Українською
  In English
Feed aggregator
Довідка про результати публічного громадського обговорення проєкту Професійного стандарту Професіонал з енергетичного менеджменту
Розробником Національним технічним університетом України «Київський політехнічний інститут імені Ігоря Сікорського» відповідно до Порядку розроблення, введення в дію та перегляду професійних стандартів, затвердженого постановою Кабінету Міністрів України від 31.05.2017 р. № 373 (далі – Порядок), завершено процес публічного громадського обговорення проєкту Професійного стандарту «Професіонал з енергетичного менеджменту».
Altum RF achieves ISO 9001 registration for Sydney design center
Top 10 3D Printer Manufacturers in India
India’s 3D printing industry has experienced significant growth, with numerous companies emerging as key players in the field. Here’s an overview of the top 10 3D printer manufacturers in India as of 2025:
- Divide By Zero Technologies
Established in 2013 and based in Maharashtra, Divide By Zero Technologies is a prominent 3D printer manufacturer catering to small and medium enterprises. The company aims to make 3D printing affordable and reliable, providing solutions to renowned clients such as Samsung, L’Oreal, GE Healthcare, Godrej, and Mahindra. Their product lineup includes models like Accucraft i250+, Aion 500 MK2, Aeqon 400 V3, and Alpha 500. Notably, their patented Advanced Fusion Plastic Modeling (AFPM) technology ensures consistent quality through intuitive automation.
- Make3D
Founded in 2014 in Gujarat, Make3D specializes in manufacturing 3D printers and scanners. Their Pratham series caters to both hobbyists and industrial users, featuring models like Pratham Mini and Pratham 6.0. They also offer the Eka Star DLP Printer and EinScan Pro 2X scanner. Committed to enhancing the accessibility of additive manufacturing, Make3D provides products known for quality and durability, alongside educational courses on 3D printing.
- Mekuva Technologies (POD3D)
Based in Hyderabad and established in 2021, Mekuva Technologies offers a range of 3D printers, including the AKAR series (300 Pro, 600 Basic, 200 Desktop, and 200 Pro). Beyond manufacturing, they provide services like 3D design, printing, scanning, CNC machining, sheet metal operations, and injection molding, serving as a comprehensive solution provider for various industries. Their printers are compatible with materials such as PLA, ABS, and carbon fiber.
- IMIK Technologies
Operating since 2007 in Tamil Nadu, IMIK Technologies supplies a wide range of 3D printers, including their own FDM printer, IMIK 3DP, and models from brands like Creality, Flashforge, and Ultimaker. They cater to sectors such as defense, textiles, robotics, agriculture, and medicine, offering products suitable for educational, industrial, and personal use. Additionally, they provide 3D prototyping services.
- Printlay
Established in 2015 in Tamil Nadu, Printlay specializes in 3D printing and scanning services. They assist clients from prototyping to end-use parts production, ensuring precision and accuracy. Their services extend to CNC machining and injection molding, catering to diverse industries with a reputation for quick turnaround times and quality service.
- A3DXYZ
Founded in 2018 in Maharashtra, A3DXYZ offers 3D printing services, including FDM printing, stereolithography, CAD modeling, digital light processing, and vacuum casting. They serve industries such as architecture, aerospace, healthcare, and medicine, and have introduced the A3DXYZ DS200 3D printer, known for its robust design and high-quality output.
- Boson Machines
Based in Maharashtra and established in 2017, Boson Machines is a leading 3D printing manufacturer utilizing technologies like FDM, SLA, and SLS. They offer services such as part production, injection molding, and CNC machining, providing comprehensive solutions from design to production.
- 3Ding
Operating since 2013 in Tamil Nadu, 3Ding supplies a variety of 3D printers, PCB printers, printing materials, and scanners. They distribute products from brands like 3D Systems, Fab X, Voltera, Formlabs, and Creality, and offer rental options. Their services include 3D design, printing, and scanning, along with workshops and training programs. They have branches in Chennai, Bangalore, Hyderabad, and Mumbai.
- Precious 3D
Established in 2017 in Tamil Nadu, Precious 3D offers 3D design, printing, CNC machining, and injection molding services. They utilize technologies like SLS, FDM, DLP, and Polyjet, serving industries such as automotive and healthcare. Their clientele includes brands like Renault, Ford, Verizon, and Nippon Paint, and they provide consultation services for material selection.
- Imaginarium
Based in Mumbai, Imaginarium stands as India’s largest 3D printing and rapid prototyping company. They offer design validation, prototyping, batch production, and various techniques such as SLA (Stereolithography), SLS (Selective Laser Sintering), VC (Vacuum Casting), CNC machining, injection molding, and scanning. Serving industries such as jewelry, automotive, and healthcare, Imaginarium utilizes 20 industrial 3D printers and 140 different materials, making them a key player in the field.
These companies exemplify the rapid advancement and diversification of India’s 3D printing industry, offering a wide range of products and services to meet the evolving needs of various sectors.
The post Top 10 3D Printer Manufacturers in India appeared first on ELE Times.
For some reason, I just love doing this fancy shit. No one will probably ever see the PCB except me lol
![]() | submitted by /u/No_Pilot_1974 [link] [comments] |
ROHM launches 650V GaN HEMT in compact, high-heat-dissipation TOLL package
📢 Тиждень математики в КПІ ім. Ігоря Сікорського!
Тема Тижня математики в КПІ ім. Ігоря Сікорського у 2025 році - «Математика для всіх: математика, мистецтво та креативність»
🎥 Defense Expo Day в КПІ ім. Ігоря Сікорського
На початку травня спільно з Мінстратегпромом було проведено «Defense Expo Day. День кар'єри в оборонній сфері». Чудово, що саме наші студенти серед перших мають можливість спілкуватися з представниками провідних оборонних підприємства України, дізнаватися про можливості подальшої роботи у ОПК і допомоги державі!
How AI is changing the game for high-performance SoC designs

The need for intelligent interconnect solutions has become critical as the scale, complexity, and customizability of today’s systems-on-chip (SoC) continue to increase. Traditional network-on-chip (NoC) technologies have played a vital role in addressing connectivity and data movement challenges, but the growing intricacy of designs necessitates a more advanced approach. Especially, when high-end SoC designs are surpassing the human ability to create NoCs without smart assistance.
The key drivers for this demand can be summarized as follows:
- Application-specific requirements: Many industries and applications, such as automotive, Internet of Things (IoT), consumer electronics, artificial intelligence (AI), and machine learning (ML), require highly specialized hardware tailored to unique workloads, such as real-time processing, low latency, or energy efficiency. Off-the-shelf chips often fall short of providing the precise blend of performance, power, and cost-efficiency these applications need.
- Cost and performance optimization: Custom SoCs allow companies to integrate multiple functions into a single chip, reducing system complexity, power consumption, and overall costs. With advanced process nodes, custom SoCs can achieve higher levels of performance tailored to the application, offering a competitive edge.
- Miniaturization and integration: Devices in areas like wearables, medical implants, and IoT sensors demand miniaturized solutions. Custom SoCs consolidate functionality onto a single chip, reducing size and weight.
- Data-centric and AI workloads: AI and ML require processing architectures optimized for parallel computation and real-time inferencing. Custom SoCs can incorporate specialized processing units, like neural network accelerators or high-bandwidth memory interfaces, to handle these demanding tasks.
The market now demands a next-level approach, one that leverages AI and ML to optimize performance, reduce development time, and ensure efficient data movement across the entire system. Today’s high-end SoC designs are necessitating smarter, automated solutions to address evolving industry needs.
The solution is the introduction of a new type of smart NoC interconnect IP that can leverage smart heuristics using ML and AI technology to dramatically speed up the creation and increase the quality of efficient, high-performance SoC designs.
Today’s NoC technologies
Each IP in an SoC has one or more interfaces, each with its own width and frequency. A major challenge is the variety of standard interfaces and protocols, such as AXI, AHB, and APB, used across the industry. Adding to this complexity, SoCs often integrate IPs from multiple vendors, each with different interface requirements.
NoC technology helps manage this complexity by assigning a network interface unit (NIU) to each IP interface. For initiator IPs, the NIU packetizes and serializes data for the NoC. For target IPs, it de-packetizes and de-serializes incoming data.
Packets contain source and destination addresses, and NoC switches direct them to their targets. These switches have multiple ports, allowing several packets to move through the network at once. Buffers and pipeline stages further support data flow.
Without automation, designers often add extra switches, buffers, or pipeline stages as a precaution. However, too many switches waste area and power, excessive buffering increases latency and power use, and undersized buffers can cause congestion. Overusing pipeline stages also adds delay and consumes more power and silicon.
Existing NoC interconnect solutions provide tools for manual optimization, such as selecting topology and fine-tuning settings. However, they still struggle to keep pace with the growing complexity of modern SoCs.
Figure 1 SoC design complexity which has surpassed manual human capabilities, calls for smart NoC automation. Source: Arteris
Smart NoC IP
The typical number of IPs in one of today’s high-end SoCs ranges from 50 to 500+, the typical number of transistors in each of these IPs ranges from 1 million to 1+ billion, and the typical number of transistors on an SoC ranges from 1 billion to 100+ billion. Furthermore, modern SoCs may comprise between 5 to 50+ subsystems, all requiring seamless internal and subsystem-to-subsystem communication and data movement.
The result of all this is that today’s high-end SoC designs are surpassing human ability to create their NoCs without smart assistance. The solution is the introduction of a new type of advanced NoC IP, such as FlexGen smart NoC IP from Arteris. The advanced IP can leverage smart heuristics using ML technology to dramatically speed up the creation and increase the quality of efficient, high-performance SoC designs. A high-level overview of the smart NoC IP flow is illustrated in Figure 2.
Figure 2 A high-level overview of the FlexGen shows how smart NoC IP flow works. Source: Arteris
Designers start by using an intuitive interface to capture the high-level specifications for the SoC (Figure 2a). These include the socket specifications, such as the widths and frequencies of each interface. They also cover connectivity requirements, defining which initiator IPs need to communicate with which target IPs and any available floorplan information.
The designers can also specify objectives at any point in the form of traffic classes and assign performance goals like bandwidths and latencies to different data pathways (Figure 2b).
FlexGen’s ML heuristics determine optimal NoC topologies, employing different topologies for different areas of the SoC. The IP automatically generates the smart NoC architecture, including switches, buffers, and pipeline stages. The tool minimizes wire lengths and reduces latencies while adhering to user-defined constraints and performance goals (Figure 2c). Eventually, the system IP can be used to export everything for use with physical synthesis (Figure 2d).
NoC with smart assistant
The rapid increase in SoC complexity has exceeded the capabilities of traditional NoC design methodologies, making it difficult for engineers to design these networks without smart assistance. This has driven the demand for more advanced solutions.
Take the case of FlexGen, a smart NoC IP from Arteris, which addresses these challenges by leveraging intelligent ML heuristics to automate and optimize the NoC generation process. The advanced IP delivers expert-level results 10x faster than traditional NoC flows. It reduces wire lengths by up to 30%, minimizes latencies typically by 10% or more, and improves PPA metrics.
Streamlining NoC development accelerates time to market and enhances engineering productivity.
Andy Nightingale, VP of product management and marketing at Arteris, has over 37 years of experience in the high-tech industry, including 23 years in various engineering and product management positions at Arm.
Related Content
- SoC Interconnect: Don’t DIY!
- What is the future for Network-on-Chip?
- SoC design: When is a network-on-chip (NoC) not enough
- Network-on-chip (NoC) interconnect topologies explained
- Why verification matters in network-on-chip (NoC) design
The post How AI is changing the game for high-performance SoC designs appeared first on EDN.
STMicroelectronics enables unmatched edge AI performance on MCU with STM32N6
In an era where artificial intelligence (AI) is rapidly transforming edge computing, STMicroelectronics is leading the charge with its groundbreaking STM32N6 series, featuring the Neural-ART Accelerator. This next-generation microcontroller delivers 600 times more AI performance than previous STM32 MCUs, redefining real-time AI processing for embedded systems.
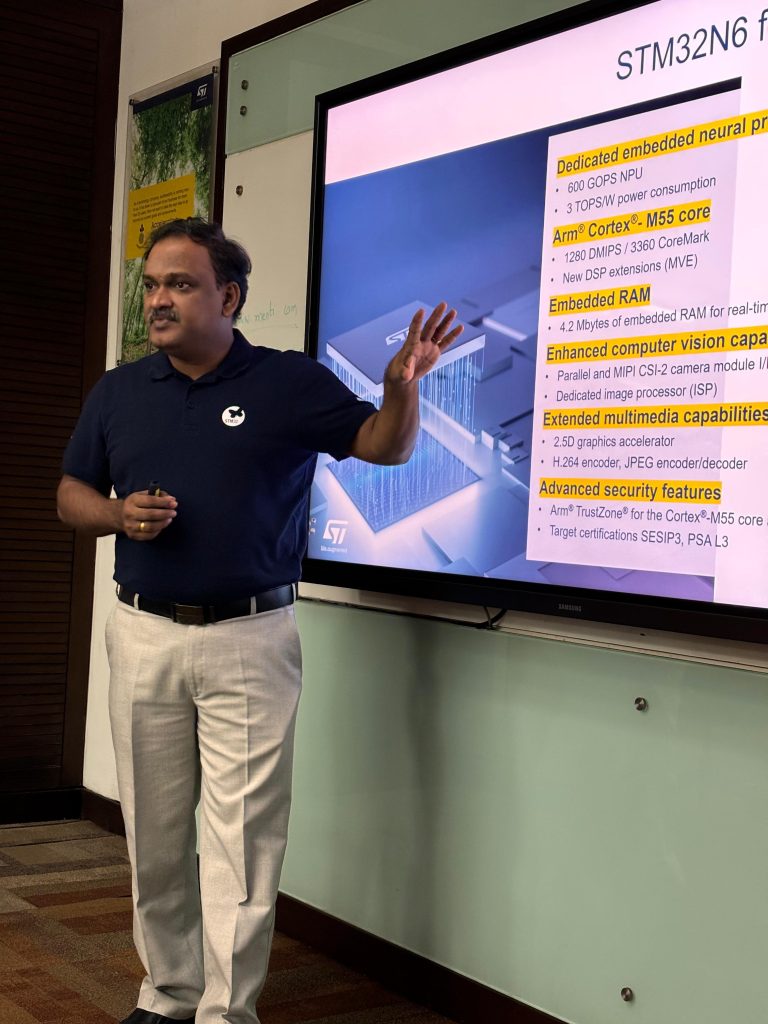
In this exclusive interview, Rashi Bajpai from ELE Times sits down with Sridhar Ethiraj, Technical Marketing – General Purpose MCU at STMicroelectronics India, to explore the technological breakthroughs behind the STM32N6. We discuss the challenges of integrating high-performance AI with ultra-low power consumption, the real-world impact of AI-accelerated MCUs in industries like automotive, healthcare, and smart devices, and how ST’s Edge AI Suite is simplifying AI deployment for developers worldwide.
With industry giants like LG, Lenovo, and Alps Alpine already leveraging the STM32N6, this conversation unveils how AI-powered microcontrollers are shaping the future of intelligent embedded systems.
Excerpts:
STMicroelectronics has introduced the STM32N6 MCU with the Neural-ART Accelerator, delivering 600 times more machine-learning performance than previous high-end STM32 MCUs. What key challenges did ST overcome to integrate such advanced AI capabilities into a microcontroller while maintaining power efficiency?
Ans: STMicroelectronics faced several key challenges while integrating the Neural-ART Accelerator into the STM32N6 MCU. The need for high computing power for advanced AI features clashed with power efficiency goals was a major hurdle. ST tackled this by creating its own neural processing unit (NPU) to handle most AI tasks while keeping power use low. Making the system work with different AI frameworks and models also proved tough, but ST fixed this by supporting common frameworks like TensorFlow Keras, and the ONNX ecosystem. ST also had to tweak the hardware to run neural networks for computer vision and audio in real-time. This meant building a computer vision pipeline and special image processing abilities. In the end, all this work resulted in the STM32N6 MCU, which offers 600 times better machine-learning performance than earlier top-end STM32 MCUs, while still being very power-efficient.
With AI inference moving to the edge, how does the STM32N6 differentiate itself from other AI-enabled MCUs in terms of performance, memory, and AI software support?
Ans: The STM32N6 series redefines AI-enabled microcontrollers with its Neural-ART Accelerator, a custom neural processing unit (NPU) delivering up to 600 GOPS for real-time neural network inference. Built on the Arm Cortex-M55 core running at 800 MHz, it leverages Arm Helium vector processing to enhance DSP performance. With 4.2 MB of built-in RAM and high-speed external memory interfaces, it excels in AI and graphics-intensive applications. Backed by a comprehensive AI software ecosystem—including STM32Cube.AI, ST Edge AI Developer Cloud, and the STM32 model zoo—it simplifies model optimization and deployment. This seamless blend of hardware acceleration and software support makes the STM32N6 a powerful and scalable solution for edge AI workloads.
The STM32N6 has been tested and adopted by industry leaders like LG, Lenovo, and Alps Alpine. Can you share some real-world applications where this MCU is making a significant impact?
Ans: The STM32N6 MCU is driving innovation across multiple industries. In automotive, it powers advanced driver assistance systems (ADAS) by enabling real-time processing of camera and sensor inputs for collision avoidance and lane-keeping. In smart home technology, companies like LG and Lenovo use it in security cameras and smart doorbells, leveraging its AI capabilities for motion detection and facial recognition. In healthcare, it enhances medical devices by accurately processing patient data for diagnostics and continuous monitoring. These real-world applications highlight how the STM32N6 delivers high-performance AI processing, improving safety, efficiency, and user experience across industries.
AI at the edge is evolving rapidly, particularly in vision, audio processing, and sensor-based analytics. How does ST’s Edge AI Suite support developers in optimizing AI models for the STM32N6, and what industries stand to benefit the most from this innovation?
Ans: Through three main tools in the Edge AI Suite from ST, developers gain complete functionality to improve AI models for the STM32N6 platform: STM32Cube.AI and ST Edge AI Developer Cloud and STM32 model zoo. The tools in this platform optimize AI model deployment on the Neural-ART Accelerator of STM32N6 while supporting the entire process from data preparation to code generation. The STM32N6 has the potential to revolutionize multiple sectors including automotive production, automotive components and consumer electronics together with healthcare and industrial automation markets. The STM32N6 allows advanced driver assistance systems (ADAS) in automotive applications as it provides healthcare products with real-time data analysis capabilities. Through their suite developers can build effective edge AI solutions which operate throughout numerous applications.
Looking ahead, how does STMicroelectronics envision the future of AI-accelerated microcontrollers, and what role will the STM32N6 series play in shaping next-generation embedded systems?
Ans: STMicroelectronics envisions a future where AI-accelerated microcontrollers like the STM32N6 series play a pivotal role in edge computing, enabling smarter, more efficient, and autonomous embedded systems. The STM32N6, with its Neural-ART Accelerator, is designed to handle complex AI tasks such as computer vision and audio processing with exceptional efficiency. Its energy-optimized AI processing will drive advancements across automotive, healthcare, consumer electronics, and industrial automation, enabling real-time data analysis, improved user experiences, and enhanced operational efficiency. As AI at the edge continues to evolve, the STM32N6 series will be instrumental in shaping intelligent, responsive, and secure next-generation embedded systems.
Sources:
STMicroelectronics to boost AI at the edge with new NPU-accelerated STM32 microcontrollers – ST News
STM32N6 series – STMicroelectronics
STM32N6-AI – AI software ecosystem for STM32N6 with Neural-ART accelerator – STMicroelectronics
Microcontrollers-stm32n6-series-overview.pdf
The post STMicroelectronics enables unmatched edge AI performance on MCU with STM32N6 appeared first on ELE Times.
EEVblog 1673 - JBL Partybox 310 Repair - Part 2 (SPOILER)
Diy 3 channel equalizer. First audio project
![]() | submitted by /u/gdma2004 [link] [comments] |
EEVblog 1672 - JBL REPAIR: You'll never guess the fault!
A pitch-linear VCO, part 1: Getting it going

Editor’s Note: This DI is a two-part series.
Part 1 shows how to make an oscillator with a pitch that is proportional to a control-voltage.
Part 2 will show how to modify the circuit for use with higher supply voltages, implement it using discrete parts, and modify it to closely approximate a sine wave.
Typical circuitAn ongoing project (or gadget) called for a means of generating an audio output to represent a varying voltage level. Ho hum: that sounds like a voltage-controlled oscillator. But this signal was bipolar, spanning peaks ranging from -1 to +1 V. A linear-in-frequency response just sounded wrong, and anyway could never deliver the symmetrical ±1-octave output that I wanted.
Wow the engineering world with your unique design: Design Ideas Submission Guide
A typical, well-known type of oscillator—though as drawn, lacks voltage control—is shown in Figure 1. At the start of a cycle, C1 is fully charged. It then discharges through R1 until the reference voltage, shown as mid-rail, is reached, when the monostable multivibrator is triggered, delivering a pulse to turn on Q1, which shorts C1 to the positive rail, thereby starting the next cycle. The output, an exponentially-decaying sawtooth having constant amplitude, is taken from the top of C1 via a buffer (not shown). (Strictly, the op-amp should be a comparator; it’s used as one.) C1 would normally be switched for different ranges, with R1 varied for tuning.
Figure 1 A typical relaxation oscillator with an exponentially decaying sawtooth output, is the starting point for this design.
Another method of tuning this is to keep R1 and C1 constant and vary the reference voltage. The output level now varies, the tuning law being exponential. If we want pitch-linearity, maybe that would be a good starting point?
TweakingAn exponential decay may not give the exact curve we need, but with a little tweaking, parts of it are close enough to be useful. Some experimenting produced the workable circuit shown in Figure 2.
Figure 2 Varying the reference voltage instead of the R-C time-constant gives a tuning law that is close enough to being linear in pitch over a couple of octaves, especially after adding R2.
Just as described above, the bipolar control voltage is compared with the falling exponential(-ish) ramp to tune the oscillator’s frequency. When they coincide, U2a, used as a multi-supply multi-voltage (MSMV), is triggered to produce a reset pulse to turn Q1 on momentarily, thus resetting C1’s voltage to its maximum value. Figure 3 shows the key waveforms.
Figure 3 Waveforms from the circuit in Figure 2, at both extremes of its two-octave span.
Bending the law so we can do what we wantThe single, simple, humble resistor R2 is the key to this design. By compressing and shifting the exponential decay curve, it allows a reasonably close approximation to a tuning law that is linear with pitch rather than frequency over a couple of octaves and more: an increment in the control voltage now changes the frequency by a fairly constant frequency ratio rather than a fixed amount. The match is worst at the low-frequency end, being around 5% off close to the low calibration point and way off even lower down. (A semitone is ~7%.) Using 51k for R2 gives the closest match for the bottom octave frequency itself, but 56k generally “sounds” better on average in that region.
With the values shown, the output frequency ranges from about 250 Hz to 1000 Hz for inputs from -1 to +1 V, which is close to the two octaves upwards from “C4” (middle C: ~262 Hz if we define A4 to be precisely 440 Hz) to “C6”. (The quotes are used here to distinguish pitch values from capacitors!) For different spans, just change C1 or both R1 and R2, whose ratio must be kept constant. If the control voltage falls below about -1.5 V, as determined by R1 and R2, oscillation will stop. Above +1 V, the match is still reasonable for another half octave and more.
U2b divides the oscillator’s pulse output by 2 to give a square wave, which the output network turns into a trapezoid of about 1.1 V pk-pk (~-6 dBu). While this has no pretensions to waveform purity, it does now have softer and “more analog” edges rather than sharp digital ones.
Other comments: MCP6002s are cheap and cheerful. The MCP6022 is better specified (much faster, and with <500 µV input offset) but more costly. The spare half of U1 could be used for further filtering of the output if desired. The spec for Q1 is not critical. A ZVP3306A has an RDS(ON) of up to 15 Ω, but the width of the pulse driving its gate ensures that C1 is fully charged under all conditions. The ~±1 V control range was just what I wanted, but that was a happy accident rather than being designed in.
It now does what’s needed and is ready for dropping into the project (or gadget). However, . . .
A few extra components give more octaves and accuracyContemplating the basic circuit threw up an interesting idea. Linear-in-frequency tuning can be done in two ways, one being to use a linear ramp and vary the control voltage much as we’re doing with the exponential one, while the other would be to replace R1 with a controllable current sink and delete R2. Use these together and the tuning law becomes “squared”, giving a power law that is inherently much closer to being linear-in-pitch. Figure 4 shows how to do that.
Figure 4 Adding a voltage-controlled current sink in place of tuning resistor R1 is the key to operation over more than 4 octaves with much better pitch accuracy.
Q2, U1b, and R1 form the current sink. Its control voltage is half of that at the input, ensuring that Q2 never saturates. C1 discharges linearly, the slope being governed by Vcon. The power rails are shown as 0 V / +5 V rather than ±2.5 V to reflect the wider tuning range, but the output frequency is still centered at around 520 Hz (close to a pitch of “C5”) with the component values shown.
The required control-voltage swing now measures ~840 mV/octave (or ~70 mV/semitone). The response is almost exactly linear-in-pitch over the middle two octaves, and still decent for the two octaves and more surrounding those. The errors are worst at the low-frequency end because the current sink is then running out of steam (or electrons). An MCP6022 is used because of its better performance but the rest of the circuit is almost unchanged.
While the range of 4-plus octaves is over the top for my target application, improved accuracy is always welcome, and this better performance opens the way to possible musical use.
In Part 2, that will be shown, but first we’ll see how to modify the circuit for use with higher supply voltages, how to implement it using only discrete parts apart from the op-amp, and how to end up with a respectable sine wave at the output.
—Nick Cornford built his first crystal set at 10, and since then has designed professional audio equipment, many datacomm products, and technical security kit. He has at last retired. Mostly. Sort of.
Related Content
- VCO using the TL431 reference
- Ultra-low distortion oscillator, part 1: how not to do it.
- How to control your impulses—part 1
- Squashed triangles: sines, but with teeth?
- Simple 5-component oscillator works below 0.8V
- A two transistor sine wave oscillator
The post A pitch-linear VCO, part 1: Getting it going appeared first on EDN.
CSA Catapult hosts UK government ministers and South Wales’ compound semiconductor cluster
Top 10 Industrial Robot Manufacturers in India
India’s industrial landscape is undergoing a significant transformation, with robotics playing a pivotal role in enhancing manufacturing efficiency, precision, and productivity. Several Indian companies have emerged as leaders in industrial robotics, offering innovative solutions tailored to various sectors. Here are ten notable industrial robot manufacturers in India:
- DiFACTO Robotics
Headquartered in Bengaluru, DiFACTO Robotics is a prominent provider of robotic solutions for the manufacturing sector. Their expertise encompasses conceptualizing, manufacturing, and implementing advanced factory automation systems. Serving industries such as automotive, metal forming, transportation, energy, electronics, and consumer goods, DiFACTO has established itself as a key player in India’s industrial automation landscape.
- Hi-Tech Robotic Systemz
Hi-Tech Robotic Systemz specializes in autonomous mobile robots and automated guided vehicles (AGVs). Their solutions cater to sectors like automotive, warehousing, and defense, focusing on enhancing operational efficiency and safety. With a strong emphasis on research and development, Hi-Tech Robotic Systemz continues to innovate in the field of industrial robotics.
- Gridbots
Based in Ahmedabad, Gridbots is known for developing robots and artificial intelligence systems for industrial applications. Their product portfolio includes robotic arms, vision systems, and automation solutions designed to optimize manufacturing processes. Gridbots’ commitment to innovation has positioned them as a significant contributor to India’s robotics industry.
- Systemantics
Systemantics focuses on designing and manufacturing industrial robots that are cost-effective and easy to deploy. Their flagship product, the ASYSTR 600, is a six-axis industrial robot designed for tasks such as material handling, welding, and assembly. By addressing the challenges of automation adoption, Systemantics aims to make robotics accessible to a broader range of industries.
- Invento Robotics
Invento Robotics specializes in service robots with applications in hospitality, healthcare, and retail. Their robots, such as Mitra, have been deployed in various settings to assist with customer engagement and service delivery. While their primary focus is on service robotics, their technological advancements contribute to the broader robotics ecosystem in India.
- Addverb Technologies
Addverb Technologies is a leading provider of automation solutions for warehouses and distribution centers. Their robotics offerings include autonomous mobile robots (AMRs), sorting robots, and pallet shuttles, designed to streamline intralogistics operations. By integrating robotics with advanced software systems, Addverb enhances efficiency and accuracy in supply chain processes.
- CynLr
CynLr (Cybernetics Laboratory) focuses on developing vision systems and robotic solutions that enable machines to handle objects with human-like dexterity. Their technology addresses complex manufacturing challenges, particularly in tasks requiring precision and adaptability. CynLr’s innovations are paving the way for more versatile industrial automation.
- PARI (Precision Automation and Robotics India)
Founded in 1991 and headquartered in Satara, Maharashtra, PARI is a global automation company that has provided over 3,000 automated solutions worldwide. Their services encompass conceptualizing, manufacturing, and implementing advanced factory automation systems, catering to industries such as automotive, aerospace, and heavy engineering.
- Goat Robotics
Based in Coimbatore, Goat Robotics specializes in autonomous mobile robots (AMRs) designed for manufacturing industries. Their robots are equipped with advanced navigation systems and are used for material transport and logistics within industrial settings. Goat Robotics’ solutions aim to enhance operational efficiency and safety in manufacturing environments.
- Peer Robotics
Peer Robotics is a startup focusing on collaborative mobile robots designed to work alongside human operators. Their robots are used in manufacturing and warehousing environments to assist with material handling and repetitive tasks. By emphasizing human-robot collaboration, Peer Robotics aims to create safer and more efficient workplaces.
India’s industrial robot manufacturing sector is characterized by a blend of established companies and innovative startups, each contributing uniquely to the automation landscape. As industries increasingly adopt automation to enhance productivity and competitiveness, these companies are poised to play a crucial role in shaping the future of manufacturing in India.
The post Top 10 Industrial Robot Manufacturers in India appeared first on ELE Times.
DigiKey statement on tariffs
![]() | submitted by /u/cosmicrae [link] [comments] |
Top 10 Drone Camera Manufacturers in India
India’s drone industry has experienced remarkable growth, positioning itself as a global leader in unmanned aerial vehicle (UAV) technology. This surge is driven by the government’s “Make in India” initiative and supportive policies, fostering a robust ecosystem of drone manufacturers. Here, we explore the top 10 drone camera manufacturers in India, highlighting their contributions to this dynamic sector.
- ideaForge Technology
Founded in 2007, ideaForge is a pioneer in India’s UAV industry, renowned for developing high-endurance drones tailored for defense, homeland security, and industrial applications. Their flagship product, the Switch UAV, boasts a flight time of over two hours, equipped with advanced imaging capabilities, making it indispensable for long-range surveillance and mapping. The company’s commitment to innovation has solidified its position as a leader in the Indian drone market.
- Zen Technologies
Established in 1993, Zen Technologies specializes in designing and manufacturing combat training solutions, including UAVs and anti-drone systems. Their drones are integral to military training, offering realistic simulations and live training exercises. The company’s focus on defense applications has made it a trusted partner of the Indian armed forces.
- Paras Defence and Space Technologies
Paras Defence is a prominent player in the defense sector, providing a range of products, including UAVs equipped with sophisticated imaging systems. Their drones are engineered for intelligence, surveillance, and reconnaissance missions, featuring high-resolution cameras and thermal imaging capabilities. The company’s expertise in optics and defense electronics enhances the performance of their UAVs.
- Asteria Aerospace
Based in Bengaluru, Asteria Aerospace focuses on developing drones for security and industrial applications. Their Genesis series offers real-time aerial surveillance with advanced imaging systems, catering to sectors like oil and gas, mining, and agriculture. The company’s emphasis on data analytics and automation sets them apart in the industry.
- Quidich Innovation Labs
Quidich specializes in aerial cinematography and has expanded into industrial inspections and mapping. Their drones are equipped with high-definition cameras, providing unique perspectives for film production and critical data for infrastructure assessments. Their versatility has made them a preferred choice in both entertainment and industrial sectors.
- Garuda Aerospace
Garuda Aerospace offers a diverse range of drones for applications such as agriculture, delivery, and surveillance. Their Kisan Drone is designed for precision agriculture, featuring multispectral imaging to monitor crop health. The company’s focus on affordability and functionality has made drone technology accessible to various industries.
- Dhaksha Unmanned Systems
Specializing in agriculture and surveillance drones, Dhaksha Unmanned Systems provides UAVs equipped with advanced imaging systems for crop monitoring and security applications. Their drones are known for durability and ease of use, benefiting farmers and law enforcement agencies alike.
- RattanIndia Enterprises
RattanIndia has ventured into the drone sector, focusing on logistics and delivery solutions. Their drones are designed to transport goods efficiently, equipped with cameras for navigation and monitoring. The company’s entry into the drone market signifies the expanding applications of UAV technology in India.
- DCM Shriram Industries
DCM Shriram has diversified into drone manufacturing, offering UAVs for industrial inspections and agricultural use. Their drones are equipped with high-resolution cameras and sensors, providing valuable data for maintenance and farming operations. The company’s industrial expertise enhances the reliability of their drone solutions.
- Aeroarc Innovations
Aeroarc Innovations is an emerging player in India’s drone ecosystem, specializing in high-performance UAVs for industrial, defense, and environmental applications. Their drones feature advanced imaging capabilities, including multispectral and LiDAR sensors, making them ideal for precision agriculture, infrastructure monitoring, and disaster response. The company is focused on developing AI-powered drone solutions that enhance automation and real-time data analysis, positioning itself as a key innovator in the Indian drone market.
The advancements made by these companies reflect India’s burgeoning capabilities in drone technology. With applications spanning defense, agriculture, industrial inspections, and entertainment, the integration of advanced imaging systems into UAVs is transforming traditional practices. As regulatory frameworks evolve and technology advances, these manufacturers are poised to play a pivotal role in the global drone ecosystem, showcasing India’s commitment to innovation and self-reliance in this cutting-edge field.
The post Top 10 Drone Camera Manufacturers in India appeared first on ELE Times.
Multi-sense MCU enables new HMI and sensing use cases

A new microcontroller featuring multi-sense capabilities claims to enable new human-machine interface (HMI) and sensing solutions, ranging from sleek metallic product designs with touch-on metal buttons to waterproof touch buttons. Infineon’s PSOC 4 is an Arm Cortex-M0+-based MCU that offers capacitive, inductive, and liquid sensing in a single device.
Figure 1 PSOC 4 integrates capacitive, inductive, and liquid sensing to accommodate a variety of HMI uses cases. Source: Infineon
This new MCU combines the company’s fifth-generation capacitive sensing technology, CAPSENSE, with inductive and liquid sensing to optimize performance, enable new use cases, and realize cost savings. For a start, the fifth-generation CAPSENSE featuring always-on capability enables sensing at 10x lower power consumption and offers a 10x higher signal-to-noise ratio (SNR) than previous devices.
Figure 2 Capacitive sensing (left) and inductive sensing (right) complement each other to enable new HMI and sensing use cases. Source: Infineon
Inductive sensing is based on a proprietary methodology that is less sensitive to noise; it complements capacitive sensing to enable new HMI use cases like touch-over-metal, force touch surfaces, and proximity sensing. This allows developers to create modern, metal-based and waterproof designs with sleek form factors such as metal touch buttons on refrigerators or robust HMI for underwater devices such as cameras and wearables.
Then there is non-invasive and non-contact liquid sensing, which employs an AI/ML algorithm to facilitate more cost-effective and accurate sensing than mechanical sensors and typical capacitive solutions. Liquid sensing is resistant to environmental factors like temperature and humidity and can detect liquid levels with up to 10-bit resolution in various container shapes.
As a result, it offers capabilities—such as foam and residue rejection and reliably working with varying air gaps between sensor and container—that other liquid sensors don’t support. So, liquid sensing on PSOC 4 can efficiently manage liquids in robot vacuum cleaners, washing machines, coffee machines, and humidifiers.
Figure 3 PSOC 4 multi-sense eliminates the need for a sensor in a liquid and is insensitive to process variations like gaps between sensor and container. Source: Infineon
Finally, CAPSENSE hover touch sensors enable applications that benefit CAPSENSE from having an air gap between the sensor and the touch surface. It leverages highly sensitive capacitive sensing capability to detect touch interactions from a significant distance. That eliminates the need for the gap to be bridged using a conductive material, typically a spring or conductive foam.
Figure 4 Hover touch sensing comes into play when a direct touch of a button is not required. Source: Infineon
PSOC 4000T with fifth-generation CAPSENSE and multi-sense capability is available now. Another MCU in PSOC 4 family, PSOC 4100T Plus, offering higher memory and more I/Os, will be available in the second quarter of 2025.
Related Content
- Haptic HMI for Reliability with Magnetic Sensors
- Poor Automotive HMI Design to Impact Euro NCAP Safety Rating
- Revolutionizing automotive HMI design through capacitive sensing
- New Functional Safety Ready MCU Features Real-Time Control and HMI
- Intuitive HMI designs – microcontroller solutions optimized for touch and display control
The post Multi-sense MCU enables new HMI and sensing use cases appeared first on EDN.
📢 Другий відкритий інженерний конкурс для школярів «Збудуй свою МРІЮ»
📢 Запрошуємо взяти участь у Другому відкритому інженерному конкурсі для школярів «Збудуй свою МРІЮ» учнів 8-11 класів
NEPCON JAPAN 2025 Welcomes 85,430 Attendees for a Grand Showcase of Electronics R&D and Innovation
NEPCON JAPAN 2025 concluded its successful run at Tokyo Big Sight. The
event attracted a remarkable 85,430* attendees from around the globe, serving as a premier, world-class platform for innovation, networking, and business growth.
(*including concurrent shows)
This year’s edition brought together key industry players and the latest technologies across
multiple shows, including the 17th AUTOMOTIVE WORLD, the 11th Wearable Expo, Factory
Innovation Week 2024, and the 4th SMART LOGISTICS Expo.
The global reach and influence of NEPCON JAPAN was evident through the participation of
industry-leading exhibitors hailing from countries such as Austria, Estonia, Germany, the Czech Republic, Italy, the United States, Malaysia, and many more.
Industry Leaders and Global Participation
The exhibition halls were packed with cutting-edge technologies and breakthrough innovations presented by some of the biggest names in the industry. These companies, among 1,711 exhibitors, showcased state-of-the-art advancements in power devices, AI-driven automation, IoT solutions, next-gen mobility, and smart logistics technology.
Notable exhibitors included:
- NEPCON JAPAN: Yamaha Motor Co., Ltd., Omron Corporation, Siemens EDA Japan, Panasonic Corporation, Denso Corporation
- AUTOMOTIVE WORLD: Bosch Corporation, Continental AG, Denso Corporation, Aisin Seiki Co., Ltd., Toyota Auto Body
- Factory Innovation Week: LG Electronics Japan Inc., Mitsubishi Electric Corporation, Siemens AG, Fanuc Corporation, Kawasaki Heavy Industries, Ltd., Yaskawa Electric Corporation, Toshiba Digital Engineering Corporation
- SMART LOGOSTICS Expo: Honeywell International Inc., Daifuku Co., Ltd., Toyota Logistics Solutions, Murata Manufacturing Co., Ltd., Zebra Technologies Corporation
- WEARABLE EXPO:Lenovo Japan LLC, Sony Corporation, Samsung Electronics Co., Ltd., Google LLC, HTC Corporation, NXP Semiconductors N.V.
Event Highlights
One of the major attractions of NEPCON JAPAN 2025 was the expanded Power Device & Module Expo and the Power Device Summit, featuring discussions by leading power device manufacturers. Attendees also had access to a range of free-to-attend conference sessions, where industry leaders from Samsung, Intel, Qualcomm, and other major players shared insights on the future of electronics and R&D.
Build on NEPCON Japan’s Success: Register for the First-Ever NEPCON Osaka
Following the success of NEPCON Japan 2025, the inaugural edition of NEPCON Osaka is set to take place from May 14–16, 2025, further strengthening Japan’s presence in the electronics industry. Expected to welcome 45,000* visitors and 600* exhibitors, NEPCON Osaka will provide a new platform for business expansion and industry growth.
With yet another remarkable edition in the books, NEPCON JAPAN continues to set the standard for electronics innovation, R&D, and manufacturing excellence. Industry professionals, exhibitors, and tech enthusiasts alike can look forward to the next milestone event at NEPCON Osaka 2025.
The post NEPCON JAPAN 2025 Welcomes 85,430 Attendees for a Grand Showcase of Electronics R&D and Innovation appeared first on ELE Times.
Pages
