to address all mass market segments appeared first on ELE Times.
Infineon expands package choices for SiC MOSFETs

Infineon has introduced Q-DPAK and TOLL package options to its lineup of 650-V CoolSiC Generation 2 (G2) MOSFETs. Leveraging G2 technology, these devices enable faster switching and lower power losses in high- and medium-power switched-mode power supplies for AI servers, EV chargers, and renewable energy equipment.
With thermal cycling onboard, the TOLL package reduces PCB footprint, enabling compact system designs. In SMPS applications, it can also help lower system-level manufacturing costs.
The Q-DPAK expands Infineon’s topside-cooled product family, which includes CoolSiC, CoolMOS, CoolGaN, and OptiMOS devices. Designed for maximum power density and efficiency, these devices achieve 95% direct heat dissipation, allowing both sides of the PCB to be used for improved space management and reduced parasitic effects.
The 650-V CoolSiC G2 MOSFETs in TOLL packages are available with on-resistance values ranging from 10 mΩ to 60 mΩ. Q-DPAK variants are available with on-resistance values of 7 mΩ, 10 mΩ, 15 mΩ, and 20 mΩ.
Find more datasheets on products like this one at Datasheets.com, searchable by category, part #, description, manufacturer, and more.
The post Infineon expands package choices for SiC MOSFETs appeared first on EDN.
Diodes afford ESD protection for automotive networks

Nexperia’s PESD1ETH10 diodes protect sensitive electronics in 10Base-T1S in-vehicle networks from ESD damage. With a maximum capacitance of 0.4 pF, they also support higher-speed 100Base-T1 and 1000Base-T1 automotive networks while maintaining signal integrity. Additionally, the devices comply with Open Alliance requirements, ensuring EMC performance and robustness for 10Base-T1S networks.
PESD1ETH10 diodes deliver single-line ESD protection up to 18 kV (IEC 61000-4-2) and up to 15 kV for 1000 discharges (Open Alliance). These diodes cover the full range of automotive board net voltages, including 12 V for cars, 24 V for trucks and commercial vehicles, and 48 V for hybrid and electric vehicles.
High-bandwidth 100Base-T1 and 1000Base-T1 networks drive automotive connectivity, but many legacy systems still use older standards like CAN and LIN. Replacing these with 10Base-T1S simplifies integration, offering a unified network for all automotive applications. The PESD1ETH10 diodes provide ESD protection across all automotive Ethernet networks, streamlining board designs and supply chains.
The PESD1ETH10L-Q is offered in a 1.0×0.6×0.48-mm DFN1006-2 package, while the PESD1ETH10LS-Q comes in a 1.0×0.6×0.37-mm DFN1006BD-2 package with side-wettable flanks for automated optical inspection.
Find more datasheets on products like this one at Datasheets.com, searchable by category, part #, description, manufacturer, and more.
The post Diodes afford ESD protection for automotive networks appeared first on EDN.
Software enables seamless IoT device management

congatec’s aReady.IOT software building blocks offer secure IoT connectivity from the company’s aReady.COM computer-on-modules to the cloud. With aReady.IOT, users can focus on their core competencies while congatec simplifies application development, enabling seamless communication and data transfer between systems and devices.
aReady.IOT allows users to remotely monitor, control, and manage their aReady.COM-based applications, connected peripherals, and sensors. These preconfigured blocks support communication via protocols such as OPCUA, MQTT, and REST. Acquired data can be used for maintenance, management, and predictive maintenance. Additionally, data can be processed at the edge for storage and visualization.
Preconfigured modules in aReady.IOT offer a range of scalable services across both application hardware and software layers. The COM Manager, Application Manager, and Fleet Manager each provide unique capabilities to optimize different aspects of the application. Additionally, congatec can offer bi-directional cloud connectivity via the Cloud Connector, supporting services like AWS, Azure, or Telekom Cloud.
Find more datasheets on products like this one at Datasheets.com, searchable by category, part #, description, manufacturer, and more.
The post Software enables seamless IoT device management appeared first on EDN.
QuickLogic enhances eFPGA design tool

Version 2.9 of the Aurora embedded FPGA tool suite from QuickLogic enables seamless integration of block RAM (BRAM) and DSP functions. Along with its new BRAM and DSP IP configurator, the software’s place and route tools improve runtime by up to 2 times.
Other upgrades in Aurora 2.9 include custom function support, which enables the instantiation of lookup table (LUT) macros to create custom functions. The release also introduces interactive path analysis within the new GUI, allowing users to debug design timing in greater detail by highlighting critical path routing. This visibility helps users make informed adjustments to improve timing performance.
Aurora’s inferencing feature streamlines the implementation of reconfigurable computing algorithms by automatically adapting BRAM read/write widths, eliminating the need for manual RTL design modifications.
The Aurora eFPGA development tool suite is now available for Windows 10/11 and major Linux distributions, including CentOS, RedHat, and Ubuntu, via a unified Linux installer. The Aurora Pro version supports Synopsys Synplify for logic synthesis.
Find more datasheets on products like this one at Datasheets.com, searchable by category, part #, description, manufacturer, and more.
The post QuickLogic enhances eFPGA design tool appeared first on EDN.
u-blox grows Bluetooth LE module portfolio

New variants in the u-blox Nora-B2 Bluetooth LE 6.0 module family integrate Nordic Semiconductor’s entire nRF54L series of ultra-low power wireless SoCs. Offering a choice of antennas and chipsets, these modules consume up to 50% less current than previous-generation devices while doubling processing capacity.
The NORA-B2 series comprises four variants that differ in memory size, design architecture, and price level. Each variant comes with either an antenna pin or embedded antenna.
- NORA-B20 features an nRF54L15 SoC and integrates a 128-MHz Arm Cortex-M33 processor, a RISC-V coprocessor, and an ultra-low power multiprotocol 2.4-GHz radio. It comes with 1.5 MB of NVM and 256 KB RAM.
- NORA-B21, based on an nRF54L10 SoC, is designed for mid-range applications. It has 1.0 MB of NVM and 192 KB of RAM and handles multiple wireless protocols simultaneously, including Bluetooth LE, Bluetooth Mesh, Thread, Matter, Zigbee, and Amazon Sidewalk.
- NORA-B22 employs an nRF54L05 SoC. It is intended for cost-sensitive applications but still provides access to up to 31 GPIOs. It includes 0.5 MB of NVM and 96 KB of RAM.
- NORA-B26, based on an nRF54L10, is designed for customers using the network coprocessor architecture. It comes pre-flashed with the u-blox u-connectXpress software, allowing customers to easily integrate Bluetooth connectivity into their products with no prior knowledge of Bluetooth LE or wireless security.
All NORA-B2 modules are designed for PSA Certified Level 3 security and meet the Bluetooth Core 6.0 specification, including channel sounding for accurate ranging. They also carry global certification, enabling manufacturers to launch products worldwide with minimal effort.
NORA-B20 samples are available now, while NORA-B21 and B22 are in limited evaluation. A pre-release of u-connectXpress for NORA-B26 is available for early adopters.
Find more datasheets on products like this one at Datasheets.com, searchable by category, part #, description, manufacturer, and more.
The post u-blox grows Bluetooth LE module portfolio appeared first on EDN.
Why RISC-V is a viable option for safety-critical applications

As safety-critical systems become increasingly complex, the choice of processor architecture plays an important role in ensuring functional safety and system reliability. Consider an automotive brake-by-wire system, where sensors detect the pedal position, software interprets the driver’s intent, and electronic controls activate the braking system. Or commercial aircraft relying on flight control computers to interpret pilot inputs and maintain stable flight. Processing latencies or failures in these systems could result in unintended behaviors and degraded modes, potentially leading to fatal accidents.
The RISC-V architecture’s inherent characteristics—modularity, simplicity, and extensibility—align with the demands of functional safety standards like ISO 26262 for automotive applications and DO-178C for aviation software. Unlike proprietary processor architectures, RISC-V is an open standard instruction set architecture (ISA) developed by the University of California, Berkeley, in 2011. The architecture follows reduced instruction set computing (RISC) principles, emphasizing performance and modularity in processor design.
RISC-V is set apart by its open, royalty-free nature combined with a clean-slate design that eliminates the legacy compatibility constraints of traditional architectures. The ISA is structured as a small base integer set with optional extensions, allowing processor designers to implement only the features needed for their specific applications.
This article examines the technical advantages and considerations of implementing RISC-V in safety-critical environments.
Benefits for safety-critical industriesTraditional proprietary architectures, such as Arm, have served safety-critical industries well, but challenges around supplier diversity, customization needs, and safety certification requirements have driven interest in RISC-V.
The following sections describe characteristics of RISC-V that make it a viable option for safety-critical development teams.
Architectural independenceOne fundamental challenge in developing safety-critical systems is mitigating supply chain risks. Traditional processor architectures require licensing agreements and create vendor lock-in, which impacts long-term system maintainability and cost.
RISC-V’s open model provides several advantages. The ability to work with multiple silicon vendors reduces single-point-of-failure risks in the supply chain. This is particularly important for long-lifecycle applications in aerospace and automotive, where systems may need to be maintained and supported for decades. When using RISC-V, manufacturers expand their options for semiconductor suppliers and development tool ecosystems, providing flexibility in responding to supply chain issues.
Customization to meet safety-critical requirementsRISC-V’s modular design philosophy allows silicon vendors and system architects to implement custom features at the hardware level. This capability helps address specific safety requirements across mission-specific applications certification standards such as:
- Custom error detection and correction.
- Hardware-level monitoring and diagnostic capabilities.
- Low-latency, deterministic execution features for real-time requirements.
Additionally, RISC-V silicon vendors have products supporting harsh environments, such as processors with radiation hardening and electromagnetic pulse (EMP) protection for space applications.
Memory managementOne of RISC-V’s distinguishing features is its approach to cache memory management, helping developers of safety-critical applications requiring deterministic behavior. The ability to implement level 2 cache memory mapping as RAM gives developers greater control over system latency, a crucial factor in real-time safety-critical applications.
This capability addresses challenges covered in aviation safety guidelines like EASA AMC 20-193 and FAA AC 20-193. By providing better solutions for cache contention mitigation than traditional architectures, RISC-V supports more predictable execution timing—a critical requirement for safety certification.
Dissimilar redundancySafety-critical systems requiring design assurance level A (DAL-A) certification under DO-178C often implement redundancy to protect against common mode failures. RISC-V’s open architecture provides advantages in implementing dissimilar redundancy strategies:
- Implementation of different processor configurations within the same system.
- Diverse redundancy schemes using different vendor solutions.
- Using different architectures in mixed-criticality systems with varying levels of safety requirements.
While RISC-V may not always match the raw performance metrics of modern Arm implementations, its architecture provides several advantages specific to safety-critical applications. The ability to implement custom instructions and hardware features allows optimization for specific safety requirements without compromising overall system performance.
Key performance-related features include:
- Deterministic execution paths for real-time applications.
- Custom instructions for safety monitoring.
- Efficient context switching for mixed-criticality systems.
- Configurable memory protection units to minimize stack and data corruption.
Over the years, the maturation of development tools and verification environments for RISC-V has expanded to cover the entire software lifecycle. For example, LDRA’s target license package (TLP) for RISC-V architectures supports development and on-target testing with multi-core code coverage analysis, worst-case execution time (WCET) measurement for AMC 20-193 compliance, requirements traceability, and integration with major RISC-V development platforms. This TLP makes RISC-V ready for safety and security.
Additionally, LDRA is highly integrated with RISC-V environments, supporting dynamic testing with hardware and commercial and open-source simulation environments, including silicon-level simulation. These environments support comprehensive hardware-accurate testing and verification to develop and test software as the hardware is developed.
Industry momentum around RISC-VA growing number of safety-certified RISC-V IP cores offer designers pre-verified components that meet stringent safety requirements. Microchip, SiFive, CAST, and other vendors have released specialized RISC-V implementations with integrated safety features, fault detection mechanisms, and redundancy capabilities tailored for automotive and aerospace applications. Vendors such as Frontgrade Gaisler add to this with radiation-hardened microprocessors and IP cores for space-based systems.
The mix of industry support, technical guidelines, and certification tools creates a positive feedback loop that accelerates RISC-V adoption in safety-critical systems, making it increasingly attractive for organizations developing next-generation applications.
Jay Thomas, technical development manager for LDRA Technology, San Bruno, Calif., and has worked on embedded controls simulation, processor simulation, mission- and safety-critical flight software, and communications applications in the aerospace industry. His focus on embedded verification implementation ensures that LDRA clients in aerospace, medical, and industrial sectors are well grounded in safety-, mission-, and security-critical processes. For more information about LDRA, visit http://www.ldra.com.
Related Content
- Standards, tools address coding and application errors in embedded software
- Software development model for the ISO/SAE 21434 standard
- How ‘shift left’ helps secure today’s connected embedded systems
- CES 2021: RISC-V’s journey from experimentation to commercial processors
- Accelerating RISC-V development with network-on-chip IP
- Developing safety critical ASICs for ADAS and similar automotive systems
The post Why RISC-V is a viable option for safety-critical applications appeared first on EDN.
Hyper-Accurate Sensors for Industry 5.0: Transforming Precision and Intelligence in Smart Manufacturing
Industry 5.0 represents the next leap in industrial evolution, emphasizing human-machine collaboration, hyper-connectivity, and AI-driven automation. Unlike Industry 4.0, which focused on full automation and cyber-physical systems, Industry 5.0 integrates human intelligence with advanced technology to achieve greater efficiency, sustainability, and personalization.
At the core of this transformation are hyper-accurate sensors, which provide real-time, high-precision data essential for advanced robotics, AI-driven decision-making, and intelligent manufacturing. These sensors are the backbone of predictive maintenance, digital twins, adaptive production lines, and self-optimizing industrial systems, ensuring unprecedented levels of control, efficiency, and reliability.
Why Hyper-Accurate Sensors Are Critical for Industry 5.0As manufacturing becomes more sophisticated, the demand for ultra-precise and reliable sensors is at an all-time high. Key drivers include:
- High-Precision Manufacturing – Miniaturization and complex geometries require sensors with nanometer-level accuracy.
- Predictive Maintenance & Self-Healing Systems – Sensors that detect anomalies in real time prevent costly downtime and enable proactive repairs.
- Human-Robot Collaboration (HRC) & Intelligent Automation – Ultra-sensitive sensors ensure safe interaction between humans and machines.
- Autonomous Quality Control & Zero-Defect Manufacturing – AI-driven defect detection improves production efficiency and minimizes waste.
- Sustainability & Energy Efficiency in Smart Factories – Smart sensors optimize energy consumption and reduce environmental impact through adaptive control mechanisms.
- Quantum Sensors: Unlocking Unprecedented Measurement Precision
Quantum sensors leverage principles of quantum mechanics to achieve unparalleled accuracy in detecting changes in electric, magnetic, or gravitational fields. Applications include:
- Ultra-precise gyroscopes for navigation in GPS-denied environments.
- Magnetometers for non-invasive fault detection in industrial machinery.
- Quantum-enhanced gravimeters for structural health monitoring in factories and critical infrastructure.
- AI-Enhanced Edge Sensors for Intelligent Decision-Making
Traditional sensors generate raw data, but AI-powered sensors process and analyze this data at the edge, reducing latency and improving response times. Key benefits include:
- Self-learning capabilities to detect micro-level deviations before failures occur.
- Real-time data fusion for complex multi-sensor environments.
- AI-driven self-calibration to enhance long-term accuracy and minimize drift.
- LiDAR and 3D Vision Sensors for High-Resolution Spatial Awareness
LiDAR (Light Detection and Ranging) is a critical technology in smart factories, offering:
- Millimeter-accurate object detection for precision robotic manipulation.
- 3D mapping of industrial spaces for dynamic logistics and warehouse automation.
- Precision alignment of micro-components in semiconductor and electronics manufacturing.
- Piezoelectric and Optical Sensors for Sub-Nanometer Accuracy
Advanced piezoelectric and optical interferometric sensors are redefining precision in industrial applications:
- Sub-nanometer resolution for micro-machining and semiconductor fabrication.
- Non-contact displacement sensing for wear monitoring and material integrity assessment.
- Ultra-fast response times for real-time vibration analysis in high-speed machinery.
- MEMS and NEMS Sensors for Scalable Miniaturized Accuracy
Micro-Electro-Mechanical Systems (MEMS) and Nano-Electro-Mechanical Systems (NEMS) enable:
- Microfluidic sensing for real-time chemical composition monitoring.
- MEMS accelerometers for high-frequency shock and vibration detection in aerospace and defense industries.
- NEMS-based temperature sensors for extreme precision in semiconductor and biotech applications.
- Predictive Maintenance & Self-Optimizing Machinery
Hyper-accurate sensors detect micro-failures and degradation patterns before catastrophic failures occur, allowing manufacturers to:
- Reduce unplanned downtime by up to 50% through early fault detection.
- Extend machinery lifespan by 30-40% through adaptive maintenance strategies.
- Minimize operational costs by shifting from scheduled maintenance to data-driven predictive servicing.
- Digital Twins & AI-Powered Real-Time Simulation
A digital twin is a dynamic virtual replica of a physical system, powered by sensor data. Benefits include:
- Continuous real-time performance monitoring for process optimization.
- Virtual simulation of process changes before deployment to mitigate risks.
- AI-driven real-time decision-making for adaptive control of industrial processes.
- Human-Robot Collaboration (HRC) & Adaptive Safety Mechanisms
For seamless interaction between humans and machines, hyper-accurate sensors enable:
- Proximity detection with sub-millimeter precision to prevent accidents.
- Haptic feedback and force sensing to enhance robotic dexterity.
- Gesture and motion recognition for intuitive human-machine interaction in manufacturing environments.
- Zero-Defect Manufacturing & Autonomous Quality Control
Advanced sensors revolutionize automated quality inspection with:
- High-resolution optical sensors and X-ray imaging for real-time defect detection.
- AI-driven pattern recognition to identify microscopic production deviations.
- Closed-loop feedback systems that dynamically adjust manufacturing processes to prevent defects in real time.
- Sustainable Smart Manufacturing & Energy Optimization
Smart sensors contribute to sustainability by:
- Monitoring real-time energy consumption at component and system levels.
- Optimizing heating, cooling, and power distribution for energy efficiency.
- Reducing material waste through precision control and automated resource allocation.
- Overcoming Data Overload with AI & Edge Computing
With sensors generating terabytes of data per second, real-time processing and intelligent filtering are critical. Future research will focus on:
- AI-enhanced edge computing architectures to reduce latency.
- Neural network-driven anomaly detection for automated decision-making.
- Federated learning models to enable cross-factory data integration without compromising security.
- Cost & Scalability of Quantum and AI Sensors
While quantum and AI-enhanced sensors offer unmatched precision, their adoption is hindered by high costs and integration complexity. Solutions include:
- Mass-scale nanofabrication for cost-effective sensor production.
- AI model optimization to enable lightweight processing on embedded systems.
- Hybrid sensor architectures that balance cost, accuracy, and efficiency.
- Cybersecurity & Interoperability in Sensor Networks
With increasing connectivity, sensor networks are vulnerable to cyber threats. Key future developments include:
- Blockchain-secured sensor networks for data integrity.
- Universal communication protocols for seamless cross-industry adoption.
- AI-driven anomaly detection for real-time cyber threat mitigation.
Hyper-accurate sensors are the cornerstone of Industry 5.0, enabling intelligent, efficient, and sustainable industrial ecosystems. As quantum sensing, AI-enhanced analytics, and edge computing converge, we are moving toward a future where factories operate with zero waste, predictive intelligence maximizes uptime, and human-machine collaboration reaches unprecedented synergy. The next decade will witness transformative breakthroughs in sensor technology, shaping the future of smart manufacturing, robotics, and industrial automation.
The post Hyper-Accurate Sensors for Industry 5.0: Transforming Precision and Intelligence in Smart Manufacturing appeared first on ELE Times.
Meta-Materials in Electronics: Revolutionizing Next-Generation Devices
Meta-materials have emerged as an innovative class of engineered materials designed to manipulate electromagnetic, acoustic, and thermal waves in unprecedented ways. Unlike conventional materials, whose properties are defined by their chemical composition, meta-materials derive their unique functionalities from carefully structured microscopic architectures. This ability to control wave propagation has opened new frontiers in electronics, enabling advanced antennas, ultra-sensitive sensors, and high-efficiency energy systems. This article explores the principles, latest advancements, applications, and future of meta-materials in electronics.
Fundamental Properties of Meta-MaterialsMeta-materials exhibit unique behaviors that do not occur naturally, making them powerful tools for electronic applications. The fundamental properties include:
- Negative Refractive Index – Meta-materials can bend electromagnetic waves in the opposite direction compared to natural materials, leading to superlenses and improved signal processing in high-frequency circuits.
- Electromagnetic Bandgap (EBG) Control – They can be engineered to create selective frequency passbands and stopbands, essential for noise reduction and antenna design.
- Anisotropic Conductivity – The directional control of electrical conductivity enhances circuit efficiency and minimizes power losses.
- Subwavelength Focusing and Super-Resolution Imaging – Meta-material-based lenses enable imaging systems beyond the diffraction limit, essential for nanoscale electronics and photonics.
- Reconfigurability and Tunability – Meta-materials can dynamically alter their electromagnetic properties through external stimuli like electric fields, mechanical deformation, or temperature changes.
- Meta-Material-Based Antennas: Redefining Wireless Communication
Meta-material antennas have revolutionized modern communication by offering superior performance in terms of:
- Beam Steering and Beamforming – Adaptive beam control for 5G/6G networks, reducing interference and improving data throughput.
- Miniaturization – Compact, high-efficiency antennas for IoT devices and wearable electronics.
- Enhanced Signal Propagation – Meta-material coatings reduce transmission losses and improve signal strength in urban environments.
- Ultra-Sensitive Sensors Enabled by Meta-Materials
Meta-materials play a crucial role in the development of next-generation sensors due to their ability to enhance signal detection and sensitivity. Applications include:
- Terahertz Imaging Sensors – Meta-material-based terahertz sensors offer non-invasive, high-resolution imaging for security screening and medical diagnostics.
- Environmental and Chemical Sensors – Highly selective and sensitive sensors for detecting pollutants, gases, and biological agents.
- Wearable Biosensors – Low-power, high-sensitivity sensors integrated into smart textiles for continuous health monitoring.
- High-Efficiency Electronic Circuits and Power Systems
Meta-materials contribute significantly to the development of energy-efficient electronic systems by optimizing electromagnetic wave interactions. Advancements include:
- Meta-Material Waveguides – Improved signal integrity and reduced transmission losses in high-speed computing.
- Efficient Heat Dissipation Structures – Thermal meta-materials facilitate effective cooling solutions for microprocessors and power electronics.
- Energy Harvesting and Wireless Power Transfer – Meta-material-enhanced resonators improve efficiency in inductive and resonant coupling mechanisms.
- Quantum Meta-Materials for Next-Generation Computing
The intersection of meta-materials and quantum mechanics is paving the way for advanced computing and sensing technologies:
- Meta-Material Superconductors – Novel superconducting structures for ultra-low-power electronic circuits.
- Photonic Meta-Materials for Quantum Information Processing – Enabling the development of ultra-secure quantum communication systems.
- Meta-Material-Based Quantum Sensors – Providing unprecedented precision in gravitational wave detection and navigation systems.
- Optical and Display Technologies Enhanced by Meta-Materials
Meta-materials are enabling breakthroughs in next-generation display and imaging technologies:
- Meta-Surface Optics – Flat optical components that replace bulky lenses in AR/VR systems, reducing size and weight.
- Holographic and Transparent Displays – High-efficiency meta-materials enable immersive and transparent display technologies.
- Ultra-High-Resolution Imaging – Meta-material-based superlenses enhance biomedical imaging and industrial inspection.
- Programmable and Reconfigurable Meta-Materials
Meta-materials with dynamically adjustable properties are shaping adaptive electronic systems. Key innovations include:
- Electrically Tunable Meta-Surfaces – Enabling real-time beam steering for adaptive radar and LiDAR applications.
- Mechanically Reconfigurable Meta-Materials – Structures that change optical or electromagnetic responses under mechanical stress.
- Smart Meta-Materials – AI-integrated meta-materials that self-optimize based on environmental conditions.
- Integration of Nano-Meta-Materials with Semiconductor Technologies
Advances in nano-fabrication techniques are allowing seamless integration of meta-materials with semiconductor devices:
- Meta-Transistors – Leveraging meta-material principles for ultra-fast and low-power electronic components.
- Nano-Photonics and Plasmonic Circuits – Ultra-efficient photonic chips utilizing meta-materials for high-speed data transfer.
- Graphene-Based Meta-Materials – Harnessing the exceptional conductivity and flexibility of graphene for futuristic electronic applications.
- Sustainable and Biodegradable Meta-Materials
The push for environmentally friendly electronics has led to the exploration of sustainable meta-materials:
- Eco-Friendly Dielectrics – Reducing toxic waste in electronic components.
- Self-Healing Meta-Materials – Extending the lifespan of electronic devices through material self-repair mechanisms.
- Recyclable and Bio-Compatible Meta-Materials – Ensuring minimal environmental impact in electronic waste management.
Despite their promising applications, several challenges remain:
- High Fabrication Complexity and Cost – Advanced manufacturing techniques are required for precise structural control at the nanoscale.
- Material Stability and Durability – Long-term reliability of meta-material structures needs improvement for commercial deployment.
- Scalability and Mass Production – Efficient large-scale production processes are needed to bring meta-material-based devices to the mainstream market.
- Regulatory and Standardization Issues – The integration of meta-materials in critical electronic systems requires adherence to safety and performance standards.
The future of meta-materials in electronics is bright, with potential game-changing innovations:
- AI-Driven Meta-Materials – Materials that self-learn and adapt to optimize electromagnetic performance dynamically.
- Hybrid Meta-Materials and Nanotechnologies – Combining nanotechnology, AI, and meta-materials to create next-generation electronic components.
- Bio-Inspired and Biomimetic Meta-Materials – Mimicking nature’s structures for energy-efficient and high-performance electronic applications.
- Space and Aerospace Applications – Lightweight, ultra-durable meta-materials for advanced communication and defense systems.
Meta-materials are driving the next wave of technological advancements in electronics by enabling unprecedented control over electromagnetic properties. From high-performance antennas and quantum computing applications to AI-driven reconfigurable circuits, these engineered materials hold the potential to reshape the future of technology. As fabrication techniques advance and challenges are addressed, meta-materials will be at the core of next-generation electronic devices, pushing the boundaries of efficiency, miniaturization, and new functionalities.
The post Meta-Materials in Electronics: Revolutionizing Next-Generation Devices appeared first on ELE Times.
OIF unites 35 member companies in interoperability demos at OFC
Сторінки
